Moving forward with sustainable concrete building
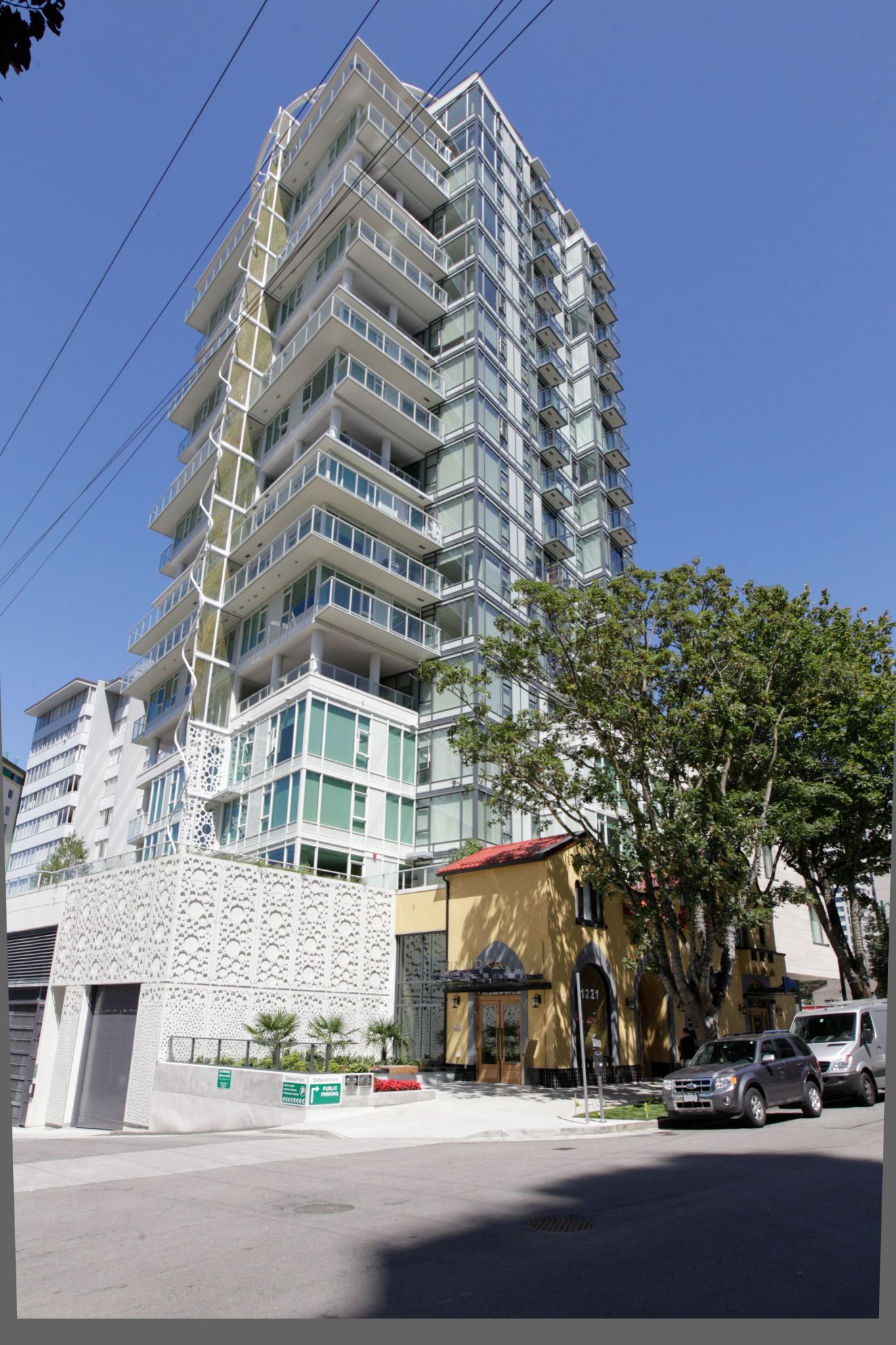
By Alireza Biparva, B.Sc., M.A.Sc.
The focus on sustainability continues to grow within the construction industry. However, one of the greatest global concerns is the uncertainty of natural resources.
P.K. Mehta’s book Concrete: Microstructure, Properties, and Materials suggests sustainability should be targeted by using products and materials that do not put a drain on dwindling resources or harm the ruptured environment, but also last the sands of time.1
According to the Canada Green Building Council (CaGBC), buildings generate:
- up to 35 per cent of all greenhouse gas (GHG) emissions;
- 35 per cent of landfill waste as a direct result of construction and demolition activities; and
- 80 per cent of water consumption in and around buildings.2
These statistics speak to the importance of designing buildings based on green initiatives to positively impact the environment. Thus, the standard of creating and building sustainable structures is a charge design professionals must account for within construction projects before a single drop of concrete is poured, or the first nail connects the foundation form. The goal set by programs such as the Leadership in Energy and Environmental Design (LEED) is to build structures based on the notion of sustainability.
