Moisture management for tall wood buildings
Glulam floor panels may need less protection because of the tight wood-to-wood panel construction, and many suppliers use a light sealer to protect the wood during shipping. Onsite taping of panel joints and internal service penetrations is recommended.
With more open joints between parallel laminations, NLT panels require more protection than CLT and glulam. Water penetrating between NLT laminations and absorbing into the wood mid-panel depth is more difficult to dry than moisture adsorbed by the upper or lower surfaces. NLT panels often include a cover layer of plywood or oriented strand board (OSB) on the upper surface and the joints in this layer can be taped after installation to provide a continuous water-resistant layer. Some OSB sheathing products are designed with an integral coating and can provide more resistance to moisture. This is an easy specification substitution if the construction schedule slides into a rainier period. If heavy rain is unavoidable during the construction of the floor levels, a factory-applied coating, sealer, or membrane can be added to the cover layer’s upper surface (Figure 5, page 44).
The added resistance to water penetration provided by the steps described above will also help control bleed water from concrete or gypcrete floor toppings. Further, each of these measures provides a built-in protection against accidental exposure to water during operation of the building.
When the full construction schedule for a tall building is considered, a reasonable approach to protection for horizontal surfaces is to create multi-storey compartments rather than addressing every floor. This allows for ‘break points’ to be planned into the schedule to accommodate weather and schedule delays: construction proceeds to designated levels where a complete water-resistant layer is installed before continuing the build. Weather events affect only the uppermost compartment. This strategy also allows for the air- and water-tight compartments to proceed with interior work, and probably more importantly, have active fire protection systems.
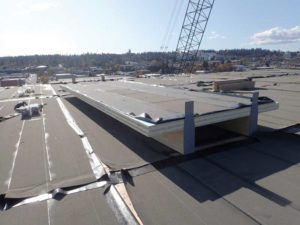
Design assemblies for long-term protection of the mass timber structure
Mass timber structures will have a long service life if kept within stable temperature and moisture conditions—the objective is to create and maintain warm and relatively dry conditions. The author’s firm recommends an enclosure to the exterior of the primary structure that passes over and encloses each floor level. This approach minimizes unprotected structural elements, and, as noted above, also helps address fast weathertightness of the building during construction. The design objective will be to keep all mass timber elements within, and protected by, the thermal enclosure.
Designing mass timber assemblies to allow for in-service drying is an important long-term protection against unexpected water intrusion. Generally, roof and floor assemblies should be designed so that drying is possible to at least one side of the assembly.
Wood undergoes shrinkage as it comes into equilibrium with the conditioned interior environment of the building. Tall wood structures have the potential (depending on framing and the specific products used) to undergo a significant amount of drying shrinkage. Although the overall shrinkage of the structural frame will be considered in the structural design, it is critical to look at how this movement will affect joints and transitions between materials and systems, and special attention should be paid to interfaces with building elements (such as concrete elevator cores) that will move differently over time. It is important to note unexpected wetting during construction may lead to dimension changes as the building dries.
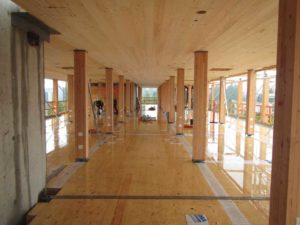
Developing a construction moisture management plan
The plan to manage exposure to moisture during construction will ultimately be the responsibility of the constructor. However, as discussed above, the plan to protect mass timber components (e.g. using a prefabricated enclosure to quickly enclosure the structure) does inform design decisions and should impact construction sequence planning, both at a high level (time of year) and in sequencing trades onsite. The author’s firm suggests the creation of a draft plan early in the detailed design process to help establish requirements that will later become part of the general conditions for the project. At a minimum, the draft moisture management plan should include:
∞ identifying moisture risks during manufacturing, transportation, storage, and construction, with a statement of impact for each construction schedule and long-term performance of the building;
∞ specifying measures to mitigate these risks, including identification of parties responsible for each;
∞ considering both passive (for example, factory-applied coatings, or tenting the structure) and active measures (such as a protocol for removal of ponding water); and
∞ processing for documentation and reporting.