Modular Building: An inherently greener construction process
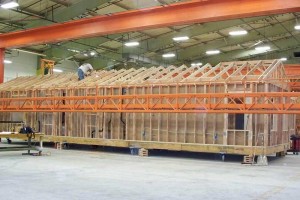
Surrey Social Housing
This three-storey supportive housing facility is the largest of five pre-planned affordable housing projects, repurposing and using existing facilities from the Olympic Games. These facilities provide safe, supportive housing for seniors, people with disabilities, and individuals who are homeless or at risk of homelessness.
The facility was designed to the City of Surrey Urban Design Guidelines to complement the neighbourhood in which it is located. The 52 studio apartments for the homeless (or those at risk of it) include a fully equipped kitchen, eating area and living room, a bed alcove, and washroom.
The modules were originally constructed for single-storey temporary accommodations built to house two people per room; they included kitchen and plumbing rough-ins so the individual units could be transformed into multi-storey permanent buildings. The modules were designed to fit together differently when they became part of the larger structure with site-built hallways and common areas including a commercial kitchen and dining room, administration offices, and additional space for program support services. The social housing facilities constructed under this program were built to all local or applicable standards, codes, and bylaws governing wood-framed buildings. The exterior roofing, cladding, and other associated work was completed onsite.
Designed to meet or exceed EnerGuide 80 guidelines, the housing units have a high level of energy efficiency, including:
- energy-efficient furnaces, heat pumps, thermostats, and lighting;
- low-flow fixtures;
- Energy Star appliances and windows; and
- high R-values combined with fewer thermal breaks for better draft-proofing.
Manufacturing of the modules started in February 2009 for November completion of the temporary accommodations. Tear-out began in March 2010 after the Olympics and the modules were relocated to Surrey and stored offsite until the new site was ready.
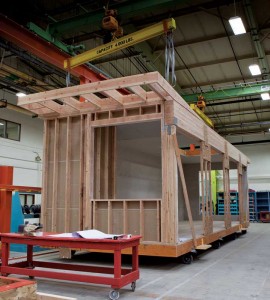
Photos courtesy Zeta Communities
Conclusion
Modular construction can provide significant green advantages by decreasing the amount of waste the construction industry produces. The modular construction process allowing waste to be reduced in the factory and buildings is designed in a way that allows them to be reused. Building the modules offsite also significantly lowers the environmental impact on the jobsite. Additionally, the construction process lends itself well to extending the useful life of building components but repurposing the modules for secondary use. By controlling all aspects of production, the modular building industry can create superior buildings to meet the highest green standards.
Tom Hardiman, CAE, is the executive director of the Modular Building Institute (MBI)––the international non-profit trade association for commercial modular construction. He has worked in the construction association industry for 13 years. Hardiman can be reached at
tom@modular.org.