Materials and engineering can differ drastically when specifying fabric-roofed buildings
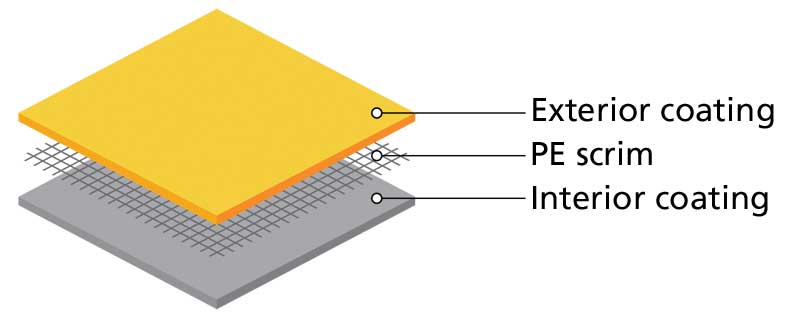
Rigid-frame provides design flexibility
Recent developments in fabric technology were preceded by a key advancement in fabric building framing when rigid-frame engineering was introduced several years ago. In contrast to fabric structures traditionally utilizing hollow-tube, open web truss framing, rigid-frame designs use the same structural steel I-beams found in most conventional construction projects.
The main advantage of this design is it provides far more engineering flexibility. Where web truss fabric buildings are often only offered in standard sizes, the rigid-frame process allows every structure to be designed to specific customer needs.
For example, if a building requires a hanging load supported by a frame (e.g. conveyor or fire suppression system), these parameters are accounted for from the very start by the finite element analysis software used to design the building. This allows engineers to modify and optimize each frame based on the actual loads that will be on it, rather than taking a worst-case approach and over-engineering an entire building to accommodate those loads.
When attempting to accommodate the same loads with a web truss design rather than a steel frame, suppliers may be forced to set up special jigging or change bay spacing between frames to handle additional loads, still with no guarantee it will achieve the desired result. I-beam construction simply uses variations like thicker steel, frame width, and flange depth instead of changing bay spacing. A different frame can be built every time without adding any cost to the design cycle.
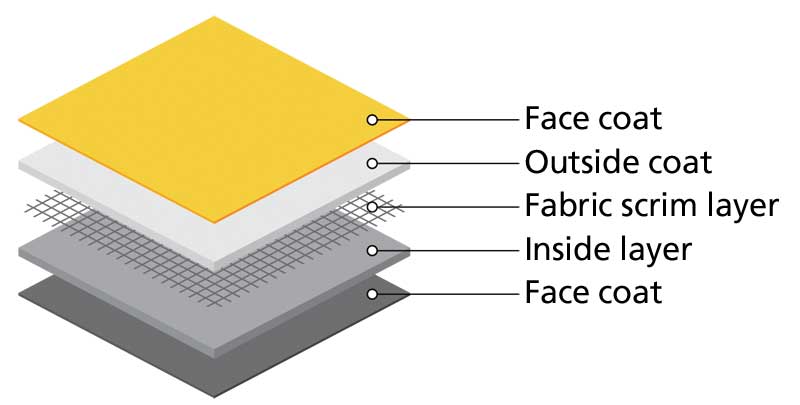
Beyond hanging loads, rigid-frame design allows the exact length, width, and height of a building to be specified down to the inch—an option not available with open web truss designs. Asymmetrical building designs, a wide variety of door options, variable column heights, insulation, ventilation, and many other loads and features can also be easily applied with rigid-frame design along with alternative exterior cladding options like steel or brick. Additionally, solid beam engineering provides straight sidewalls, clear spans, and tall overhead clearances—maximizing the usable square footage inside the building and allowing the owner to take advantage of additional interior space.
Securing fabric
No matter the type of frame a building employs, the attachment system used to secure the fabric can drastically impact the project’s lifespan.
Mono-covers, as the name implies, use a simple, large piece of fabric draped over the building and attached only at the ends and sides. This is a clear engineering weakness, as fabric is not designed to handle wind and other loads without support. During wind events, unsupported fabric has been known to tear, allowing the elements into the structure and, in extreme cases, causing building failure. Issues can range from unintended loading on the building frame to replacing the entire cover if any part of the membrane becomes damaged. Mono-covers are easy to install and relatively inexpensive, so they are suitable for small or temporary applications.
A panel attachment system is commonly employed. Fabric panels are shipped to the site in specified widths—6-m (20-ft) wide is typical, but it varies depending on the manufacturer—and then are slid through an aluminum keder channel to connect to each frame.
The traditional challenge with this method has been effectively attaching the aluminum extrusion channel to the frame. Many installers use self-drilling fastener screws (tek screws), which can lead to a variety of problems, including:
- tek screws sometimes get over-torqued during installation, causing the heads to shear off or the threads to strip out;
- motion-type pressure from wind or snow can make the extrusion susceptible to fatigue at pressure points because of the screw’s small heads and aluminum’s flexibility; and
- water can settle into the hole created in the aluminum around a tek screw, leading to corrosion.
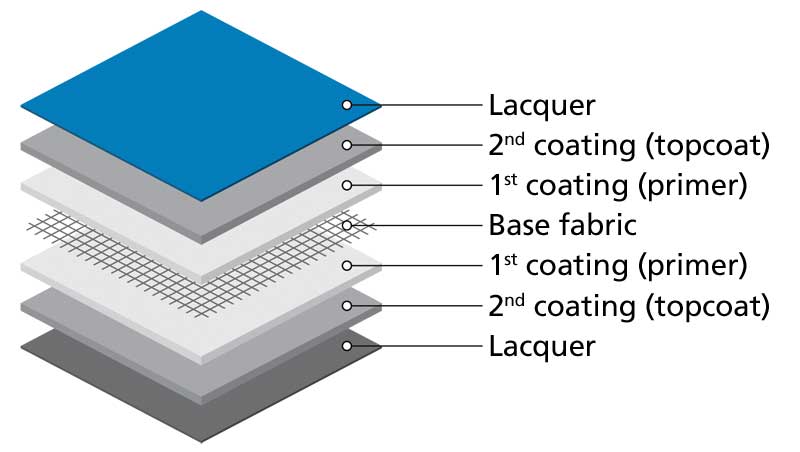
However, the biggest challenge or flaw in this process in the opinion of many suppliers is the need to disconnect secondary bracing and literally pull trusses out of plane to install the fabric as well as apply horizontal tension to it. Flexing the building’s frame after it is up leaves the building vulnerable to wind damage and safety concerns during installation.
Rather than depending on tek screws, one can employ a fabric attachment system with stronger 12.7-mm (1⁄2-in.) diameter bolts to clamp a keder rail to the top flange of the structural steel frame. This method contributes to corrosion-resistance and greater longevity, as it eliminates any areas where water could accumulate.
Additionally, it allows fabric panels to be pulled into place with the properly calculated tension in both directions—horizontal and vertical—without removing any secondary bracing or pulling the frame out of plane. The frame can be permanently in its place during panel installation, which helps maintain the proper fabric tension throughout the structure’s life cycle.
Installation using this method is also faster and safer. The time to build the framework for a fabric structure will be comparable to a traditional metal-clad building. However, once the framing is up, the fabric panels are easy to handle and quickly pulled in by an experienced crew, rather than painstakingly aligned and attached with multiple fasteners like metal panels.
The cladding portion of fabric building installation can take as little as one-third the time of a metal structure. When it comes to deciding between a conventional brick-and-mortar building and a fabric structure, there is a greater difference in erection time.