Managing the risks of efflorescence
By Michael Micalizzi, CTC
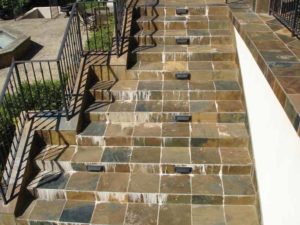
The costs of cleaning efflorescence from grout joints and tile surfaces can range from a lost day on a callback to a fortune, depending on the size and type of project on which it occurs. For example, to acid-wash tile on one large project, remediation costs exceeded $100,000 for labour and scaffolding. Additionally, the owners were highly concerned with acid-wash residues over window trims and plantings because the cleaners used to remove efflorescence are acidic and could damage plantings and leave residue. Further, the metals on the exterior were a primary concern due to the acids. The owners also expressed fears regarding risk to occupants entering and leaving the building.
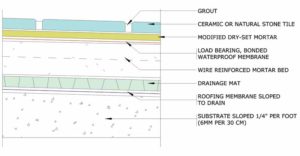
Often, these issues with efflorescence lead to hiring consultants and attorneys. In these disputes, the general contractor (GC) and tile contractor will not accept responsibility for efflorescence as the design team approved the installation products and configured the building components, such as drip edges, that may have led to the problems. Manufacturers disclaim the occurrences unless materials that will not contribute to it are used. In this actual event, the contractor substituted a lower-grade grout when the specified one was not readily available. He denied, it of course, but laboratory analysis was able to reveal the substitution.
Efflorescence occurs when mineral salt deposits that have leached or migrated from cement and masonry materials are carried to the building’s surface in moisture vapour. These minerals occur naturally in Portland cement and, when dried, appear as a white film, powder, or crystal. Many kinds of mineral salts have been detected in multiple samples of efflorescence, including sodium sulphate, potassium sulphate, sodium carbonate, calcium sulphate, sodium bicarbonate, and calcium carbonate.
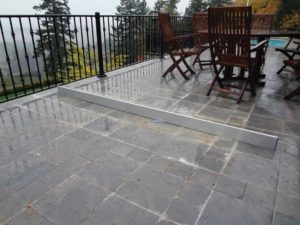
The tile industry has experienced efflorescence for a very long time. Unfortunately, building owners and GCs often believe it is solely the tile contractor or installation material supplier’s responsibility to prevent it from happening, and remove it when it occurs. Although poor installation methods can cause it and certain products are more susceptible to it, in many cases, building design and product selection causes or contributes to the problem in both interior and exterior applications.
New concrete and mortar beds provide a source for efflorescence in a wide variety of projects. For example, when porcelain tiles are installed in exterior applications, the mortars used are polymer-modified, so when standard-setting, Portland cement-based mortars are used instead of rapid-curing, calcium aluminate-based types, they retain moisture for an extended time, adding to the possibility of salt migration. Note, standard-setting and rapid-setting mortars are both polymer modified, however, the cements used in the two are different. Calcium aluminates are preferred as they set faster, and contain very little sources of minerals that effloresce, like lime.
To prevent the issue of salt migration, it is important to address the main causes resulting in or contributing to efflorescence, namely:
- tile installation practices;
- choice of installation materials; and
- building design options and installation flaws.
Design/construction professionals will likely be familiar with many of these issues, but unfamiliar problems may catch a team by surprise.