Metal’s winning ceilings
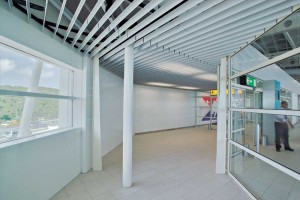
Linear metal systems also can be installed as an open-plenum system. As the names suggests, ‘open plenum’ refers to an application where the occupied space is not separated from the space above by a continuous ceiling.
Other open plenum systems include beam assemblies, which use deep sections to create large, open modules. These systems allow completely free circulation of air and the creative placement of light fixtures and other features. They are effective in defining a ceiling plane without a solid ceiling, and letting displays define the space, such as in a retail centre or showroom. Specifiers select:
- depth and width of the beams (typically 25 to 102 mm [1 to 4 in.]);
- module size (typically 305 to 1219 mm [12 to 48 in.]); and
- finish.
As a subset of beam systems, open-cell systems offer an inexpensive way to add a design element to open areas. These systems use a standard grid, painted 360 degrees. This type of ceiling system should be used with heavily perforated panels and wire/mesh panels. Standard grid faces are 24, 14, and 35 mm (15⁄16, 9⁄16, and 1 3⁄8 in.). Standard grid module sizes are 610 x 610, 610 x 1219, and 1219 x 1219 mm (2 x 2,2 x 4, and 4 x 4 ft). As previously noted, specifiers must be cautious in reconciling Imperial-sized grids with soft and hard metric-sized grids.
For open-plenum systems, ‘masks’ are used to provide an attractive way to block the view of the structure and mechanical systems above the ceiling from a casual viewing angle without impeding air movement. Depending on the ceiling height, the view is usually obstructed at a 45-degree viewing angle. For an industrial look, plenum masks with woven wire and expanded metal can be selected in carbon steel or stainless steel, unfinished or painted, and in several styles.
Plenum mask cell ceilings involve a grid suspension system with vertical-slat covers installed over the web of the grid to give a solid appearance. Ceiling suspension modules are usually sized as standard grid modules. Once the web covers and cells are installed, the openings are much smaller; cell sizes range from 104 x 104 mm (4 x 4 in.) to 305 x 305 mm (12 x 12 in.). This provides the desired plenum masking, while still allowing for the installation of standard services such as air and light diffusers and security devices. Steel- or aluminum-cell ceilings and metal panels can be mixed for visual interest, and a wide range of finishes can be specified.
Another type of plenum mask is the baffle system, used to hide the structure above with a linear design element. Baffles give a space a very different look when viewed from different angles. Along with specifying steel or aluminum and the appropriate finishes, the depth and spacing of baffles must also be noted.
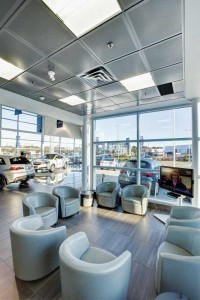
Photos © Bochsler Creative Solutions, Burlington, Ont. Photos courtesy Chicago Metallic Corp.
Planks, panels, curves, and trim
Used as design elements to cover large areas and provide accessibility, planks are panels that are three times longer (or more) than their width. The decision of attachment styles is largely based on the frequency of access to the plenum. Ideal for large public spaces and as design features in offices, planks can be formed into custom shapes and can be manufactured as solid or with perforations. The acoustical properties of planks mimic those of metal panels and the finish options are the same.
Also ideal for frequently accessed plenum areas, torsion spring panels allow maintenance staff access without taking the panel completely out of the ceiling. These products can be specified for flat or curved installations as planks or as panels, solid or perforated, and finished with paint, wood grain laminates or veneers. Due to the strength of the connection to the grid system, this type of system can be effective in areas concerned with seismic activity.
Well-suited for renovation applications, but not for most seismic areas, clip-in panels are easily removed and replaced into standard 24-mm (15⁄16-in.) suspension systems—this can be helpful for spaces that must quickly adapt to changing décor and tenant needs. The panels may be specified as square or reveal edge. The former conceals the suspension from view, while the latter exposes the suspension in a recess detail.
Panels are available in almost any finish and colour, but when reveal panels are desired, one should check for compatibility of existing suspension grid colour. Reveal or square, all clip-in panels are installed from the room’s interior over a new or existing ceiling grid. The ceiling grid must be a 24-mm style and completely square.
