Managing noise in a fully digital hospital environment
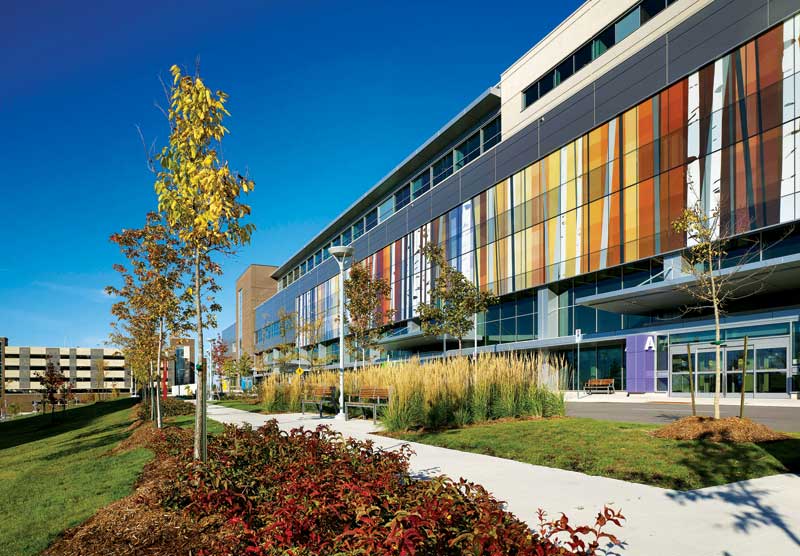
Photos © Tom Arban
Streamlining staff communication in order to reduce noise
Reducing the amount of communication between staff may seem counterintuitive in providing good care, but a review of the process showed the communication system was causing the unnecessary relay of information to people not directly involved in care. By introducing new approaches, the design team was able to ensure communication was directed to the healthcare practitioners and staff who actually needed the information.
Healthcare practitioners and staff each have their own HRH-specific personal device (PD) that manages all forms of work-related communications to their specific job during their shift. Reducing the amount of information coming to a caregiver irrelevant to their work helps fight alarm fatigue.
The traditional overhead public address (PA) system used to communicate with healthcare staff has also been eliminated at HRH. When a code alert occurs, it is broadcasted to specific healthcare practitioners through their PDs. Each team member is then required to acknowledge and respond to the alert. If there is no response, the alert can be escalated to other healthcare providers until the problem is solved. This staged alert eliminates the ever-annoying code calls broadcast to the entire hospital population and increases safety by requiring acknowledgment by healthcare providers. It meant HRH did not need to install a PA system, leaving only the life safety annunciation system for public safety announcements and redundancy.
Updating the nursing station
Patients always have the option of pressing their nurse-call button in their room. However, a simple press of the button in a traditional hospital setting sets off a chain reaction of noisy follow-ups before the patient ever sees a nurse.
In a traditional setting, a patient pressing the nurse-call button triggers an alarm at the nurse’s station, which is usually located in the middle of a floor. It means the request is sent to the nurse at the station who may or may not be involved in the patient’s care. The message may then be relayed to the appropriate nurse.
HRH’s interoperable systems send the call directly to the PD of the nurse caring for the patient, eliminating the need to convey a message first to the main station. The direct communication reduces potential errors in the relaying of the messages and allows a nurse to give the patient direct instruction or timeline for when they can attend to their needs. It also allows the nursing staff to be more efficient with their movement around the unit. For example, the patient may need supplies from an area the nurse will be passing by on the way to the room.
