Modular Building: An inherently greener construction process
Ability to repurpose
As demonstrated by the case studies in this article, buildings constructed using a modular process are designed for onsite assembly. As such, the buildings are also designed for disassembly. Modules and components can be more easily disassembled at the end of a facility’s useful life, and repurposed for a secondary site. This effectively closes the end of the lifecycle loop, or at least greatly extends the lifecycle of the modules.
Repurposing is a relatively new concept within the sustainability community as it has been commonly accepted most materials will in fact end up in landfills after a certain point. In most cases, it simply costs too much to deconstruct a site-built structure and salvage materials for repurposing.
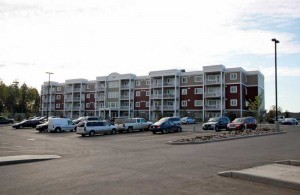
Photo courtesy BCT Structures
Modular and LEED
While using modular construction does not automatically qualify for points under the Leadership in Energy and Environmental Design (LEED) rating system, there are several areas in which modular buildings can earn points. In some categories, the building method can even provide an advantage. The Canada Green Building Council’s (CaGBC’s) LEED for Homes rating system rewards construction waste management at the construction site in the category of Materials and Resources (MR) for material-efficient framing, specifically for offsite fabrication. It also awards points for waste management by being able to account for the materials, by weight or volume, that are diverted from landfills. Special recognition is also given to using existing buildings and materials with recycled content.
The offsite construction process also provides other advantages in meeting LEED requirements. It can have minimum site impact if delivered carefully and strategically with respect to site constraints qualifying projects for credits under Sustainable Sites (SS). The tight building of modular construction allows for superior energy conservation and indoor air quality (IAQ) qualifying modular projects for credits in the categories of Indoor Environmental Quality (EQ) and Energy and Atmosphere (EA). (See the Canada Green Building Guide (CaGBC) Leadership for Energy and Environmental Design (LEED) for Homes rating system. For more information, visit www.cagbc.org/AM/PDF/LEED_Canada_for_Homes_2009_RS.pdf).
Modular buildings are particularly well-suited to be energy-efficient depending on assembly techniques, making them eligible for EA Credit 1, Optimize Energy Performance. Additionally, modular unit manufacturing plants contribute to meeting the intent of EQ Credit 3.1, Construction IAQ Plan During Construction.
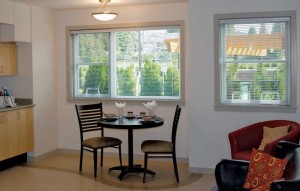
Photos courtesy Britco
Case study examples
The following are case studies that demonstrate the resource efficiency and inherently green benefits of the modular construction process.
Stoney Mountain Apartment Complex
This project is the largest four-storey modular project ever undertaken in Alberta. The two apartment complexes were designed to esthetically blend into their surroundings by incorporating earth-tone materials such as stone and hard plank siding in warm neutral colours. The balconies were installed onsite, but used refabricated balcony structures that were then craned into place.
The modules were structurally engineered using a minimum number of materials without compromising the structure’s integrity during transport. Some modules were built in one continuous section and then divided onsite.
Each suite has its own energy recovery ventilation (ERV) system to provide isolated ventilation and to achieve energy efficiency by reclaiming heat and recirculation back into the suite from heat loss sources such as the bathroom exhaust fans. The whole building complex employed a geothermal hydronic heating system and also incorporated solar energy to fuel the water heating system. Corridor and party walls used insulation and the design specifically allowed each suite to essentially be one module; therefore, double wall construction was realized between units and allowed for a sound transmission class (STC) rating in excess of 55. Windows were designed as dual-pane, low-emissivity (low-e), and argon-filled.
Chilliwack Social Housing
The Vancouver Organizing Committee for the 2010 Olympic and Paralympic Winter Games and B.C. Housing made an agreement to convert over 320 temporary modular housing units into 156 permanent apartments for people in need in six communities across the province:
- Chetwynd;
- Chilliwack;
- Enderby;
- Saanich;
- Sechelt; and
- Surrey.
As part of this initiative, the groups worked with a local modular builder to design and manufacture temporary accommodations used by almost 600 officials in Whistler’s Athletes’ Village during the Winter Olympics. The 74 modules were disassembled afterward and relocated to the communities. (For more on the Athletes’ Village, see “The Efficiency of Modular Construction” by this author in the July 2010 issue of Construction Canada. Visit www.constructioncanada.net and select “Archives.”)
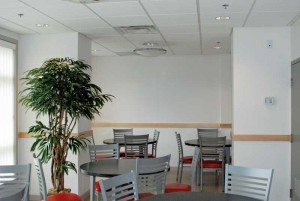
One of the projects completed as a result of this partnership was a social housing project in Chilliwack, B.C. The modules were manufactured in February 2009 with onsite completion in November. After the Olympics, the modules were relocated to Chilliwack and stored offsite until they were moved to the new site in September 2010. The site-constructed first floor incorporates office and meeting space with other amenities including a games room and lounge, commercial kitchen and dining room, and ancillary space for youth services.
There are 11 suites on each of the three floors with the first floor for youth and the top two floors for adults struggling with mental health and addiction. The 33 suites each have one bedroom or one bedroom with a bed alcove for residents with children, and feature fully equipped kitchens with eating areas, living rooms, and washrooms.
The modules were designed to be reconfigured from single-storey temporary accommodations into a multi-storey permanent building, so they had to fit together differently when they became part of a four-storey structure. Since the modules were used for the suites, they were constructed with kitchen and plumbing rough-ins and designed with accessible features. The lumber used in the modules’ construction was primarily sourced from B.C. forests damaged by pine beetle infestation, which otherwise would not have been used.
The design and construction achieved high sustainable standards to promote energy efficiency and minimize any environmental impact. When the temporary accommodations were dismantled, the metal siding and other materials were recycled and the untreated wood blocking was sold for firewood.