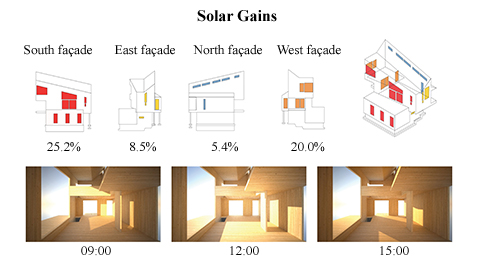
Using the CLT manufacturer’s tables, engineer Éric St-Georges, ing. M.Sc.A., calculated the structure and integrated the results with the 3-D drawings intended for the manufacturer. The non-CLT structural elements basically consisted of a single 12.2-m (40-ft) long steel beam that supported the roof, and a transversal 4-m (13-ft) long glued-laminated timber (glulam) beam supporting the larger mezzanine. A steel column was introduced between the two, transferring the load from the roof. Another steel column, placed at the southwest angle of the mezzanine level, works in tension, stabilizing the cantilevered floor.
When designing his home, one of the few constraints with which Laroche had to contend was the maximum width for cross-Atlantic shipping. To facilitate stacking in (and removal from) a 2.4 x 12 m (8 x 40-ft) container, panels had to be kept to a maximum width of 2.1 m (7 ft). The project’s longest panels, which were 8.7 m (28 1/2 ft), presented no problem. In the end, the entire house fit into one open-top container.
In terms of timing, the CLT manufacturer received the order on May 7, 2013. Panels were ready two weeks later and were shipped out on May 22. The container arrived in Montréal on June 12, with materials onsite in Saint-Calixte, ready to be unloaded, a week following.
Meanwhile, beams and columns, manufactured by a local company, had been delivered as well as connectors and screws, ordered from a North American supplier by the Montréal builder involved in the project, OÏKOS. With footings and foundation ready, assembly started June 20. It took less than five days to piece the whole thing together, which was about a day and a half longer than expected. The delay was due to heavy rains and the architect refusing to take down a tree that blocked the easiest route. By the end of June, all panels had been assembled—floors, walls, and roof.
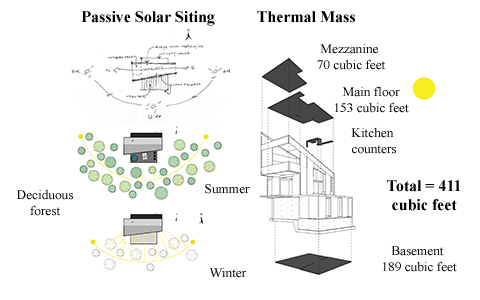
The building was completed during the following months, with the architect allowing himself time to weigh each subsequent move. Windows were installed after the panels, followed by the pouring of concrete slabs—over the CLT floor panels in the case of the entry and mezzanine levels, and directly on the ground at the lower level.
Plumbing and heating elements were incorporated as the floors were being done. For esthetic reasons, most electrical wiring was run on the exterior face of the CLT panels. Insulation was installed: 178-mm (7-in.) blown cellulose for the walls and 203 to 279-mm (8 to 11-in.) polyisocyanurate (polyiso) rigid insulation for the roof, which was then covered with a thermoplastic polyolefin (TPO) reflective membrane.
Two ‘breathable’ membranes—an air barrier and a rain barrier—ensured proper sealing and protection of the building. Finally, untreated red cedar planks, set vertically, were used as exterior finish.