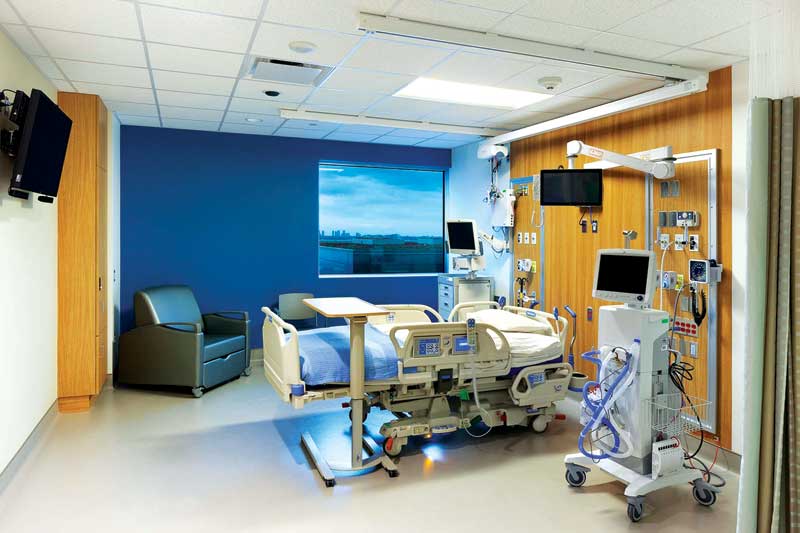
Not only does this reduce some unnecessary noise, but it also provides consistent care to a patient. It reduces staff fatigue by allowing them to manage a patient’s request immediately or based on their location on the floor. The nurse’s PD can also be connected to the patient’s life support and vital monitors so it generates an alarm when the data readings hit critical levels, triggering immediate attention from the nurse.
HRH went even further and redesigned the traditional station. The hospital’s stations are located in the central core of the floor footprint—one at the far end of the unit, one at the middle, and one at the entry. This brings the staff closer to the patient rooms and reduces the number of staff at each station. Along with glass screens to dampen speech transfer, ‘team rooms’ are available adjacent to the nurse’s station. These spaces are equipped with conferencing technology and provide a private place for team discussions.
Building a patient room for quiet healing
To adhere to its patient-centred care philosophy, HRH wanted to make the patient room quiet and comfortable. Comfort in the patient room was enhanced with room-side monitors, integrated bedside terminals, and display monitors. This technology allows patients to connect with family through social media and Skype, order food, access entertainment, or review their medical charts. (HRH also permits family members to visit 24/7.)
The room allows a healthcare practitioner to complete automated charting, increase accuracy in recording patient information to the medical record, and review diagnostics and imaging with the patients on the screens at the bedside. It also means medication can be scanned via barcode to ensure it is being correctly administered.
With the added technology, change in healthcare operations, integration of family in the room, and access to the outside world, the patient room had the potential to become noisier and more obtrusive—therefore, the sound in the room needed to be managed. The patient room was carefully planned to provide a comfortable healing space. Eighty per cent of patient rooms are private—improving infection control and providing a quieter environment to speed recovery. The family zone is located on the outside wall of the room so it does not interfere with direct care providing space, the patient access path or the corridor. This allocates a quiet space for the family to be beside their loved one that does not disrupt care, and reduces sound transmission into adjacent spaces through the corridor.
