Lightweight rear-ventilated rainscreen façade thickness 101
Strength versus panel thickness
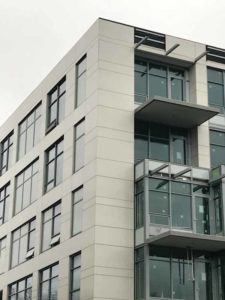
A key part to answering questions on panel thickness is to clarify the expectations of a building façade in terms of strength.
Outside of the resistance to solar exposure and moisture from precipitation, façade systems are expected to withstand the effects of wind-born projectiles, such as rain, hail, and minor debris. In most cases, with a properly supported substructure (explored later in the article) behind the façade material, the actual system thickness needed to physically withstand expected environmental impacts is usually thinner than what manufacturers provide. A common example in commercial building construction is the use of steel siding, which can be as thin as 0.70 mm (24 ga), yet is considered sufficient to withstand all but the most extreme forms of impact from precipitation.
LWRVRS systems are typically produced in thicknesses well beyond the strength expectations for a façade system. The material production process often dictates the minimum thickness available. For example, GRFC façade materials—typically cast using shallow moulds—will have a minimum thickness of 13 mm (½ in.) or more. In contrast, PSS panels are produced as thin as 6 mm (¼ in.) for façade systems. In both cases, the minimum thickness set by the manufacturing process produces a material of sufficient strength for most common façade assembly exposures to climate.
In some project applications, the façade is expected to contend with additional forces, such as impacts from non-environmental related sources and/or nearby human activities. At this point, the panel thickness versus strength question becomes more relevant. However, it still remains somewhat subjective and generates more questions, such as:
- what kinds of impacts;
- how intense;
- how frequent; and
- what level of ‘damage’ is allowed afterwards?
Most LWRVRS façade systems have a high degree of resistance against moderate unintended impacts, like a stray soccer ball kicked form the nearby school yard. However, as the majority of drive-thru buildings can attest, the repeated impact of automobile mirrors on the sides of unprotected façades will eventually, at the very least, result in some surface damage.
While fibre cement and phenolic are considered to provide a good degree of impact resistance due to their high density or minor flexibility (or combination of both), the primary function of these materials is to serve as the façade component of the building envelope assembly. Increasing the material thickness of a LWRVRS system for improving the impact resistance of the façade may not be the most efficient method. Often, the location and spacing of the substructure components behind the façade will make a more significant contribution to improving the impact resistance of the overall assembly compared to the cost of increasing the panel thickness.
For high-risk situations, railings or barriers (e.g. steel posts at drive-through corners) may provide a better long-term solution for protecting the building envelope than relying on the durability of façade material alone.
Panel façade substructure and wind loading
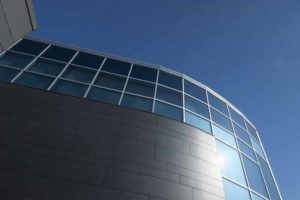
Behind the LWRVRS façades is a substructure system creating the rear-ventilated rainscreen cavity that enables the material to work effectively as part of a building envelope. The substructure in commercial wall systems is typically composed of a layer of 18-gauge galvanized steel bar profiles affixed to a thermally broken support clip (for exterior insulated walls meeting the American Society of Heating, Refrigerating and Air-conditioning Engineers [ASHRAE] 90.1, Energy Standard for Buildings Except Low-rise Residential Buildings).
The substructure assembly is engineered to ensure the façade material withstands the expected wind loads/pressures within a prescribed deflection limit (i.e. L/300). This substructure provides significant reinforcement to the material and improves the façade’s overall strength.
Increasing the panel thickness (e.g. 8 to 10 mm [5/16 to 3/8 in.] for phenolic/HPL) may allow for slightly wider distances between the mid-support structures behind the panel. However, the additional costs for a thicker panel to get those slightly wider support distances may not translate into any actual jobsite savings. Most LWRVRS exposed fastener panel façade systems are engineered to work with standardized substructure component lengths and distances (i.e. 600 mm [24 in.] max spacing), and this requires a relatively low panel thickness (i.e. 8 mm [5/16 in.] for phenolic/HPL instead of 10 or 13 mm [3/8 to ½ in.]).