Mid-rise Makeovers: B.C. code changes encourage building with wood
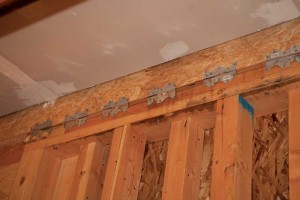
Advancing light-frame wood construction
Light-frame wood construction has been a mainstay in the North American forestry, construction, and design industries for small commercial and residential buildings. Perhaps because of familiarity, many architects and engineers have taken the technology for granted, and may have overlooked its potential for larger-scale buildings.
This situation has been perpetuated in part by NBC, which has historically applied strict limitations on the size and height of combustible light-frame wood construction. In 1990, however, the maximum allowable height for residential (Group C) buildings of wood-frame construction was increased from three to four storeys. In 1995, this was extended to Group D and E occupancies—the former including business and service buildings and the latter including mercantile occupancies.
Light-frame wood construction has always been known for its economy, versatility, and speed of erection, but not necessarily for its strength, accuracy, and precision. While that perception may have been legitimate several decades ago, new materials, innovative engineering solutions, and offsite prefabrication have substantially increased the quality and sophistication of light-frame wood construction.
For the most part, these individual changes have been unobtrusive, hidden within wall, floor, and roof assemblies, but collectively their impact has been profound. As a result of these modifications, light-frame wood construction is now considered a viable, affordable, and environmentally responsible alternative to concrete and steel.
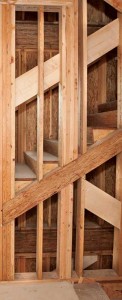
Mid-rise design and construction
When constructing and designing mid-rise structures with wood, there are various factors to consider.
Seismic performance
Key aspects of design that become critical in this new generation of mid-rise structures include increased dead, live, wind, and seismic loads that are a consequence of building to a greater height. The responses to such an imperative within more complex mid-rises involves the adaptation of structural and architectural design details that address key construction-related issues.
Earthquake engineering researchers examined the seismic performance of a full-size, six-storey wood building on the world’s largest shake table at a facility in Miki City, Japan, as part of the BCBC review process. (To read more on this study, see “Seismic Testing” by Steven E. Pryor, PE, SE, John W. van de Lindt, PhD, and Shiling Pei, PhD, in the June 2010 issue of Structure Magazine. Visit www.structuremag.org/article.aspx?articleID=1078#ArticlePDF). The structure was built from B.C. forest products and with commonly used Canadian construction techniques. The strongest test simulated an earthquake expected to occur once every 2500 years. Results confirmed seismic risk can be kept at an acceptable level for six-storey, light-frame wood buildings when they are constructed and designed well.
Acoustic performance
Recent testing has confirmed noise and vibration (i.e. flanking) transmission can be further reduced by breaking the continuity of the subfloor and ceiling system at the acoustic separation. Additionally, blocking members can be added in the floor cavity to decrease joist vibration, and concrete topping is now universally used on all floors to minimize vertical transmission of airborne noise. Research has shown the addition of an extra layer of floor sheathing is also an effective method for lowering the transfer of noise and vibration.
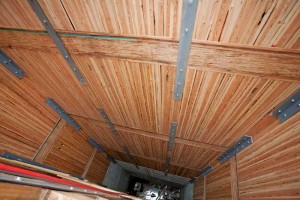
Fire performance
For construction up to six storeys, fire separations (other than firewalls) are required to have a fire resistance rating of one hour. BCBC does not prescribe any particular solution, leaving designers and code consultants the flexibility to determine the best option for their project. Solid, nail-laminated 2×6 dimension lumber construction is one way to achieve the required one-hour fire resistance rating for wood elevator shaftwalls.
With mid-rise construction, the exterior cladding must be non-combustible or constructed of materials expected to limit vertical fire spread. These include stucco, brick, and/or siding material (i.e. metal or vinyl). This is intended to minimize the risk of fire spreading to upper units if windows in an apartment below break because of heat from a fire.