In truth, if the goal is to deter the rapid forward thrust of climate change on the planet, the greenest and most sure-fire way to ensure its safety is to not build at all; unfortunately, this is not entirely feasible. The fact remains new structures are required to suffice the growing global population. Further, Mehta states:
at the beginning of the 20th century, the world population was 1.5 billion, with only 10 per cent living in cities. By the end of the 20th century the population had risen to six billion, with over 50 per cent city dwellers. To put a little perspective on this population growth, it took the human race 10,000 years after the last ice age for the population to rise to the 1.5-billion mark.
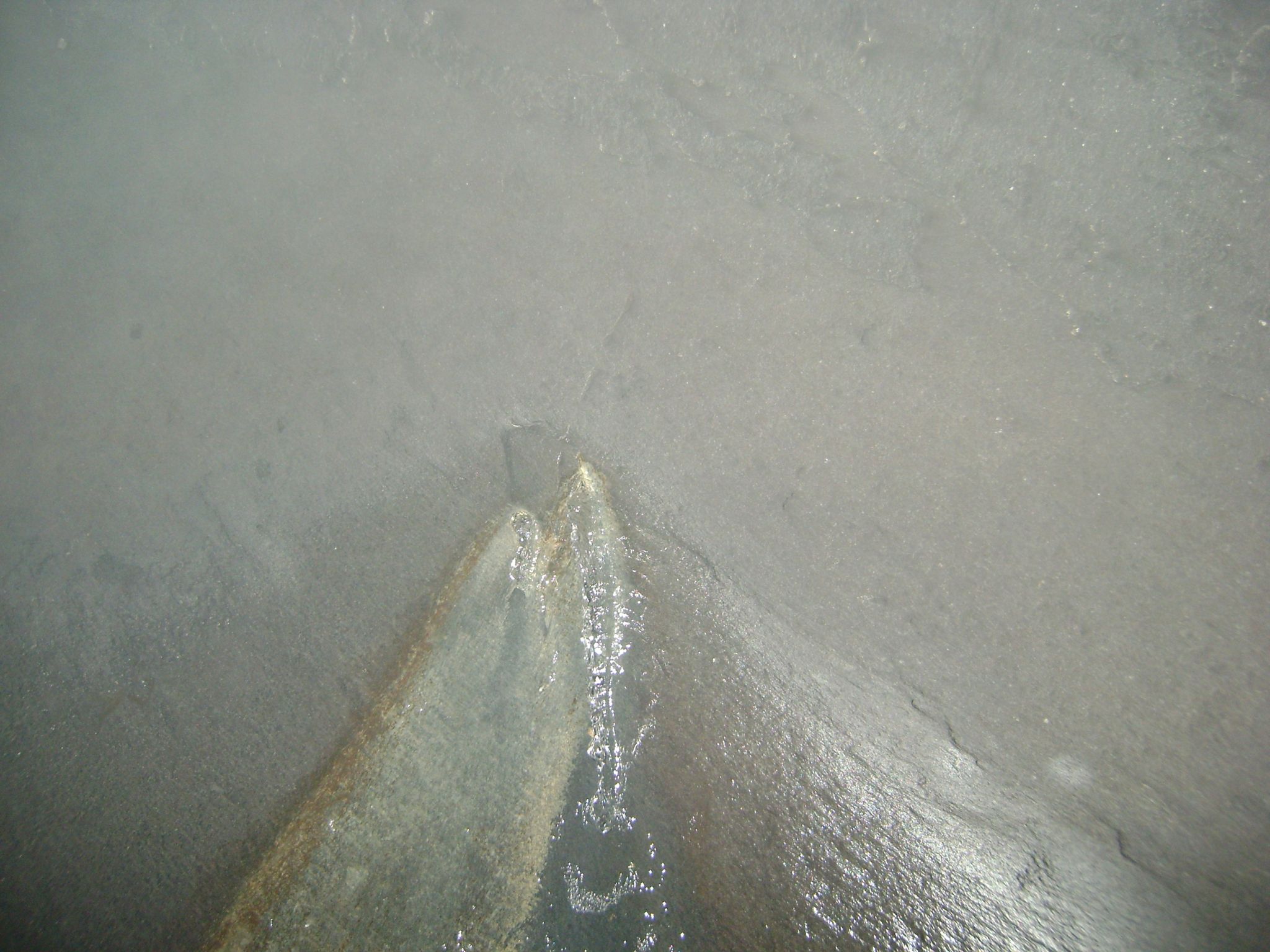
However, many technology choices have turned out to be wasteful and harmful to the planet, creating for the short-term instead of the long-term goals of the global collective. According to Mehta, only six per cent of the total global flow of materials actually ends up in consumer products, whereas much of the virgin materials are being returned to the environment in the form of harmful solid, liquid, and gaseous wastes. To sober that statistic further, this refers to about six per cent of 500 billion tonnes generated a year.