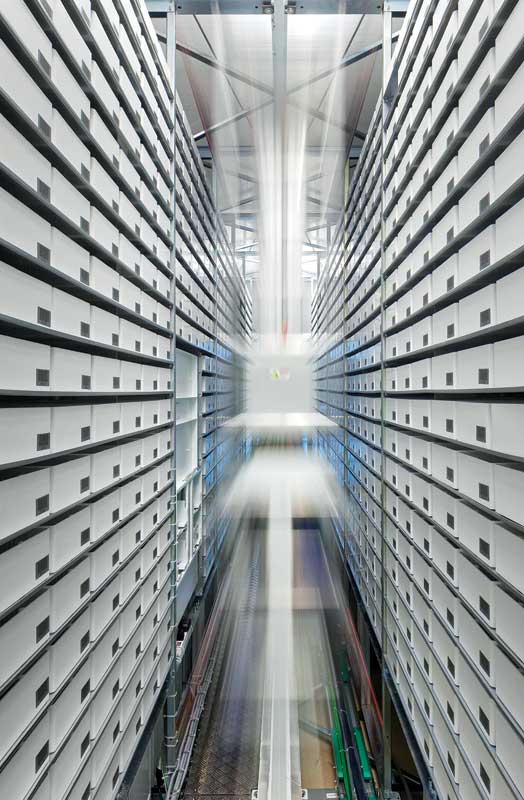
Controlling environmental noise
Aside from the noise concerns within the room, the HRH design team also had to address noises from exterior and operational sources having an impact on the building. HRH is located on an urban site near North American’s busiest highway (i.e. Macdonald-Cartier Freeway or 401), causing concern of transfer of traffic noise into the patient rooms. Patients, supplies, and carts are transported on a more frequent basis to take advantage of just-in-time healthcare practices and delivery equipment.
Automated guided vehicles (AGVs) are robots programed to deliver supplies to the floors from the central storage area in the basement. Pneumatic tubes for drug and test samples delivery and the 460-mm (18-in.) diameter automated disposal chute system had the potential to transfer noise. The traditional hum from the HVAC system also had to be considered.
Patient, family, automation, and outside noises all need to be controlled, contained, and isolated from adjacent patient rooms. To accomplish this, some simple design strategies were implemented. For example, the exterior wall assembly is precast concrete, which helps dampen road noise from the highway. The HVAC equipment in the ceiling was located above the corridor, isolated from the patient room; further, larger ducts reduced the hum created by the velocity of the air being delivered.
The construction of the rooms were designed to meet sound transmission class (STC) 50, with wall assemblies and door-seal requirements. This means the sound from one space would be mitigated by roughly 50 decibels before reaching the space across the partition. This was especially challenging for patient room partitions that included back-to-back headwall systems. Details like quiet door latches on the patient room door and silent sliders with quiet stops on surface-mounted sliding washroom doors were implemented.
Extra care had to be taken for the design of the patient rooms to ensure the acoustic performance of the walls was not compromised by the presence of back-to-back headwalls. Specially developed acoustical reinforcement was applied to the detail on the headwalls to address a potential noise flanking path. Post-construction and mockup tests were used during the design and construction to verify the adequacy of the solution.
The floor is also designed not to transmit footfall by stipulating vibration criteria. AGVs are confined to a staging area in the core and designated corridors in the basement away from patients and public. Different wheels on the carts were tested to reduce the sound of the carts as the AGVs transported them. The pneumatic tubes are located at the nurse’s stations at the centre of the patient floor with padded receivers, and the chute is in the service core with the horizontal run in the basement ceiling space. All these strategies isolated the noise from critical patient and staff areas.
Conclusion
The Humber River Hospital’s vision of a fully digital hospital changes patient care and greatly enhances the healing experience and comfort. Through proactive design and thinking, it has successfully integrated technology to create a better healing environment. HRH will be looked on as a shining example by other healthcare facilities looking to introduce new technologies while keeping the quiet patient healing environment intact.
Jeff Churchill is a vice-president and architect with HOK—a global design, architecture, engineering, and planning firm that serves clients with four offices across Canada. With more than 16 years of experience, he specializes in leading project teams for large complex building types such as healthcare and science and technology. Churchill is a leader in the public-private partnership (P3) industry and often participates in initiatives setting new levels of effectiveness in the procurement process. He can be reached at jeff.churchill@hok.com.
Payam Ashtiani, P.Eng., is a professional engineer and a principal at Aercoustics Engineering Limited, a firm specializing in fostering innovation in acoustics, vibration, and noise control. With more than a decade of experience in acoustics, he works with architects to solve noise reduction and noise mitigation issues for a wide variety of projects including healthcare facilities and residential planning. Ashtiani can be contacted via e-mail at payama@aercoustics.com.