Mid-rise wood-frame construction gets innovative
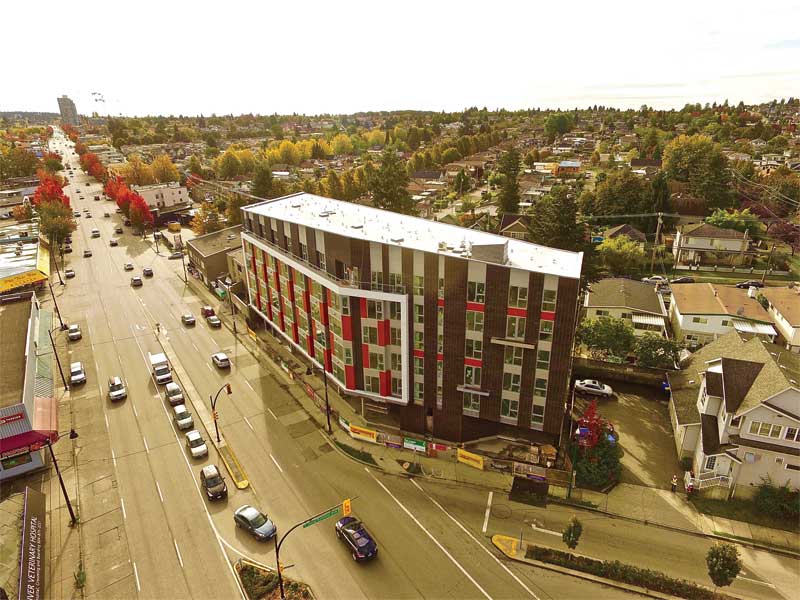
Photo © Take Off Eh! Aerial and Artistic Photography
King Edward Villa
Completed in the fall of 2017, King Edward Villa is a mixed-use residential building, with a basement parking garage, ground-floor commercial space constructed in concrete, and 77 apartments occupying five floors of wood-frame construction above.
As with The Heights, GBL Architects applied to rezone this former C-2 zoned site under the City of Vancouver’s Rental 100 program. Permission was granted for a six-storey building with an overall floor area determined by the application of the pre-existing setback requirements to the new structure.
With a 1-m (4-ft) setback from the sidewalk, the plan of the building follows the property line, making an oblique angle where Kingsway and King Edward Avenues meet. The ends of the building abut the property line at either side of the site, giving the long front and rear elevations a north-northeast and south-southwest orientation, respectively. The only vehicular access to the site is through the rear yard, where a large tree reduces the width to 12 m (40 ft).
Once building permit drawings were in process, the project was let as a construction management contract. Up to this point, it was assumed the building would be constructed using conventional nominal 20 x 152-mm wood-framed exterior walls to meet the energy requirements of American Society of Heating, Refrigerating, and Air-conditioning Engineers (ASHRAE) 90.1, Energy Standard for Buildings Except Low-rise Residential Buildings, and achieve a Leadership in Energy and Environmental Design (LEED) Gold certification as mandated by the City of Vancouver.
The contract was awarded to Performance Construction, which persuaded Richard Wong, the owner, to consider a low-energy option based on passive design principles, using a similar business case to that described previously for The Heights.
At King Edward Villa, the super-insulated envelope was achieved by using two nominal 20 x 101-mm wood-stud walls with a 25-mm (1-in.) space between them. The exterior sheathing is plywood with a vapour-permeable (breathable) peel and stick membrane that also acts as an air barrier. The entire wall depth is filled with two layers of spray-applied cellulose insulation achieving an R-value of 28 (Figure 5). The cellulose insulation eliminates heat transfer by convection; because it is hygroscopic (i.e. able to absorb and release moisture), it also provides added insurance against interstitial condensation.
The wall’s inside is lined with airtight drywall along with vapour barrier paint on the interior face. Gaskets were installed around power receptacles and other openings, and the edges were sealed with fire-resistant caulking.
Since the floor structure runs parallel to the long front and rear exterior walls, the only component penetrating the insulation layer is the plywood flooring. Windows and doors are steel-reinforced vinyl ‘tilt-and-turn’ units, with low-emissivity (low-e) double glazing. The average window-to-wall ratio is approximately 32 per cent, but feels higher because the two end walls of the building are fire-resistance-rated walls with no window openings.
The drywall was installed before the gypsum concrete floor screed was poured. This increases the airtightness between inside and outside as well as between suites. Baseboards were glued in place. The air change rate is controlled by a pair of heat-recovery ventilators (HRVs) installed in each suite.
Above the concrete basement and ground floors, the structure consists entirely of light wood-frame components factory-prefabricated by Mitsui Homes. These include 20 x 152-mm nail-laminated timber (NLT) panels used for the elevator shaft, floor, and roof trusses as well as wall panels.
Of these components, the 304-mm (12-in.) deep parallel chord floor trusses are the most ingenious. Running parallel to the exterior walls, their open webs permit all the main mechanical and electrical services to be run horizontally throughout each suite (Figure 6), with vertical drops only where needed for HRV grilles, light switches, and plugs. This proved quicker and less expensive than the traditional roughing-in process.
Another advantage of the floor trusses is they could be hung from their top chords only, enabling the drywall finish on party walls to be notched around them, but otherwise taken up to the underside of the floor above. This simplified the fire separation between suites, with intumescent caulking used to seal the joints, and mineral wool insulation employed in the ceiling cavities.
Demising walls between suites were also constructed using a double-wall system to improve sound isolation. On the southwest side of the building, these walls are topped with a 304-mm-deep parallel strand lumber (PSL) beam that cantilevers approximately 1.5 m (5 ft) beyond the exterior wall to support the balconies, which also function as sun shades. This detail means that, rather than a series of header joists penetrating the building envelope to support the balconies, only the PSL beams project, significantly reducing thermal bridging (Figure 7).
From the architectural and structural drawings, Mitsui Homes created a 3-D model that identified each individual wall panel and truss, giving it specific attributes and a unique position within the model. Co-ordinated with mechanical and electrical drawings, wall panels that were to be superimposed one above the other were framed with identical placement and spacing of studs. This enabled vertical drops for plumbing pipes, electrical conduits, and tie-down anchors to be continuous, requiring only minimal drilling of plates and headers on site (Figure 8). The net result was to reduce uncertainty, mistakes, and mess while speeding up installation. It also enabled drywall to be installed from bottom to top—a safety precaution that can limit the extent of a construction fire.
Framing lumber with a moisture content of 15 per cent or less has become the norm for five- and six-storey construction. The quality and consistency of the material used by Mitsui lends itself to precise fabrication, with frames being factory-produced to tolerances of 3 mm (0.12 in.) or less.
Speed and accuracy are the most notable advantages of prefabrication. The unique code given in the factory to each completed panel identified where it fit in the construction sequence. In turn, this enabled deliveries to be made on a ‘just-in-time’ basis and improved the flow of work on a tight and congested site. This was particularly important on the King Edward Villa project, where the site had only one narrow point of access, and lane closures on the arterial road were particularly disruptive.
The specified slider id does not exist.