Moisture management for tall wood buildings
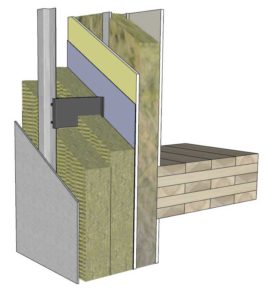
Most of the sources listed above can be controlled through careful design of the building enclosure to minimize bulk water leakage, avoid accumulation by air leakage or vapour diffusion, and allow for some drying to the interior or exterior as environmental conditions allow. The period of time the structure is unenclosed during construction is the highest risk of moisture exposure for the structure. Although tall buildings present a smaller horizontal ‘footprint’ to rain, wind-driven rain has access to a greater number of floors and, given the longer construction time for tall structures, the exposure may be significant until the building enclosure is in place.
To address the concerns above, the author’s firm has the following recommendations for tall mass timber buildings.
Enclosure the structure quickly
Mass timber structures assemble and are loadbearing more quickly than concrete-framed ones. Speed of building enclosure construction is, therefore, an important factor in the protection of wood from moisture, reducing the amount of time structural elements are exposed to the weather. To fully protect the mass timber elements, construction of exterior wall and roof elements should be planned to enclose each floor level quickly as the erection of the primary structure proceeds. This can be done with temporary protection (scaffolding and tarping, for example) but the costs may be significant. Prefabrication of wall components is recommended to meet this ‘fast enclosure’ objective.
Unitized curtain wall or insulated precast concrete systems are good choices with robust technical details, good design support, and a mature procurement process. These systems, however, may not easily meet increasingly stringent project requirements for low operating and embodied carbon. Other options, such as light steel frame, light wood frame, or cross-laminated timber (CLT) panels (Figure 1), are possible, but may require additional design work and planning, including:
∞ detailing of joints and interfaces with other enclosure systems;
∞ co-ordination of multiple suppliers offsite (frame, insulation, cladding, glazing systems); and
∞ some level of work onsite to complete critical seals and finishes.
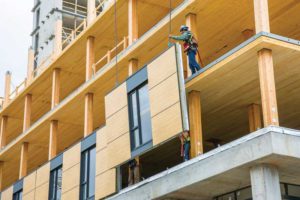
The challenges listed above have been successfully addressed for several tall mass timber projects in Canada. For example, Figure 2 shows the installation of large frame panels with windows and cladding pre-installed offsite. No finishing work was required on the exterior of this building, but final air and water seals, additional thermal insulation, and interior finishes were installed from the interior after panels created a watertight exterior enclosure.
Protect horizontal surfaces
Floors and roofs are at high risk of water penetration during construction. However, strategies can be employed for both types of assemblies to minimize exposure.
For roof assemblies, a fully adhered membrane installed by the supplier before the panel leaves the production facility can provide protection against moisture during transport and storage (Figure 3, page 40). This membrane can also serve as a temporary roof membrane after the panel has been installed. The author’s firm recommends ‘designing in’ this protection layer in the place of the deck-level air control layer (commonly referred to as the roof vapour retarder) in the finished assembly.
Floor decks may also be exposed to rain for shorter periods during construction, but are still subject to saturation of the mass timber and staining of the exposed surfaces (Figure 4, page 42). Recommendations for protection for CLT, glue-laminated (glulam) timber, and nail-laminated timber (NLT) floor panels differ slightly. Due to the tightly assembled panel construction, CLT and dowel-laminated timber (DLT) panels are less open to bulk water penetration. A wax-based sealer on the end grain with a low permeance polyurethane coating on the top surface of the panel will generally be enough protection if rain exposure can be minimized. The author’s firm has tested several options and recommends the following:
∞ apply the coating in the factory, testing if necessary to ensure adequate thickness (avoid
site installation);
∞ observe the coating manufacturer’s installation instructions for moisture content of the wood (often best controlled at the factory) and surface preparation;
∞ apply waxed-based coating to all exposed edges, including internal service penetrations and where fasteners and anchors will be installed; and
∞ include requirements for construction-phase moisture protection.