Making History Again: Repurposing Maple Leaf Gardens
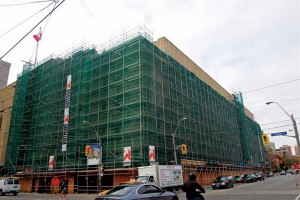
Throughout the restoration, the existing structure and exterior walls were remotely monitored on a continuous basis for any movement through the innovative use of a proprietary computerized fibre-optic technology. Engineers worked closely with the demolition contractor and exp to fine-tune the computerized monitoring technology setup to ensure alarms would sound and work could be stopped immediately if movement or vibration exceeded a pre-determined safety threshold.
Once the new interior structure was constructed and connected to the original exterior façade systems, the temporary bracings were carefully removed. Since stability was now provided by the new structure within the original shell, large openings could then be cut into the corner buttresses to accommodate a parking ramp and main entrance. The new loading-dock door installed through the north wall required removal of four concrete columns that supported both the north wall and the roof. In the end, exp engineers were successful in solving the formidable structural engineering challenges of the historic building’s redevelopment.
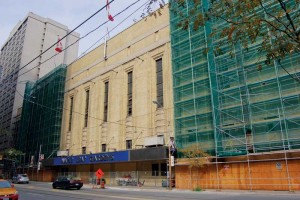
Photos courtesy ERA Architects
Retaining heritage elements
ERA Architects was retained as the heritage architects at the project’s earliest stages to consult on the range of modifications to the original building, which is designated as a National Historic Site under the auspices of Parks Canada. ERA supervised the alterations to the designated heritage fabric and directed the restoration of the retained heritage elements. The company also prepared a heritage interpretation plan (HIP) to ensure the building’s history was celebrated throughout the spaces that would be occupied by the new owners. Additionally, ERA designed the replicated Carlton Street marquee using archival photographs.
Will MacIvor, ERA project architect, says about one-fifth of the bricks were repointed during the restoration. In cases where bricks were damaged or cracked, much of the replacement material was salvaged when it was removed to accommodate the new openings that were created for loading bays and air intake vents. When additional brick was required, salvaged brick that was tinted slightly to match was acquired from the R.C. Harris water treatment plant located in eastern Toronto that was built at approximately the same time as the Gardens.
According to MacIvor, the original 1931 drawings helped ERA with various aspects of the design, including the ornamental metal work components with the horizontal banding and octagonal window drops. The upper-level fenestration components were refitted with double-glazed vintage steel industrial windows. ERA restored 12 original windows while the remaining units were manufactured to match the original ones.
MacIvor also explained not all elements were kept entirely intact because of the dramatic structural modifications to the interior.
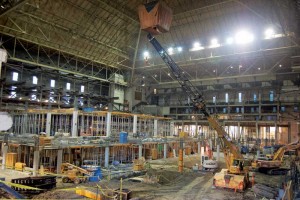
Photos courtesy exp
Opening the new Gardens
Although the construction speed garnered most of the headlines while it was being built, construction of Maple Leaf Gardens was a marvel in the application of building science expertise.
Few realize almost all enclosed stadiums and arenas have roofs supported by columns that obstruct the view of at least some of the spectators. Maple Leaf Gardens is one of the few that had none. This was accomplished in an era when computers were unavailable and the innovative roof design involved constructing trusses where one corner was ‘pinned’ while the other three rested on rollers, allowing the structure to expand and contract in response to temperature changes.
Designing a roof at that time with the weight of 0.67 kPa (0.097 psi)
was unheard of, and this was just one of the innovations in building science and technology that almost certainly reflects Canada’s long-standing reputation as a world leader in cold-weather building science.
“We are very proud to have been involved in the redevelopment of this historic landmark,” says David Tippler, vice-president of Building Design. “While the technical challenges were rewarding to us as engineers, the opportunity to restore the vibrancy of this building for the community is even more gratifying.”
Conclusion
Maple Leaf Gardens was built for approximately $1.5 million in 1931. This significant adaptive reuse project, aside from preserving and restoring one of Toronto’s best-known landmark buildings, can be expected to generate several million dollars in economic activity for the city and the immediate neighbourhood over the next 20 years and beyond.
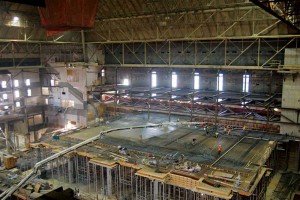
Although it seldom receives recognition as such, construction is Canada’s largest industry and biggest employer. The continuing investments, combined with ongoing efforts to repurpose the existing building stock and commitment to designing efficient, sustainable buildings is almost certainly one of the factors that has allowed Canada’s economy to perform so well relative to many other nations. The remarkable restoration of Maple Leaf Gardens is a case in point.
Brian Burton is an R&D specialist for consulting firm exp. He has published more than 450 articles on building and landscaping science. Burton writes a regular column for Glass Canada entitled “Fenestration Forum” and is a regular contributor to Canadian Home Inspector Magazine. He was recently appointed to Canadian Standard Association’s (CSA’s) Fenestration Installation Technician Certification Programs Personnel Committee. Burton can be reached via e-mail at brian.burton@exp.com.