Concrete usage
According to the World Business Council for Sustainable Development, concrete is the most used manufactured material in the world. In fact, twice as much concrete is used around the world than the total of all other building materials combined, including wood, steel, plastic, and aluminum.3
According to a 2007 United States Geological Survey, “Minerals Commodity Summary–Cement,” nearly 3000 kg (6613 lb) of concrete is used for every man, woman, and child on the planet every year.4 This means about 8.2 kg (18 lb) of concrete is being used daily for every inhabitant on Earth, translating into 0.34 kg (0.75 lb) of concrete per hour. It is astounding to think in the time it takes to read this article—approximately six minutes—there is 238 million kg (238,000 tonnes) of concrete being poured worldwide.
The reason concrete is used so readily is because few other materials can match it in terms of effectiveness, price, and performance for most purposes. Further, concrete can be durable, is easily installed, and can limit the negative environmental effects more than other major building materials. Concrete is also easy to procure, as in its simplest form is made of three main ingredients: water, portland cement, and aggregates. Water is all around us, coarse and fine aggregate can be found in numerous quarry locations around the world, and cement is also readily available.
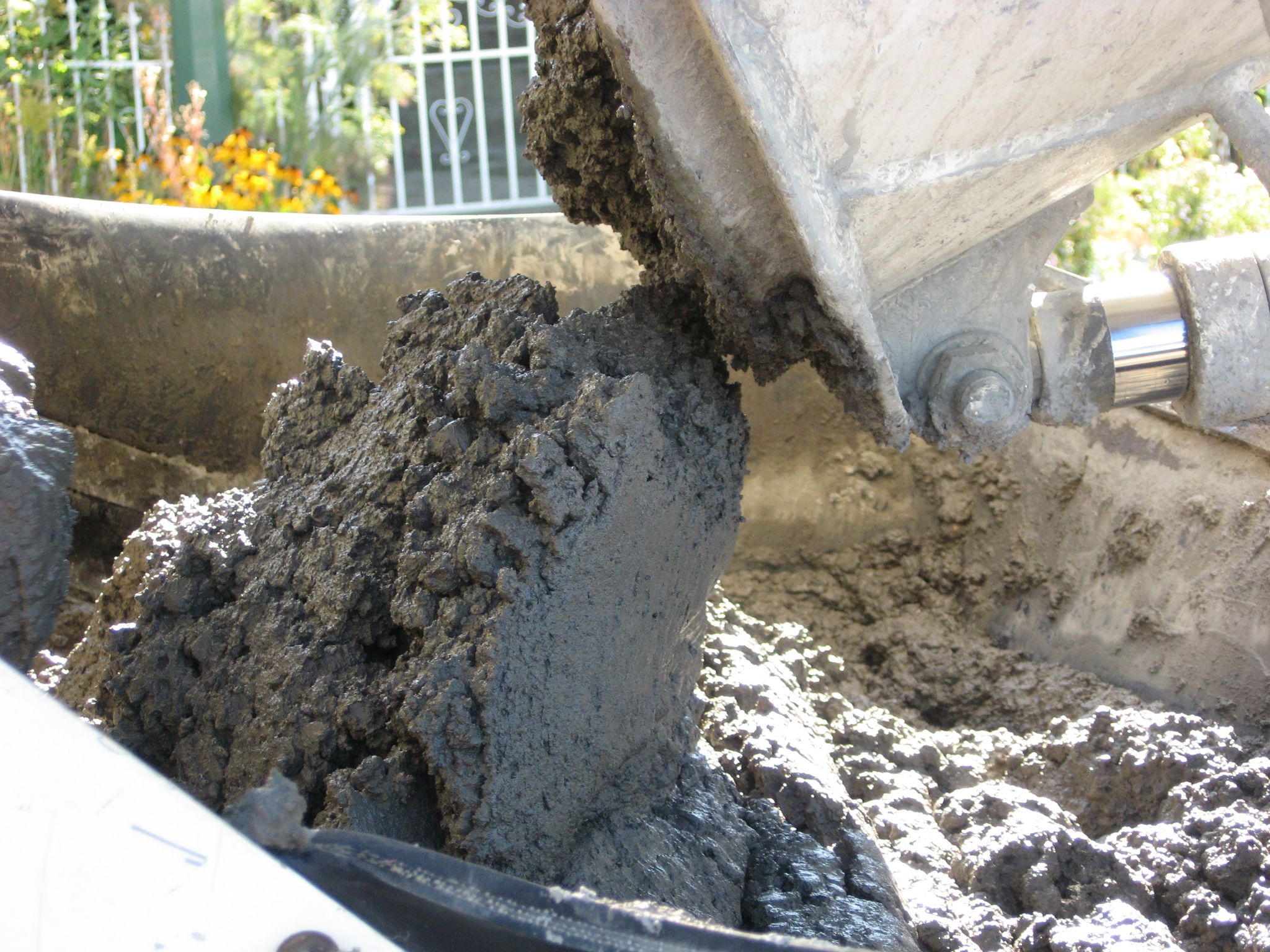
According to Chemistry World’s March 2008 article, “The Concrete Conundrum,” cement generates 1.5 billion tonnes of carbon dioxide (CO2) per year, which accounts for five per cent of the total CO2 production in the world.5 Concrete also uses one billion tonnes of water annually. Add to that the nine billion tonnes of aggregate used for concrete, which has a depletion effect on natural resources, and it can be surmised concrete properties themselves are not going to save the environment.
