Maintaining building quality control with fabric cladding
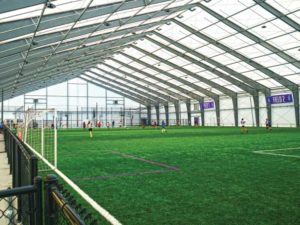
The move toward using rigid-frame I-beams and metal building software (MBS) instead of web truss instantly brought more credibility and engineering certainty to fabric buildings. Engineering professionals were now able to look at the plans for fabric structures, universally understand them, and trust the I-beam frame would stand the test of time.
The change allowed for more engineering flexibility and customization. Web truss designs were typically only available in standard, off-the-shelf size configurations, always in a basic hoop shape. Rigid-frame designs, by contrast, begin with a clean sheet and can be fully optimized from the beginning to meet an end user’s exact needs and specifications.
Using finite element analysis (FEA) software, designers can modify the structural framing of a fabric building in numerous ways such as conventional brick-and-mortar buildings. Features such as lean-tos, offset peaks, and variable column heights can be incorporated. Thicker steel beams can be applied where needed to account for hanging or collateral loads at specific points on the frames, rather than over-engineering every beam. Rigid-frame buildings can also be designed much larger than web truss structures, making it possible to accommodate user needs such as higher ceilings or longer clear spans.
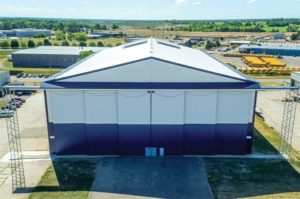
Taking control with framing structure
It is one thing to have greater building design capabilities, but it is another for the product to be correctly fabricated as intended. In addition to offering a superior I-beam framing structure, some manufacturers have sought to enhance their QC measures by bringing their steel beam manufacturing in-house, rather than outsourcing.
QC has become a challenge for the fabric structure building type because the materials and components are sometimes shipped from different suppliers directly to the jobsite. It is important to perform a quality evaluation of the materials prior to the start of construction.
With the goal of ensuring better QC, leading manufacturers have invested in their own on-site facilities and employ their own full-time certified welding inspectors (CWI) to thoroughly inspect the varying I-beams for every project. Having inspectors on site has provided manufacturers with the flexibility to accommodate requested modifications which impact the final design required for the steel frame.
Fabric self-fabrication |
The story of how epoxy coating became more cost-effective is not unique in recent fabric building history. Certain polyvinyl chloride (PVC) fabric materials have followed a similar path to affordability, after previously having been reserved mostly for higher-end building projects due to higher costs.
Polyethylene (PE) fabric has traditionally been the most used material for cladding the roofs and sidewalls of tension fabric structures. Compared to the heavier yarn of PVC, standard PE material is relatively thin, with three total layers comprising a fabric weave and top and bottom coatings. Its life expectancy is about 15 years. A newer PVC on the market has seven material layers to provide increased tensile strength and longer service life. Further, as more in-house fabrication emerges in the industry, fabric structure manufacturers can handle all the necessary panel cutting and preparation of this fabric themselves, helping them to now offer PVC cladding to clients at lower prices than in the past. Going hand in hand with lower costs is a better level of quality control (QC). Manufacturers can cut PVC fabric panels to the desired specifications, rather than relying on a third party to handle the task. In-house personnel can review drawings and paperwork prior to fabrication, and in cases where they work under the same roof as the design engineers, can immediately discuss any issues without causing major project delays. Having their own controlled environment for fabrication is another advantage toward ensuring quality. Common procedure is for fabric to be tested at the beginning of each day, at each new roll, and during any significant temperature changes observed throughout the day. Humidity and temperature are kept as consistent as possible in the plant as fabric panels are produced, and the final fabric panels can then be examined by the original building manufacturer before shipment. |