Leveraging energy efficiency to finance HVAC system retrofits
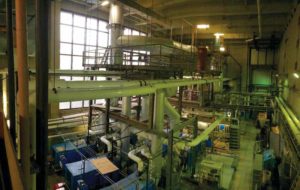
Project planning
To achieve its goals, CHU issued a public request for proposal (RFP), seeking a design-build firm with the ability to contractually guarantee the project cost, financial incentives, and annual savings over the entire payback period. One of the financial metrics used to choose the winning firm was net present value (NPV). This model highlighted the project with the greatest overall value for CHU, accounting for all related expenses and savings over a 20-year period.
In this RFP, CHU made outcomes such as critical asset renewal mandatory. Beyond this, the proponents were free to come up with the best answer to CHU’s needs. It was more about defining the ‘what’ (i.e. goals) than the ‘how’ (i.e. specifying the preferred solutions).
Over the following months, Ecosystem, the chosen firm, virtually became an extension of CHU’s technical services department, doing extensive surveys of HVAC systems and prompting feedback from CHU’s operating staff. The project team focused on achieving substantial results and took a holistic approach to retrofitting the buildings, seeking every opportunity to improve the heating and cooling networks, lighting, and ventilation and centralized control systems.
A central aspect to the design was converting the hospitals’ steam heating systems to hot water, making it possible to add high-efficiency heat pumps. These, in turn, can also provide some cooling and extra flexibility during shoulder seasons. The design for each site focused on maximizing heat recovery and minimizing energy losses throughout all networks (steam and hot and chilled water). Site designs also considered all possible incentive programs available and tried to maximize them.
Once the design for the deep energy retrofit was finalized, the project team provided a detailed description of the energy conservation measures and the contractually guaranteed financial figures. This allowed CHU to secure financing and get started with the implementation phase.
Throughout the entire construction period, the design-build firm supported CHU’s staff to ensure efficient operation without compromising the comfort and security of patients and staff.
LESSONS LEARNED |
There are many ways to tackle large projects, and each approach has its pros and cons. For projects specifically targeting energy-consuming HVAC systems, Québec City University Hospital Centre (CHU) de Québec – Université Laval felt paying a firm to achieve results, rather than simply deliver a project, would compel all the parties involved to a more collaborative approach and thereby provide better integrated solutions.
Identify a project champion within the organization Despite the pros of the integrated performance contracting approach largely outweighing the cons, the relative complexity of the process requires a full commitment from the organization. This commitment lasts for many years through the design, construction, and performance follow-up periods. Having an internal resource dedicated to the project ensures it moves ahead seamlessly and that all stakeholders work with the best available information to meet the desired outcomes. Specify needs clearly Attracting design-build firms willing to contractually guarantee the project cost, financial incentives, and annual savings necessitates a very specific type of request for proposal (RFP), requiring more time to build a proper reference year, among other considerations. Get the most value out of the RFP To help get the most from a performance contracting project, prior to RFP, it is advisable to have a thorough knowledge of the building, including existing capital plan requirements such as aging HVAC equipment replacement. This way, one can include a few mandatory requirements within the scope of the project and plan to inject money into the project to finance some of the improvements that do not generate energy savings. The extra effort spent prior to issuing the RFP will pay dividends in the future. The procurement process should also allow proponents the freedom to come up with innovative solutions, as long as existing environmental conditions remain equally as good or better. Using the net present value (NPV) calculation over 20 years is helpful to compare various projects with different return on investment (ROI) periods. It is important to ensure proponents enter the useful life of industry-recognized equipment in their NPV calculation, along with the appropriate annual maintenance cost that can at times negate any maintenance cost gains from removing older equipment. Future building operations With projects based on the unification of many networks, one must consider isolation devices (e.g. valves and heat exchangers) and strategies to isolate portions of the network in case of maintenance issues. Transparency During the performance follow-up period, a well-documented measurement and verification (M&V) plan is critical to preventing unnecessary negotiations between parties. A thorough knowledge of the building will equip one to set the best M&V strategies for various energy conservation measures. Investing in operating staff Major infrastructure upgrades bring on new operating strategies. The staff should get a comprehensive training program. |