There are negative aspects attributed to the use of all building materials, of course. For example, steel requires tremendous energy for mining and refining. In a study by the National Ready Mixed Concrete Association (NRMCA), the CO2 emissions of concrete and steel framed buildings were compared on a per-square-metre basis, the former produced 550 kg of CO2 per square meter of floor area (112 lb/sf) and the latter 620 kg of CO2 per square meter of floor area (127 lb/sf).6
Defining sustainability
In determining how to build as wisely as possible, sustainability must first be defined. Sustainability can be defined as the capacity to endure or maintain. As per the United Nations (UN) Brundtland Commission’s “Our Common Future,” sustainable development meets the needs of the present without compromising the ability of future generations to meet their own needs.7
According to the Global Footprint Network, humanity uses the equivalent of 1.5 planets to provide the required resources and waste absorption, which means it now takes the Earth one year and six months to regenerate what is consumed in one year. UN scenarios suggest if current population and consumption trends continue, by 2030 the equivalent of two Earths will be needed to support the population.
As a collective global network, the population is at a seminal crossroads and the correct path must be chosen. Thankfully, there are initiatives and ‘blueprints’ available to alter a potentially disastrous outcome.

Triple bottom line
Attempting to educate the public on what variables need to be taken into account for true sustainable practice to take place, the U.S. Green Building Council (USGBC) has adopted the concept of a ‘triple bottom line’ within LEED. This is a framework LEED uses to recognize sustainable development, referring to three measured aspects.
- Environmental: The natural resource, environmental management, and pollution prevention come into direct play in regards to air, water, land, waste.
- Economic: This speaks about profit, cost savings, economic growth, and research and development.
- Social: The standard of living, education, community, and equal opportunity is taken into account.
Within the triple bottom line there lies an intersecting area where all three of these variables meld to create an earthly equilibrium state. When environment, economy, and social areas are equally attributed to within a given project, sustainability can be reached.
Recycle, reuse, reduce
The steps to a sustainable future also include the three Rs: recycle, reuse, and reduce. For instance, when structures made of concrete are demolished or renovated in some capacity, recycling the material is far more environmentally useful than sending it to landfills for disposal. Concrete is sent to primary and secondary crushers, foreign material is removed and then graded and washed, and it is then reused as coarse and fine aggregate.8 This readily available method of recycling concrete is a more attractive option as it saves space in landfills, reduces gravel mining, is cost-effective, and reduces the pollution involved in trucking materials.
Unfortunately, there are some drawbacks associated with having recycled concrete in a new mixture. The use of recycled concrete aggregates can lessen the durability of the concrete being used; in the end, this negatively affects the lifespan of the concrete structure. Further, as cited in by Roz-Ud-Din Nassar and Parviz Soroushian’s “Construction and Building Materials” recycled aggregate absorbs more water (two to three times as much) and causes increased shrinkage.9 However, if the optimal amount of recycled aggregate is used where no negative effects of concrete are seen, concrete sustainability improves.
