Making music in an old warehouse
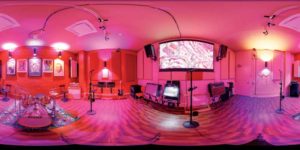
By Steve Titus, P.Eng.
There is a critical shortage of rehearsal space in Toronto. In an era when developing a condo or office building is more lucrative, creating spaces for musicians is not a priority for property owners. However, Lynx Music is looking to stem the tide of losses and produce a space for musicians to enjoy their trade or hobby.
The company has opened a new 929-m2 (10,000-sf) music rehearsal and multimedia production facility in west Toronto by converting an old warehouse. It combines music rehearsal spaces with a comprehensive recording and post-production suite as well as a film and photography shooting space.
Challenges
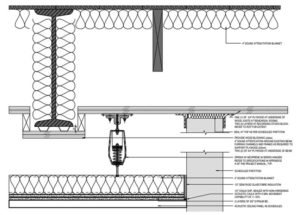
Image courtesy Aercoustics & Gensler
Usually, rehearsal and recording spaces have different objectives. Recording requires soundproofing to ensure the quality of sound is pure. Rehearsal spaces are a place to create, test, and play with good acoustics but without worrying about recording.
For Lynx Music, the desire to offer both rehearsal space and recording studio was a challenge. While the project’s engineering team has worked on acoustics for music production and rehearsal studios separately, this was the first time they have encountered a design wanting to incorporate both spaces. It meant finding the right balance to meet the different acoustical requirements so musicians could play without worrying about sound. With multiple potential noise transmission paths to evaluate and test, Lynx Music became a technically demanding project but allowed for some outrageous engineering to ensure the client had a space suitable for all its creative users.
The design requirements for recording and rehearsal venues can be simplified as follows:
- keep exterior sounds from entering the recording studio; and
- keep sound within the studio and rehearsal space from bleeding into neighbouring rooms or even buildings.
When working on such a facility, design professionals need to understand what happens to sound energy in this type of space. It can be absorbed, reflected, or diffused. In most cases, the goal is to minimize the noise transfer by maximizing the sound isolation of demising partitions, and also to include acoustically absorptive finishes within the rooms. While old warehouses can be an interesting space for interior designers, the lack of walls causes some unique acoustical considerations and construction issues. The exterior of this warehouse is old masonry, beneficial because heavy brick and stone limit sound transmission to nearby buildings. However, the interior posed some problems. The floor plan provided limited space for wall, ceiling, and floor assemblies. This can be a challenge as developing sound isolating rooms can require a lot of space. This is also why most rehearsal facilities are the equivalent of garages with little to no thought to the acoustics of the space. Acoustically designed wall, ceiling, and floor assemblies can manage or mitigate noise transmission. So, not being able to add them immediately introduced challenges.
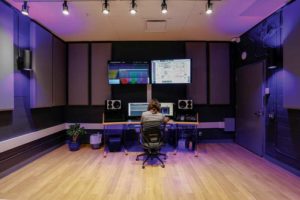
Photo © Semco Salehi
The interior timber floors and steel structure also added to the acoustic difficulties. A limited loadbearing capacity reduced the ability to develop traditional designs. In fact, neither the lightweight timber floors nor the steel frame was ideal for creating soundproofed studio spaces. The design team had to approach the existing structure and its limitations with open minds to develop suitable spaces, balancing the performance requirements with technical and budget constraints.
The design
Lynx Music is a two-storey facility consisting of nine rehearsal studios and a fully floating recording studio block featuring a live room, control room, vocal isolation booth, and a production room. Each area had its own acoustical requirements but needed to be part of a cohesive space.