Maintaining building quality control with fabric cladding
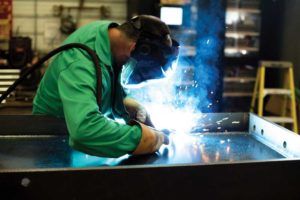
Putting it together
Much like the design and manufacturing phases, the final piece of fabric building QC comes down to a combination of “how” and “who” questions:
- How is the fabric attached to the building frame?
- Who is erecting the building?
Many fabric buildings use a panel attachment system, commonly featuring 6-m (20-ft) wide fabric panels, which are connected to each frame by sliding through an aluminum keder channel.
A traditional method for attaching the extrusion channel to the frame was using self-driving screws, which were problematic for a variety of reasons, including the fact that water could settle in the hole created in the aluminum around a screw, eventually causing corrosion. An even bigger flaw emerged when some buildings had to have trusses twisted out of plane to install the panels and apply horizontal tension to the fabric.
Beyond the attachment method, the actual people handling the installation—and their experience or lack thereof—can come into play. Many suppliers hire local subcontractors to have their buildings erected on-site. Some manufacturers leave it to the customer to hire their own assembly team.
Some manufacturers have in-house fabrication crews, which is an ideal method of construction for this building type. Their internal knowledge and expertise make it easier to get every detail right, helping ensure a complete chain of QC from start to finish.
Going beyond
Fabric building companies that have invested in manufacturing facilities and experienced personnel have an inherent advantage in maintaining QC. They also are more likely to communicate and interact as a cohesive team, using feedback not only to improve existing processes, but to continually innovate into new areas.
Rigid-frame fabric buildings are on the rise in new applications. PVC fabric is now a cladding option for complex structural designs that would have been difficult to conceive five years ago. Improvements in technology and methodology have opened more doors for tension fabric structures. The ability to handle more tasks internally—thereby elevating the QC of every project—is making it possible to approach these new horizons successfully.
Authors
Ben Fox is the founder and president of Legacy Building Solutions. Along with two-plus decades of fabric building experience, he notably created the process for applying fabric cladding to rigid steel frames. He can be reached at bfox@legacybuildingsolutions.com.
Ellie Fox is the chief operating officer of Legacy Building Solutions. With 10 years of experience in the fabric building industry, she oversees operations throughout the company. She can be reached at efox@legacybuildingsolutions.com.