Making History Again: Repurposing Maple Leaf Gardens
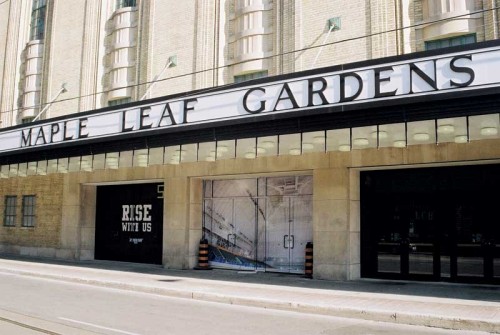
By Brian Burton
When the Toronto Maple Leafs moved into the Air Canada Centre (ACC) in 1999, not only was the world-famous Maple Leaf Gardens venue left empty, but there was also silence at ice level and in the seats for the first time in more than 60 years.
This classic arena––the last ‘cathedral’ still standing of the six original National Hockey League (NHL) teams––can boast some of the most incredible sports and entertainment attendance records in the world. Between 1946 (when one could purchase an upper-tier seat for 95 cents) and 1999, there was not a single unsold seat in the house. In total, more than 100 million patrons have witnessed events in the building.
Built in 1931, during the depths of the Great Depression, by sand and gravel tycoon Conn Smythe, the Gardens still retains the same appeal it had during pre-expansion times when the ‘Gashouse Gang’ (the 1930’s Leafs were called this for their off-ice antics) was the toast of the NHL.
Fast forward to 2012 and the famous facility at 60 Carlton St. has been remarkably transformed. It has been repurposed as a ‘state-of-the-art’ multi-purpose retail venue and athletic centre after Ryerson University partnered with Loblaw Companies Ltd., to transform the structure into a multi-use building. In doing so, they also managed to preserve and restore the most significant architectural heritage elements, including:
- 80-year-old ‘Art Deco’ brick façade;
- domed roof;
- windows;
- light fixtures; and
- iconic marquee above the main entrance.
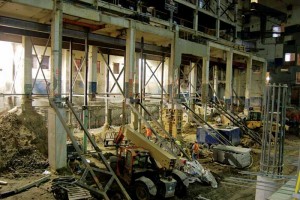
Photos courtesy exp
Cashbox on Carlton Street
This revitalization of one of Canada’s landmark buildings was much more than just a cosmetic renovation to an existing building. Construction on what eventually came to be known, with good reason, as the ‘Cashbox on Carlton Street,’ began at midnight on June 1, 1931. In what is still considered to be an unparalleled accomplishment, the structure was built by 1200 workers in 165 days.
The original structure required 750,000 bricks, 2006 m3 (850,000 board feet) of lumber, and 22.5 km (14 mi) of underground piping to control the ice surface temperature, all of which were purchased at bargain prices because of low demand brought about as result of the depression.
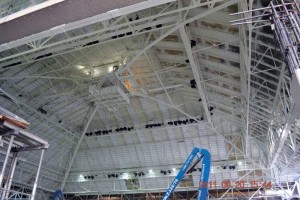
Photo courtesy exp
The principal architectural firm for the design was Ross & Macdonald––designers of many well-known château-style railway hotels of the early 20th century. Regardless of whether the building was a railroad station, hospital, bank, or hotel, the client’s expectations and building function were first and foremost. In the case of the Gardens, a principal design criteria was a good view of the action.
Structural engineering and building science challenges
The building, 13 storeys high at the top of its roof, features a concrete seating bowl topped with a structural steel-arched dome roof. The seating bowl––for 13,542 ticket-holders––by way of its shape and placement, provided lateral stability to the roof supported by immense concrete columns integral with concrete stair towers at the four corners of the building and exterior walls. Demolishing the seating meant both the exterior walls and roof would lose their essential lateral support.
The principal challenge was to retrofit the building’s structure and interior, while ensuring the exterior walls did not collapse during seating, concourse floor area, and box seat removal. Replacing these components was to be a grade-level Loblaws supermarket and two additional floors for retail and athletic use, including a second-floor gymnasium, a third-floor ice rink, and below-grade parking.
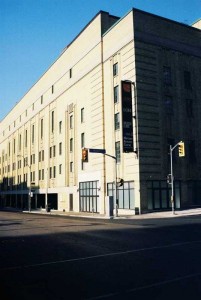
Photo © Brian Burton. Photo courtesy exp
Ship in a bottle
The project entailed solving a variety of complex structural engineering challenges. The structural and geotechnical consultant for the renovation was exp—a multi-disciplinary firm that had been associated with the facility since the early 1960s and had intimate working knowledge of the existing structure.
“Re-adapting the Gardens could be compared to building a ship in a bottle, except the bottle already contained a ship which, by necessity, had to be dismantled piece by piece—without breaking the bottle,” explained Paul Sandford, exp project principal engineer.
While the original building interior was demolished and removed, the stability of the structure and exterior walls was maintained by installing temporary steel bracing within the original concrete frames at the building’s east and west sides. At the north and south ends, large box trusses––3.4 m (11 ft) deep, 8.5 m (27.9 ft) wide, and spanning more than 66 m (216.5 ft)––were installed between the existing buttresses at the facility’s corners.
With the new underground parking level specified 3.4 m below-grade at the south side and up to 7 m (23 ft) below-grade on the north side, significant portions of the exterior foundation walls required underpinning using a combination of traditional underpinning, helical piles, micro-piles, and soil-nailing. At the corner buttresses, which supported the entire roof’s weight, temporary caisson walls were installed adjacent to the footings to laterally support the soil under them while the surrounding area was excavated down to the parking level. Basically, an entirely new structure was fabricated inside the four walls and connected to the existing structure to provide lateral support for the restored building.