Mould, moisture, and the building envelope
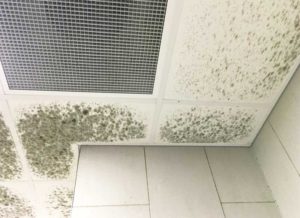
By David Muise and Gord Rajewski
The term “mould” refers to a large group of microorganisms that grow on organic material and reproduce through the formation and spread of spores. These spores germinate within a few days of finding the right combination of surface, moisture, and temperature, and can form new spores to produce the next generation of growth within five to 10 days.
Mould growth in buildings can occur when mould spores, which are always present in buildings, are exposed to wet or humid conditions for a sufficient length of time and on an appropriate surface to support growth. Water sources can include plumbing leaks, spills, foundation seepage, roof or wall leaks, condensation on cool surfaces such as inside ductwork and on windowsills, etc. In the presence of wet or highly humid conditions, mould spores can germinate within 48 to 72 hours (about 3 days).
Health risks and effects
Exposure to airborne mould can have varying effects on building occupants depending on their individual sensitivities. Those who are affected may have increased risk for respiratory symptoms, asthma, and respiratory infections in some individuals. Some common symptoms associated with exposure may include: runny nose and congestion, eye irritation, coughing, and headache.
There are no set exposure limits for indoor airborne spore concentrations. Health impacts are more broadly related to the presence or absence of dampness and mould growth and not a specific spore concentration or type of mould. Further, a combination of level of exposure, individual sensitivity, and extent and location of mould growth are all factors that may impact risk. Virtually, all guidelines reviewed indicate all mould can be harmful, so if discovered indoors, it should be eliminated.
Controlling mould growth in buildings
To remove all spores from a building, or to have a building free of finishes which promote mould growth, is simply not possible. The only way to truly prevent mould growth in a building is with the careful management of humidity, condensation, and water intrusion via building envelope leaks, floods, or plumbing failures. For this reason, the
risk of recurring mould growth must be addressed, not only by prompt repairs to address sources of water damage, but through a comprehensive mould and water damage management program. Key elements of a mould and water damage management plan are:
- The training of facilities maintenance staff in the causes and how to identify indoor mould growth.
- Development of a surveillance program to ensure all instances of water/moisture infiltration are discovered and mitigated in a timely manner.
- Regular building inspections to examine the condition of interior finishes which could be susceptible to water/moisture infiltration issues.
- Routine inspection of the interior accessible HVAC components in the building.
- Timely review of exterior envelope conditions to look for deterioration which could lead to future water infiltration and subsequent mould growth.
Given all the science and expertise available to draw from, even a regular educated employee can become a trained set of eyes, ears, and nose to identify potential problem areas.