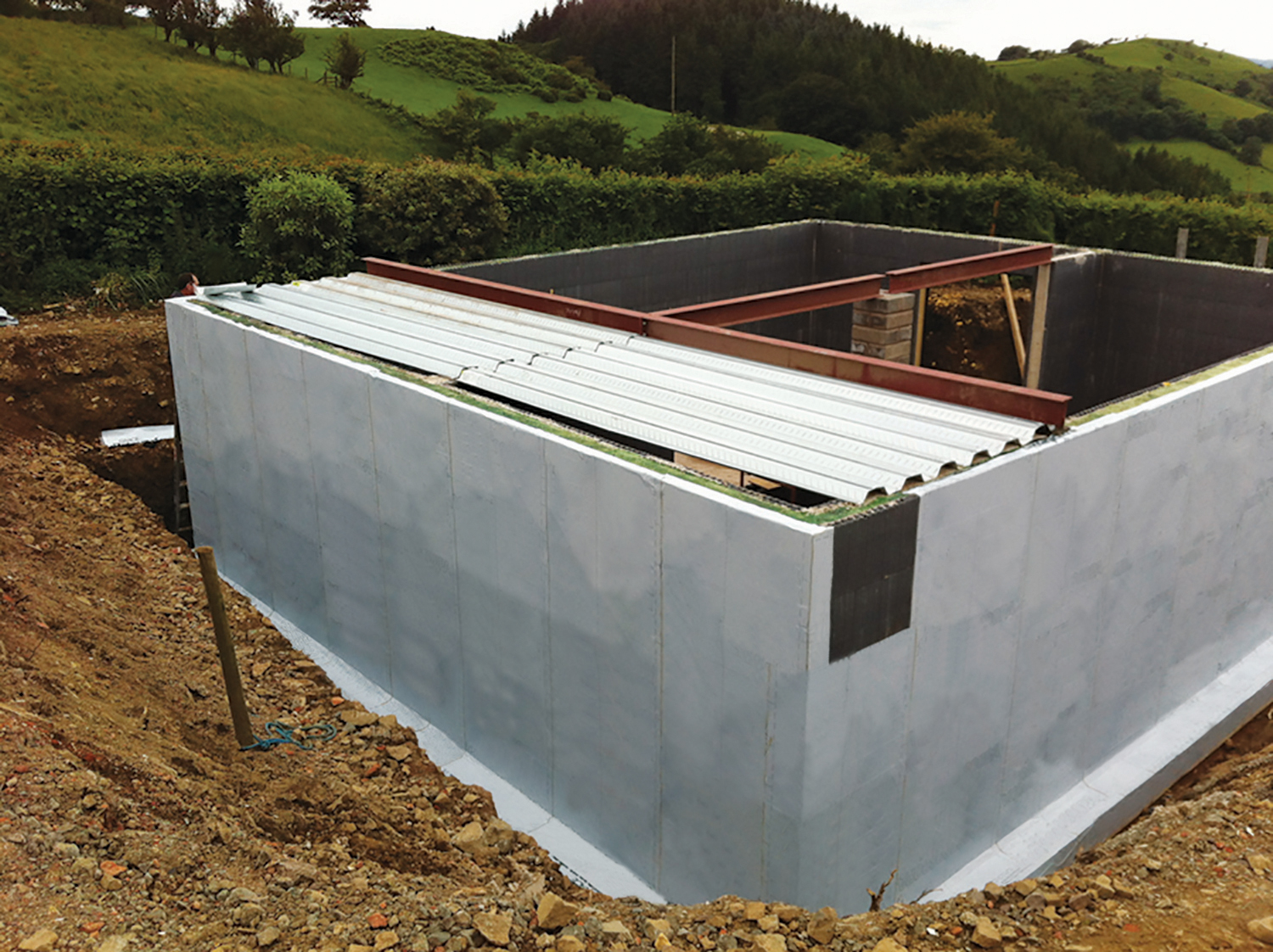
As mentioned, the manufacturing of cement causes CO2 by-products to be released into the atmosphere. However, there are supplementary cementitious materials (SCM) that can be used to lessen the amount of cement needed.10 In the same vein as the use of recycled aggregate, these by-products cannot replace the former, but can be employed to lessen the amount of virgin materials needed to a certain point. For instance, slag, which is a by-product of iron production in a blast furnace, can replace a percentage of cement mass in a concrete mixture, reducing CO2 emissions.11 However, when adding an SCM of any kind—including slag—testing must be done to confirm the amount is ideal for adequate concrete durability.
Designing for durability
While not all durable structures are sustainable, sustainable structures are durable. Therefore, one of the solutions for preserving natural resources is through increasing the service life of concrete by increasing durability.
Concrete must be designed to resist weather action and chemical attack while maintaining its desired engineering properties. When listing all the positive attributes of concrete, it is always known primarily as a durable material; yet, there is extensive evidence to show concrete structures are not meeting their designed service life due to rapid deterioration.
Concrete can deteriorate under certain circumstances, such as:
- chloride attack/corrosion of steel reinforcement;
- sulphate attack;
- alkali aggregate reaction (AAR); and
- freeze/thaw cycles.
