Lightening up on concrete cladding
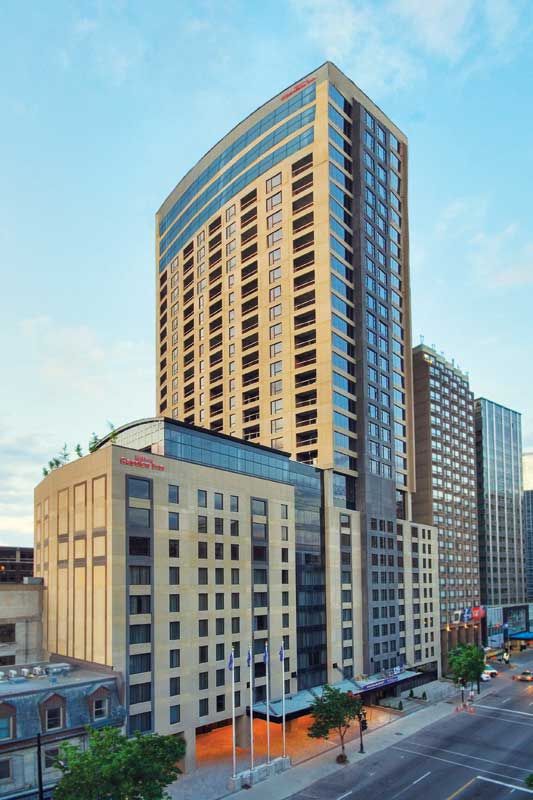
By Moffette Tharpe, Robert Bouchard, CPCI,
and Michael Chusid, RA, FCSI
There was more than half a metre of snow on the ground—the kind of weather when construction crews hate jockeying truckloads of precast concrete panels into position under a crane. However, on the jobsite of Montreal’s Hilton Garden Inn, it was worth the effort because every truckload covered a large expanse of wall. There were more panels per load than a truck usually carries, and some were 9.8 x 3.2 m (32 x 10.5 ft)—a size generally impractical with conventional precast architectural concrete. However, even these surprisingly large panels weighed less than 4600 kg (10,141 lb).
These panels were studcast precast architectural concrete. With 50 mm (2 in.) of concrete thickness, mated to a panelized frame of heavy-gauge galvanized steel studs, such products could enclose a wall two to four times as quickly as conventional precast, sealing out freezing weather and thereby speeding up construction on the building interior by weeks.
In the eternal struggle between building cost and quality, these studcast systems can be potent tools. The thin-panel system provides benefits of architectural precast concrete, but reduces weight by more than 50 per cent. The light weight leads to cost reduction that multiplies through every level of the superstructure, into the foundation. Building with studcast panels saves time, tends to be lighter on the environment than conventional panels, and offers performance advantages.
Weighing the options
Architectural precast is known for esthetic versatility, durability, affordability, speed of erection, and, unfortunately, its great weight. Typical 150-mm (6-in.) thick panels tip scales at about 350 kg/m2 (70 lb/sf), and carry none of their own load. Some precast is even thicker and heavier, hanging on building frames, needing a weighty superstructure for support, which then demands a heavy foundation. The resulting building can also be an environmental burden with respect to materials consumption and greenhouse gas (GHG) emission; about 1 kg (2.2 lb) of portland cement production will emit approximately 1 kg of carbon dioxide (CO2) into the atmosphere.
During the past two decades, several proprietary systems have been developed with the goal of preserving the great virtues of architectural precast, but losing the weight. These different systems are composed of a thin slab of concrete, each with a different integrally cast connection to panelized steel stud framing.
Such studcast panels, made of the same concrete type as a conventional precast panel, can cut the cladding’s weight by about 60 per cent. For the Hilton Garden Inn, this difference alone saved about 1.7 million kg (3.8 million lb), plus further consequent weight reductions in the superstructure and substructure.
The significant thinness is made possible by re-envisioning the interaction between concrete and steel. Conventional precast concrete must be heavily reinforced so the panels can span from floor to floor and transfer wind, seismic, and other horizontal loads into the building structure. The steel reinforcing bars, at the panel’s centre, are not efficiently located to provide tensile forces required to hold together a panel. Consequently, conventional architectural precast panels are usually 152 to 203 mm (6 to 8 in.) or more thick.
