LEEDing opportunities for glass and glazing
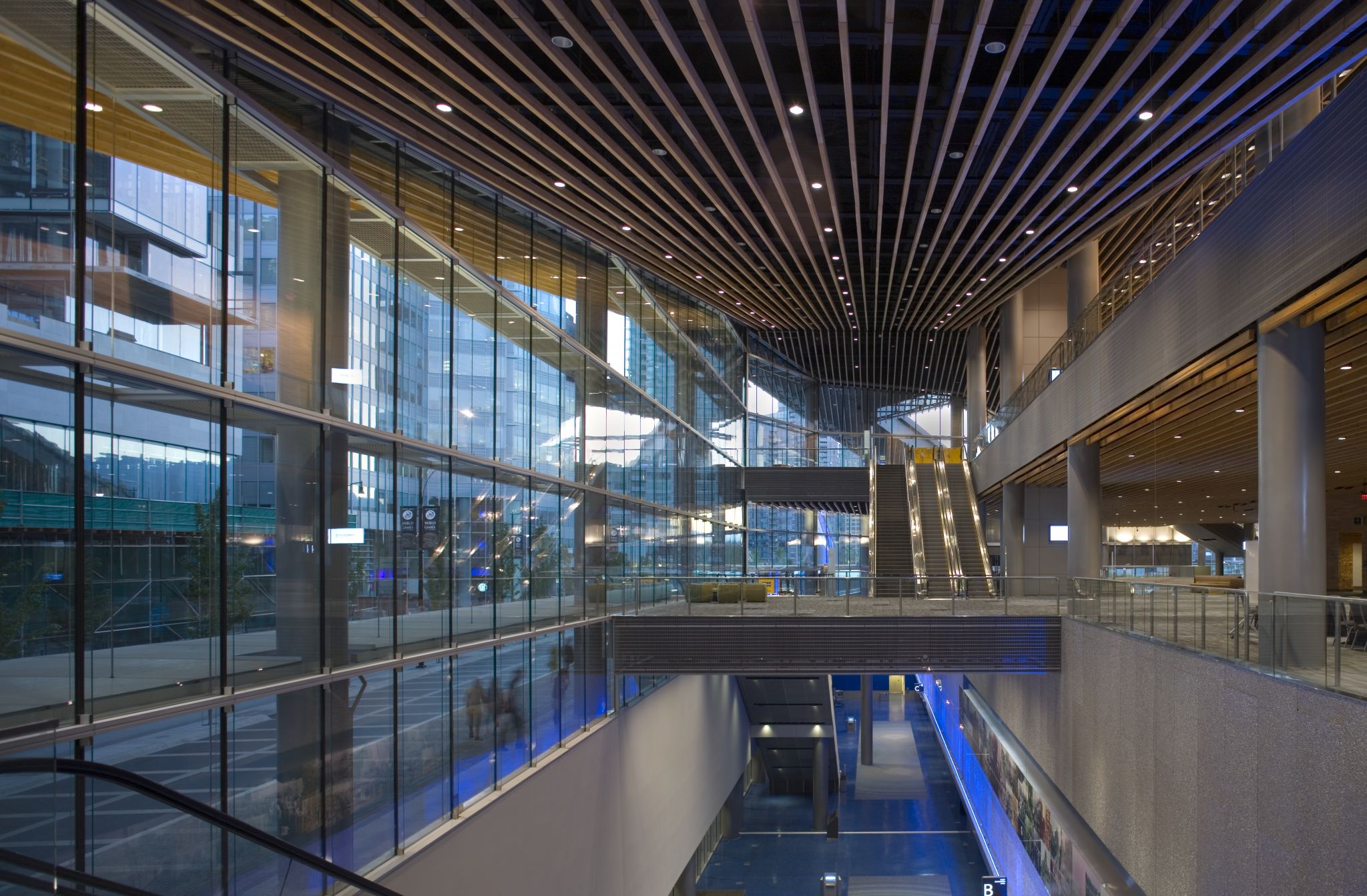
By Valerie L. Block, CDT, LEED AP
Sustainability is a guiding principle for architects around the world. Designs are aimed at conserving our natural resources and improving the quality of life for people inside homes, schools, and office buildings. The specification of glass and glazing assemblies is typically based on the availability of high-performance systems with thermal and solar benefits, as well as the material’s ability to allow natural light into a space.
Canada Green Building Council (CaGBC) plays a vital role in the growth of energy-efficient buildings. The organization’s “Green Up” program is aimed at improving the energy and environmental performance of the Canadian built environment. The program enables building owners and real-estate managers to measure energy and water use, compare results to other buildings, set building performance targets, and track savings.
CaGBC’s Leadership in Energy and Environmental Design (LEED) rating system is the most well-known of several different rating systems. First developed for new construction and major renovations, it covers buildings regulated by Part 3 of the National Building Code of Canada (NBC), which include retail, mid- and high-rise residential projects, public assembly facilities, and manufacturing plants. Based on the U.S. Green Building Council’s (USGBC’s) LEED system, the Canadian rating program is specifically tailored for the country’s climates, construction practices, and regulations.