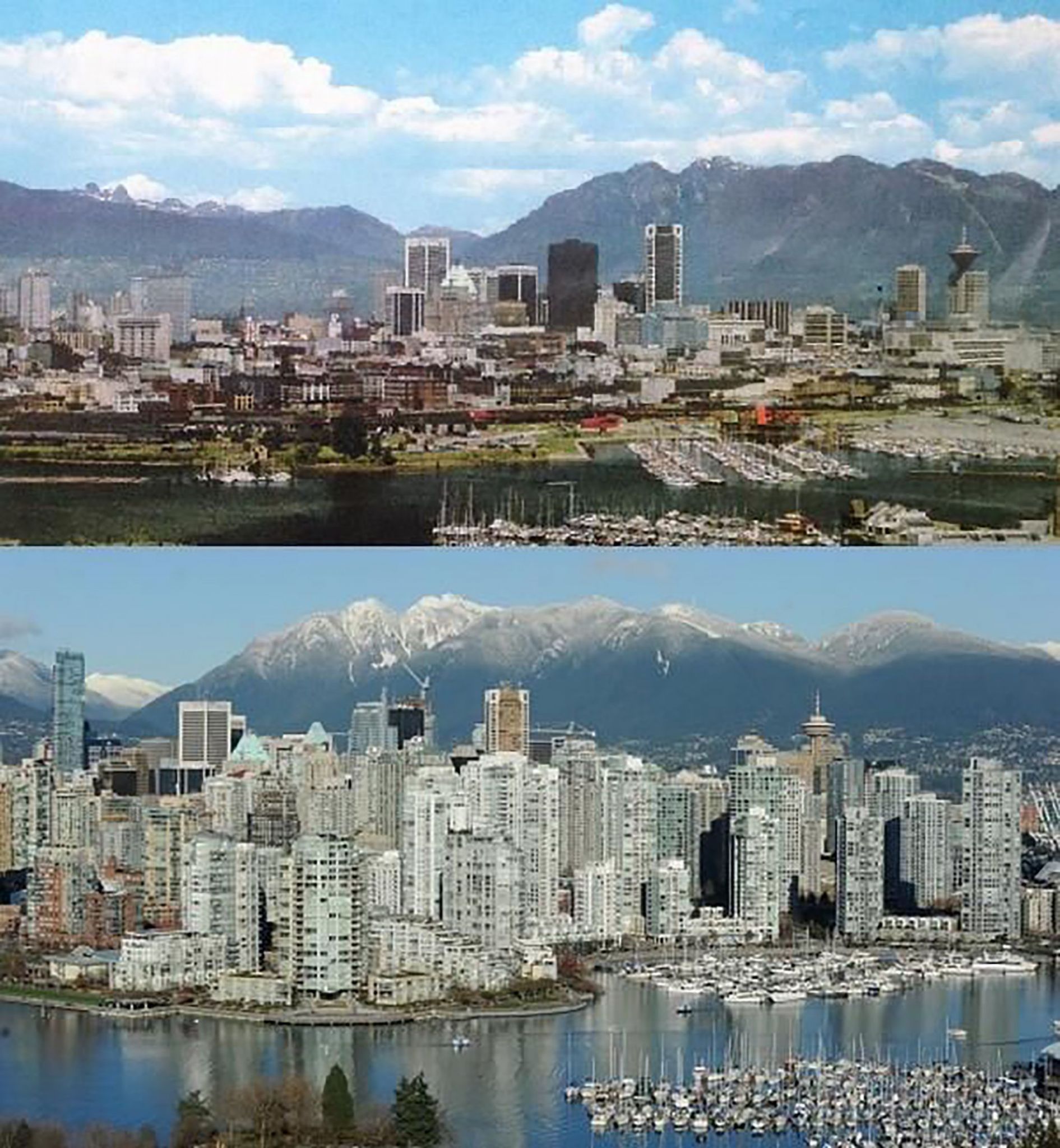
However, most adverse influence on concrete durability involves the transport of fluids through the concrete. Water continues to damage or completely destroy more buildings and structures than war or natural disasters.12 Concrete does have water-resistant qualities, but is certainly at risk to water damage when proper precautions are not taken. The problem arises when the concrete matrix starts developing cracks either due to early-age plastic shrinkage, or longer-term drying shrinkage, thermal changes, or excessive stresses due to loading. Cracks in concrete generally interconnect flow paths and increase concrete permeability.
Service life and durability increases by limiting cracks and water/chemical compound penetration. As the permeation of concrete decreases, its durability performance increases (in terms of physicochemical degradation). Permeation controls the ingress of moisture, ionic, and gaseous species into concrete. Thus, a waterproofing barrier must be used to ensure a watertight seal.13
One of the options available is an external surface-applied membrane. These surface waterproofing membranes form a barrier against water penetration. After hardening of concrete, a waterproof membrane is installed. The membrane is used as a system to prevent the ingress of water into foundations, roofs, walls, and basements. The external membrane is installed, keeping water out of the concrete and preventing deterioration.14
Most of the surface-applied membranes have many drawbacks, including:
- the external membranes are at risk of puncture damage;
- application can be labour-intensive;
- it takes time and money from the rest of a project; and
- it is difficult to repair since it can be inaccessible and hard to locate the failed area.