While several metal ceiling systems can be installed on a radius, other systems are specifically designed for curves. These are categorized as one- or two-directional curved systems, and concealed curved systems: A two-directional system refers to a ceiling system that uses exposed curved main tees and cross-tees. A one-directional system uses exposed curved main tees, and concealed systems hide the suspension from view. Each curved system forms undulating ‘ribbons.’ The peaks and dips of the ribbon’s curvatures are commonly called ‘vaults’ and ‘valleys,’ respectively. A minimal 457-mm (18-in.) radius is necessary for these valleys and vaults.
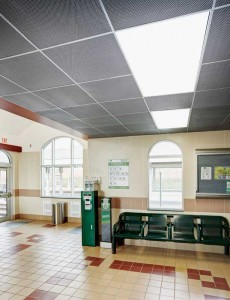
Curved systems are most often used in open-plenum ceiling applications. As with other metal ceiling systems, these curved systems’ panels can be solid or perforated, supplied with or without acoustical backers, in a full complement of finishes and colours, including simulated wood grain.
To allow ceilings to float in shapes and forms, manufacturers took another evolutionary step in the late 1980s by developing trim systems. These are custom-designed systems that can be used as ornamentation, to create a change of elevation in ceilings or to add drama. Trim systems can incorporate metal panel ceilings, acoustical ceilings, drywall, and open-plenum designs, even those with beam systems. Trim systems are specified as acoustical or drywall, in the desired colour, and in heights of 51, 102, 152, 203, 254, or 305 mm (2, 4, 6, 8, 10, or 12 in.).
Customized, specialized, or standardized
Customized ceiling systems require close co-ordination between the designer, specifier, manufacturer, and installing contractor. Blending multiple systems and finishes, the team can create one-of-a-kind spaces that reflect the occupants’ brand and personal tastes, while working within the timeframe and budget. The earlier the manufacturer is involved in the design discussion, the more easily it can help bring the vision to reality within the project’s scope. This collaboration may include full-scale mockups to minimize confusion and maximize the likelihood of a successful installation.
In addition to their design flexibility and ease of installation, the strength of metal ceilings makes them highly compatible with specialized applications, such as correctional facilities. In medium-security environments, one may specify a heavy-duty grid and steel panels that fit securely and resist removal after installation. High-security areas require steel planks held in place by heavy steel channels and tamper-proof screws. When specifying for security, it is important to consider the desired level of security, along with the interfaces with HVAC, lighting, and structural systems. One must also take into account whether the ceiling panels should be perforated or solid, steel or aluminum.
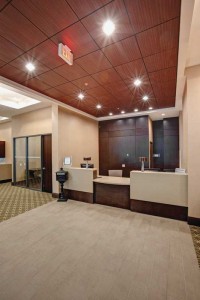
Metal ceilings can also be very suitable for cleanroom applications. To accommodate stringent cleaning regimen in these spaces, the panels can be used with several grid systems, including stainless and gasketed. These systems can be used in rooms as strict as Class 100. As with other specialized applications, one must be careful to consider the HVAC, lighting, structure, and interfaces. The decision regarding perforated or solid panels rests mainly on how the airflow through the room is designed.
Addressing more common applications’ daily needs for health, safety, and sustainability, standardized metal ceilings:
- are Class A fire-rated (per ASTM E84, Standard Test Method for Surface-burning Characteristics of Building Materials), but are not included in any Underwriters Laboratories’ (UL) time-rated designs;
- contain no fibrous material content;
- promote neither mould nor mildew growth;
- emit no volatile organic compounds (VOCs) when finished with baked enamels or powder-coated paints;
- offer low maintenance, as long as there is periodic cleaning to remove surface debris; and
- provide performance of 25 to 50 years, at which point they are 100 per cent recyclable.
(As mentioned, metal ceilings are not necessarily suitable for exterior soffits, however.)
Wherever a metal ceiling is specified, it is essential to check local codes for fire, seismic, and wind load, along with acoustic requirements and corrosion resistance needs. Working closely with the building team means collaboration not only among the designer, contractors and manufacturers, but also the owner, occupants, and maintenance staff. The shared goal is to ensure the ceiling system looks and performs as intended.
Edward Williams is a manager for Chicago Metallic Corp.’s metal ceilings unit. He draws from more than 30 years of experience in manufacturing ceiling systems for commercial spaces, partnering with owners, designers, and installing contractors. Williams is an affiliate of the International Interior Design Association (IIDA). He can be contacted via e-mail at williamse@chicagometallic.com.