Mould, moisture, and the building envelope
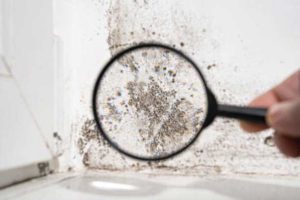
Building science and mould control
In general, the buildings envelope is a key line of defence for mitigating water and moisture infiltration into a building. General building envelope methodologies include the concept of providing both waterproofing and shedding water away from the buildings elements. The key building envelope concepts can be categorized into four components: deflection, drainage, durability, and drying. A properly designed, installed, and maintained envelope should be able to effectively deflect moisture from precipitation events, drain roof components efficiently away from the building, provide long-lasting materials and assemblies, and be implemented using three primary processes for drying. These processes include:
- Diffusion—movement of moisture through materials at the molecular level.
- Evaporation—conversion from liquid to a gas at the surface.
- Convection—transport of moisture via air currents.
To manage the negative effects of deleterious moisture within building enclosures, proper building envelope design must provide control layers that include water shedding surfaces, the design of building form and features to enhance drainage, employment of water-resistive barrier (WRB) continuous air barrier systems, thermal insulation, and vapour retarder/barriers. These concepts and designs must be effectively communicated (including effective details, drawings, specification, and construction review services) during the construction and/or restoration of buildings in order to ensure continuity of building envelope concepts.
Moisture control and durability of building envelopes is of particular concern in northern climates which are subjected to large temperature gradients, extreme weather, and require indoor heat and comfortable humidity levels. In addition to the moisture infiltration from exterior sources, such as precipitation, controlling indoor temperatures can also impact the production of moisture within a building. Similar to the concept of an aluminum can cooler sleeve, when warm air (indoor heated air) reaches a cool object (exterior/perimeter components of a building), it condenses and creates moisture. The concept that takes this into consideration is thermal bridging. This is simply a pathway (bridge) to move cold temperatures from an outdoor surface to an indoor surface. An example of this would be a wooden wall stud on an exterior wall. The stud gets cold and acts as a “bridge” to transport the cold temperature to an interior wall. When the interior wall cools, there is potential for condensation and mould growth.
When moisture becomes a problem and steps towards resolution
Mould is considered a symptom of a problem, its roots are most often linked to a failure in the design and execution of the building envelope assembly and the associated air handling systems provided.
The process towards resolution of moisture issues within a building enclosure involves three phases, broken down into nine key elements.
Phase I
Condition assessment
Investigators should undertake building envelope condition assessments as a first step towards the remediation of moisture problems in affected building enclosures. These assessments can include: review of architectural as-built drawings and details, interviews with occupants, on site visual review, air leakage testing, thermography, water testing, vapour transmission testing, destructive testing, monitoring, and sample material testing.
Evaluation
Once the sources of problematic moisture are identified and understood, a conceptual remedial repair plan with design options is created and evaluated. In this second step, inspectors will also draw upon their experience and industry knowledge, and consult with representatives from manufacturers to source appropriate options. Inspectors may also use analytical software, such as WUFI, THERM, Window, and Energy Star.