There are numerous situations in which an external membrane will fail, most stemming from design errors, installation mistakes, and material limitations and defects. Also, referring back to both the three Rs and the triple bottom line, the external membrane does not fit the bill. For example, if aggregate from building demolitions is going to be recycled, it must be confirmed the aggregate is not mixed with other products that will negatively affect the concrete. If an external membrane is used, the concrete demolition cannot be recycled because the membrane material is interlaced. This also interrupts the triple bottom line in that nothing can be recycled, it is not socially responsible to use a product that will be landfilled, and there are cost considerations for both landfilling and requiring virgin materials.
This then poses the question: why use more materials for a concrete waterproofing barrier when instead the concrete itself could be used as the barrier?
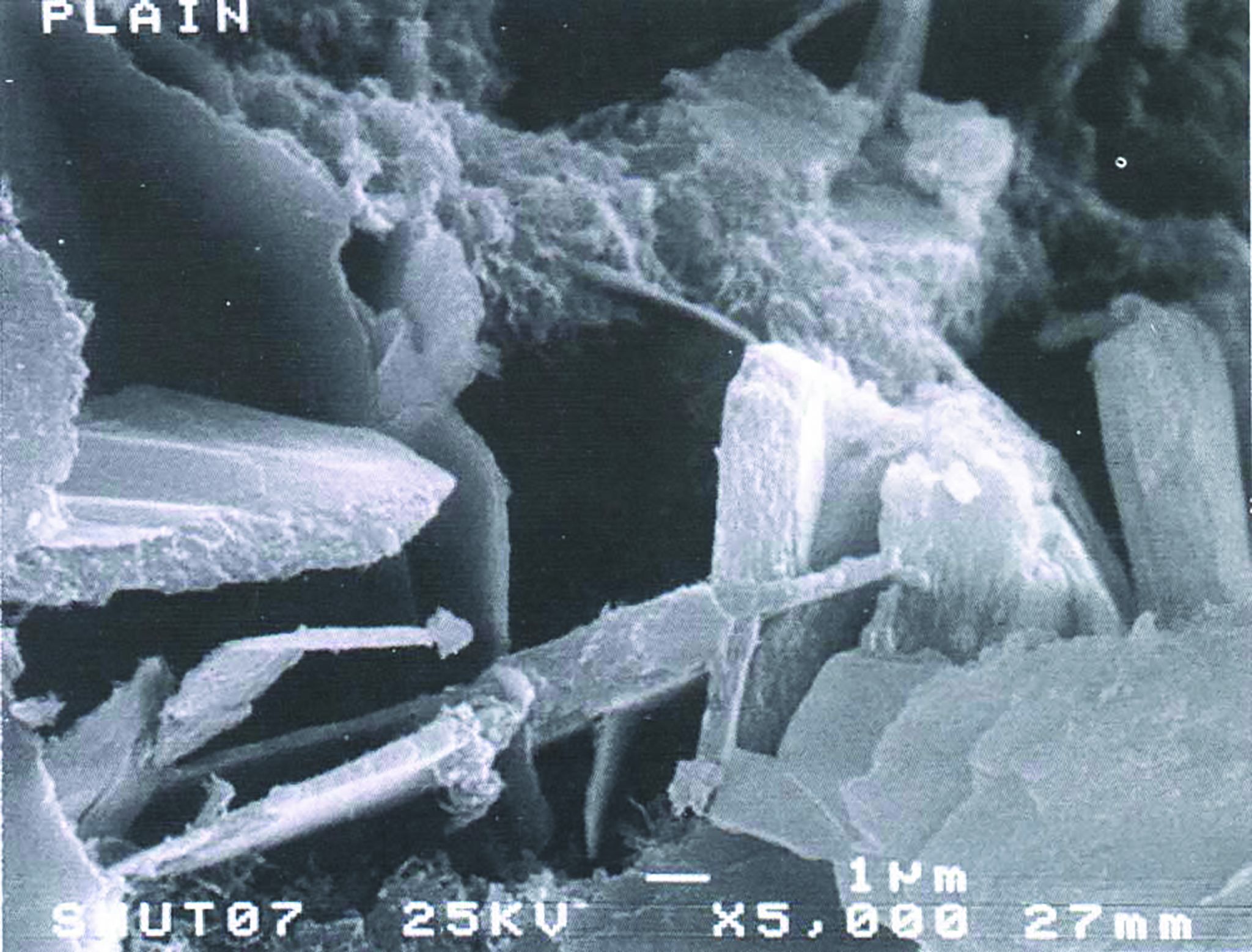
Integral crystalline waterproofing
The basic idea behind integral crystalline waterproofing (ICW) is to prevent the movement of water by plugging or blocking the natural pores, capillaries, and cracks present in concrete. The addition of an admixture displays itself during the reaction of cement and water, also known as hydration:
- untreated concrete: cement + water à CSH + CH
- treated concrete: cement + water + crystalline admixture à CSH + CH + pore-blocking crystal
The hydration reaction between cement and water creates crystals that helps strengthen the concrete and develops attributes to some water blockage, but not a watertight seal. Over the structure’s service life, concrete without any admixture is expected to develop micro-cracks that may develop into macro-cracks. These cracks can allow free passage to moisture, which will eventually reduce a structure’s service life. However, when crystalline technology is used, the passive admixture in the matrix gets activated as soon as it comes in contact with moisture in the pores and micro-cracks of concrete. On activation, this admixture starts crystallization and develops a needle-like microstructure of crystals in concrete.