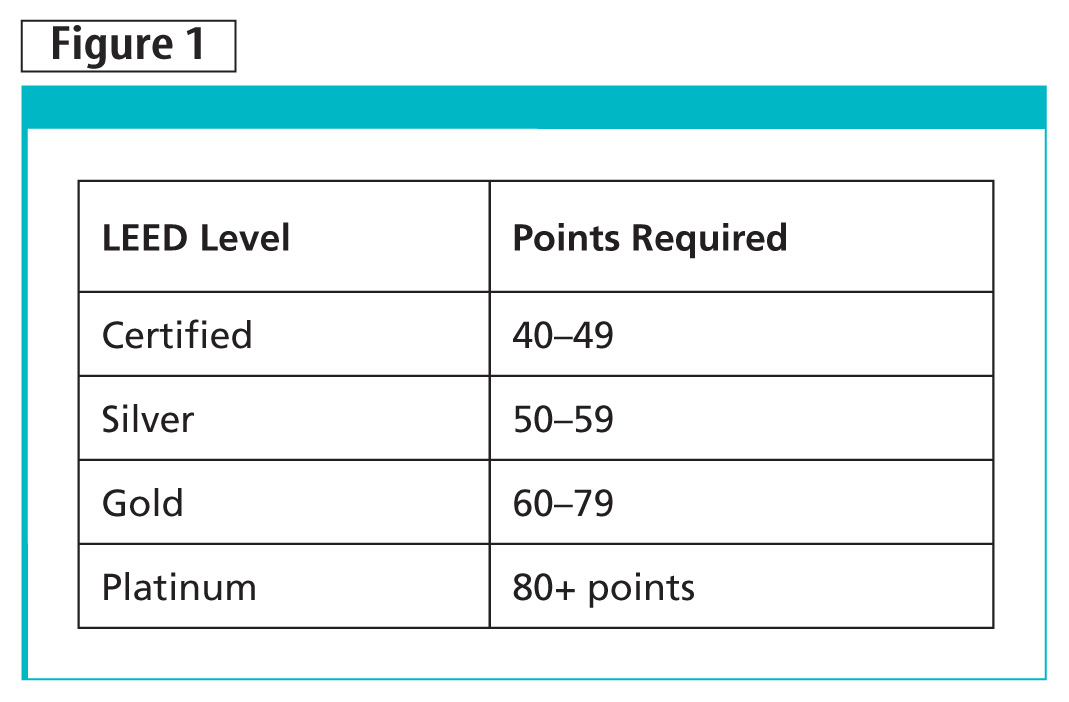
Glass and glazing point opportunities
LEED certification is the prize at the end of the building process. To attain certification, projects registered under the New Construction and Major Renovations program must obtain points based on the scale in Figure 1. The LEED categories where points are awarded are:
- Sustainable Sites (SS);
- Water Efficiency (WE);
- Energy & Atmosphere (EA);
- Materials & Resources (MR);
- Indoor Environmental Quality (EQ); and
- Innovation in Design (ID).
Energy & Atmosphere
The biggest opportunity for the glass industry falls in the EA category. EA Prerequisite 2, Minimum Energy Performance, establishes the minimum level of energy efficiency for the project. There are three options for compliance: a whole building simulation, a prescriptive compliance path, or following the New Building’s Institute’s (NBI’s) Advanced Buildings Core Performance Guide.
If the first is selected, there are two outcomes. This option requires a 23 per cent cost improvement in the proposed building performance rating over the Model National Energy Code for Buildings (MNECB) for new buildings, or a 19 per cent cost improvement in the proposed performance rating for major renovations to existing buildings, as compared with the reference building performance rating.