In a studcast panel, by contrast, the steel studs are efficiently deployed to resist horizontal loads. If studs can be considered the ‘bones’ of the panel, the relatively thin precast surfaces are the weather-resistant ‘skin.’ The precast requires only a modest amount of reinforcing (typically, welded wire mats) to strengthen short spans between steel studs. The two materials work together for an efficient wall.
Studcast panels are typically made with 50-mm (2-in.) minimum concrete thickness. The concrete can be full-density ‘hard rock’ with compressive strength in the range of 35 MPa min (5000 psi). (‘Hard rock’ refers to the kind of concrete normally used in buildings and sidewalks. It is made with crushed rock and sand for coarse and fine aggregate.) It can be cast utilizing any possible options with conventional precast panels (e.g. multiple integral pigments, exposed aggregate, form liners for cast-in textures such as brick or stone, returns, and reveals).
The panelized steel stud framing is integrally cast with concrete, making it possible to achieve composite action. The panelized frame is easy to properly position for casting, allowing the process to become fast and efficient. This integral framing also eliminates need for applying additional furring to the panel’s interior; as cast, it is ready to receive interior finishes. Moreover, the frame provides built-in cavities for utilities and insulation. By eliminating the need for additional furring, 50 to 100 mm (2 to 4 in.) of floor space is gained around the entire building perimeter. At least one system mounts out-board of the floor edge, providing even more floor space. (Depending on the project’s size, this extra space could be worth a ‘free’ office or more.)
There are several proprietary types of studcast panels. The main distinguishing factor between them is the method of achieving connections between concrete and steel. In some systems, specially designed connectors are attached to the steel frame and embedded in concrete during casting. Another method involves embedding part of the steel frame itself in the concrete.
The choice of attachment technique can impact several aspects of panel performance. Thermal isolation of the steel frame from concrete affects the panel’s insulating ability. The smaller the surface area of steel/concrete contact, the better thermal isolation. Use of a connector creating a small air gap between the framing and interior concrete surface is ideal, eliminating ‘hot spots’ and ‘cold spots’ that would telegraph stud positions on the concrete’s exterior surface.
A connector with slight flexure and a thermal coating gives the concrete skin a small degree of movement freedom relative to the framing. Flexure of the connector isolates the building’s concrete skin from movement of the frame, allowing the panel to respond better to thermal expansion and contraction, wind loads, and seismic movements. It minimizes tensile stress in the concrete at connection points—reducing the possibility of cracking—and helps maintain integrity of seals in panel joints.
Perhaps the greatest advantage is reduced dead load. It results in a lighter superstructure, which in turn allows a smaller investment in foundation and footings. This saves cost in terms of reduced material consumption, excavation, and construction time. In locations where seismic activity is a design concern, the lower mass of thin panels reduces the level of bracing required.
Lighter panels make possible certain designs that would be impractical with conventional precast concrete. For example, the Marriott ExecuStay in New York City was built next to a low-rise building, and ‘air rights’ over the low-rise were secured. Cantilevered floor slabs were designed over the top of the lower building without column supports for the floor slabs, creating extra leasable floor space. This design required lightweight cladding, so the architect specified a studcast panel system.
Less weight per square metre of wall area makes it practical to cast larger panel sizes. Numerous benefits flow from this ability:
• more wall surface area can be carried on a single truck, speeding up delivery and minimizing associated transportation-related costs and energy consumption;
• larger panels mean fewer ones, so more expanse of wall gets enclosed with each panel erected;
• fewer panels minimizes the number of joints that must be sealed, and reduces locations for air or water infiltration in the event of sealant failure;
• larger panels give architects more freedom to design joint spacing in a logical and esthetically attractive manner; and
• faster enclosure of the building allows other trades to begin work sooner on the interior, minimizing potential weather delays.
Alternatively, if larger panel sizes are impractical due to building design, the lightweight system means regular-sized panels weigh less. Lightweight panels can be erected with a lighter-duty crane, which can create significant savings or simplify construction operations.