Benefits of ICW
Integral waterproofing is a permanent solution, since it becomes part of the concrete so it will not wear away or crack.
Other benefits include:
- saving time by replacing the external waterproofing barrier;
- less repair, which means less overall cost;
- concrete remains recyclable at end of life, unlike surface-applied membranes; and
- elimination of the need for petroleum-based membranes, which are harmful to the environment.
The addition of the self-sealing water-protection system transforms concrete into a powerful water-resistant barrier. The crystalline technology turns porous concrete into an impermeable barrier. The result is a structure with reduced cracking, self-sealing, and waterproofing abilities that provide a powerful defense against water damage and corrosion of reinforcing steel. These attributes lead a concrete structure to being more durable, and are able to withstand tear and decay throughout service life. In turn, as the durability increases, fewer repairs will be needed, allowing the three Rs and the triple bottom line to be taken into account.
Conclusion
The longer a service life can be stretched for a material or product, the more sustainable that product is. The more sustainable the product, the better it is for the environment. When this thinking is instituted for the use of a readily available material, less harm is caused to the environment.
Notes
1 For more, see P.K. Mehta’s book Concrete: Structure, Properties, and Materials, Prentice Hall, 1993. (back to top)
2 Visit www.cagbc.org/Content/NavigationMenu/Programs/LEED/GoingGreenwithLEED/default.htm. (back to top)
3 For more, see World Business Council for Sustainable Development’s (WBCSD’s) “The Cement Sustainability Initiative–Recycling Concrete” at www.wbcsdcement.org. (back to top)
4 For more, see the U.S. Geological Survey, “Minerals Commodity Summary–Cement 2007,” at minerals.usgs.gov/minerals/pubs/mcs/2007/mcs2007.pdf. (back to top)
5 See Chemistry World’s March 2008 article, “The Concrete Conundrum,” at www.chemistryworld.org. (back to top)
6 Visit www.greenconcrete.info/downloads/12_ClimateChangeConcrete.pdf to access the study. (back to top)
7 Visit www.un-documents.net/our-common-future.pdf. (back to top)
8 For more, see B.C. Ready-Mixed Concrete Association’s (BCRMCA’s) “The Sustainable Benefits of Concrete Pavements,” at www.bcrmca.ca. (back to top)
9 For more, see Roz-Ud-Din Nassar and Parviz Soroushian’s “Construction and Building Materials” at news.msu.edu/media/documents/2012/02/2bebe2ce-4e0a-49ce-a450-a142a112bde4.pdf. (back to top)
10 For more, see M.I. Khana and C.J. Lynsdaleb’s “Strength, permeability, and carbonation of high- performance concrete,” found in Cement and Concrete Research Volume 32. (back to top)
11 See Portland Cement Association’s (PCA’s) “Design and Control of Concrete Mixtures,” at www.cement.org/for-concrete-books-learning/education/on-line-courses/design-and-control-of-concrete-mixes. (back to top)
12 See Michael T. Kupal’s Construction Waterproofing Handbook. (back to top)
13 For more, see Zhang, F.H. Wittmann, T. Zhao, and E.H. Lehmann’s “Neutron imaging of water penetration into cracked steel reinforced concrete,” in Physica B, Volume 405. (back to top)
14 For more, see L. Connell and K. Yuers article, “Waterproofing Made Crystal Clear” in the November 2009 issue of The Construction Specifier. (back to top)
Alireza Biparva, B.Sc., M.A.Sc., LEED Associate, is research and development manager/concrete specialist at Kryton International Inc. He has more than 10 years of experience in the field of concrete permeability. Biparva oversees several research projects focusing primarily on concrete permeability studies and the development of innovative products and testing methods for the concrete waterproofing and construction industries. He is an active member with the American Concrete Institute (ACI). Biparva has published several research papers in international journals and conferences on concrete permeability, waterproofing, durability, and sustainability. He can be reached by e-mail at alireza@kryton.com.