Managing the risks of efflorescence
Project design options and flaws
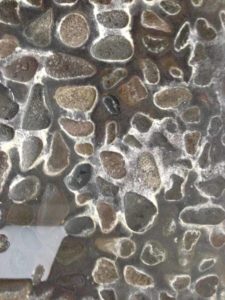
Numerous design choices can lead to the formation of efflorescence. One of the most common is reducing the substrate and assembly pitch from 6 mm in 300 mm per foot to 3 mm (1/8 in.) in 300 mm per foot. This is often proposed with accessible showers and exterior decks/balconies where the elevations have not been properly accounted for or the design team feels the pitch is too severe. As shown in Figure 2, this reduction severely impacts the margin of error for even the best tile contractor due to acceptable variances in the installation and the tile itself. The actual pitch could be reduced to 0.7 mm (1/32 in.). Figure 2 also shows allowable variances in the tile manufacturing, lippage tolerance during installation, grout (no standard for depths), etc. What makes things worse is the tile and natural stone recommended for these areas are purposely profiled, rough, or clefted to provide adequate slip resistance. That also means they will slightly slow down water flow or prevent water from draining, resulting in ponding and formation of salt deposits.
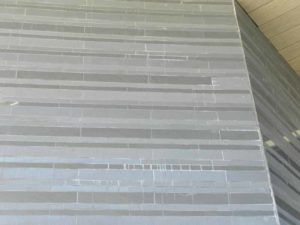
Construction schedules and budgets all too often push the limits on risks with regard to surface preparation, curing timeframes, or costs to add products that would manage efflorescence and avoid potential failures. Not correcting variations in substrate pitch to effectively evacuate water, not providing protection from the elements until the installation products are cured, and filling pools and water features too soon are just a few examples of real life conditions. Additionally, rapid-setting mortars and cement grouts or noncementitious grouts and waterproofing membranes used in a system may be more expensive, but can limit risk of efflorescence. In the author’s experience, waterproofing or moisture mitigation is often ‘value engineered’ out of the specification, proper sloping is eliminated, or tile is direct bonded over fresh concrete. Most tile contractors have been told at one time or another,
“I need it installed now! Just put it in or I will have to get someone else.” In such situations, the possibility of efflorescence is not considered.
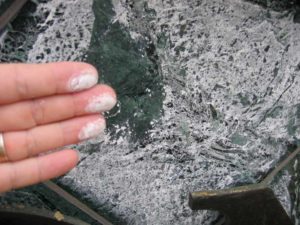
Exterior tile roofing and façades require a design able to effectively evacuate or shed water. Another common flaw is poor detailing of drip edges or the elimination of them altogether at a rooftop or around windows. When water is allowed to seep behind a tile, it will eventually find a way out, bringing with it minerals and salts. An extended drip edge and gutter will help keep water off the sides of the building (Figure 3). Also, at times, a stone façade is chosen that does not allow for grout in the joints. It can be expected efflorescence can occur in this design, as water is freely allowed into the bonding mortar and substrate, allowing easier salt migration.
Proper design of movement joints in every assembly relieves the stresses of normal building movement from deflection, loads, and thermal changes. When expansion joints are inadequate, tile expansion and the resulting compression of joints cracks grout or loosens tile, creating fissures for water and moisture to pass through and draw out minerals from below. It should also be noted, dark-coloured tiles absorb and retain much more heat, a factor leading to increased expansion and fractured grout without adequate movement space.
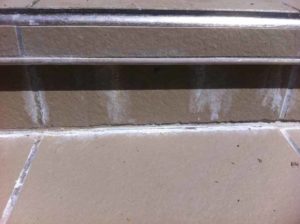
Irrigation systems have also been known to create cycles where the assembly is saturated and dries repeatedly. Typically, sprinklers supply water in the early morning, and as the sun rises, heat draws out moisture from grout lines along with minerals and salts. Improper grading also impacts water flow. Worse, some water used for irrigation could have greater potential to cause efflorescence if it is reclaimed and rich in minerals.
Since anyone’s actions on a project could cause the appearance of efflorescence, it should be an important consideration for every installation. Each person involved should reflect on what steps can be taken to manage risks. Important strategies include performing a mockup to evaluate the details related to the potential for future efflorescence, such as pitch or the reaction of a standard grout over a fresh mortar bed, along with incorporating industry best practices, such as creating adequate substrate and waterproofing pitch, edge detailing, and acceptable adhesive mortar coverage. Not to be overlooked is heating or tenting the installation in extreme temperatures and providing protection from weather during curing. The material supplier will also have suggestions and warranty requirements for the product and assembly installation conditions and protection.
When working on a fast-track project or noticing anything that could cause a problem, one should notify the whole team of the possible risks and determine who is responsible for the remediation.
In the words of former U.S. general Colin Powell, “There are no secrets to success. It is the result of preparation, hard work, and learning from failure.”
Michael Micalizzi, CTC, is the senior director of technical services for Custom Building Products, with more than 33 years of industry experience. In his role, Micalizzi assists industry professionals with recommendations on commercial projects for various installation challenges. Prior to becoming involved in product technology, Micalizzi owned a tile and stone installation company in New Haven, Conn. He currently serves on technical committees for the Tile Council of North America (TCNA), American National Standards Institute (ANSI), ASTM International Materials & Methods Standards Association (MMSA), National Tile Contractors Association (NTCA), and Natural Stone Institute (NSI). Micalizzi can be reached easily via e-mail at mmicalizzi@cbpmail.net.