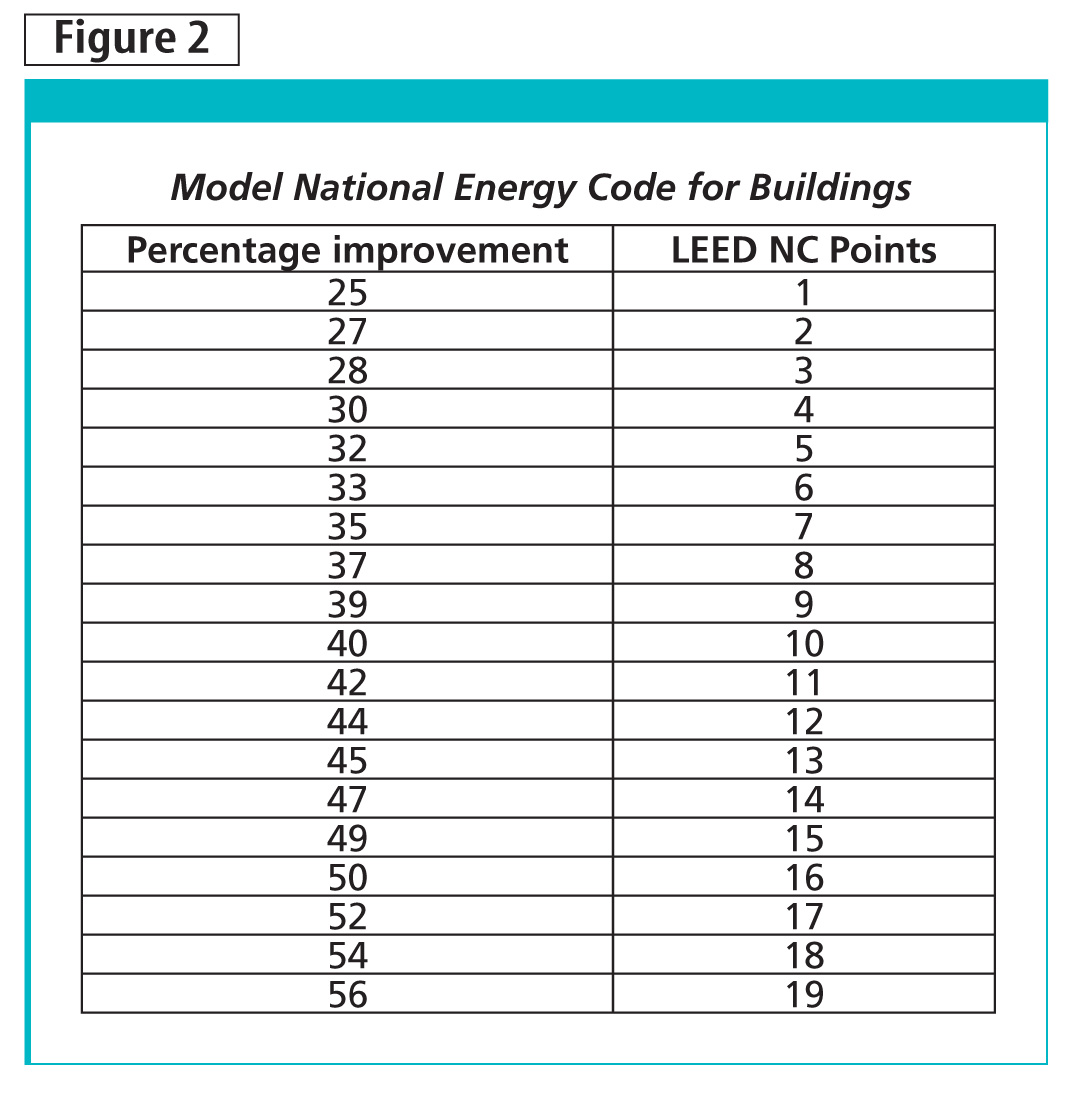
Unlike other parts of the building envelope that use R-value to describe insulation, glazing’s insulation value is referred to as U-factor, or U value. For example, high-performance double-glazed windows can have U-factors of 0.30 or lower. Triple-glazed insulating glass units (IGUs) can achieve U-factors as low as 0.15. (The lower the value, the better the overall performance of the glazing in reducing heat loss.) The fraction of solar radiation admitted through a the material is described as the solar heat gain coefficient (SHGC). The lower the SHGC, the less heat is transmitted. High-performance low-emissivity coatings on glass can improve its performance in both heating and cooling dominated climates.
The second option requires American Society of Heating, Refrigerating, and Air-conditioning Engineers (ASHRAE) 90.1-2007, Energy Standard for Buildings Except Low-rise Residential Buildings, demonstrates a 10 per cent cost improvement in the proposed building performance rating for new buildings, or five per cent cost in the proposed building performance rating for major renovations to existing buildings, compared with the baseline building performance rating.
This option is the prescriptive compliance path. There are four routes that can be used to demonstrate compliance as determined by ASHRAE:
- 2004 Advanced Energy Design Guide for Small Office Buildings;
- 2006 Advanced Energy Design Guide for Small Retail Buildings;
- 2008 Advanced Energy Design Guide for Small Warehouses and Self-storage Buildings; and
- 2008 Advanced Energy Design Guide for K-12 School Buildings.
The final option is to demonstrate compliance by following NBI’s Advanced Buildings Core Performance Guide, which consists of 30 criteria related to the building envelope, lighting, HVAC, and power systems and control. A 30 percent energy savings is expected over model energy standards.
EA Credit 1, Optimize Energy Performance, enables the award of one to 19 points based on a whole building simulation run in accordance to MNECB or ASHRAE 90.1-2007. As glass is a cost-effective, popular material for the building envelope, high-performance coatings and glazing systems designed to conserve energy can take advantage of the points available in this category.
EA Credit 2, Onsite Renewable Energy, awards one to seven points for onsite renewable energy savings—an opportunity for systems that incorporate solar cells. Today, building-integrated photovoltaic (BIPV) glass is found in skylights, façades, spandrels, curtain walls, and atrium roofing where transparency is not required.
Future BIPV glass may offer transparency as well as solar power. The two methods for calculating energy savings from renewable energy are the building annual energy cost calculated in EA Credit 1 or the U.S. Department of Energy’s (DOE’s) Commercial Buildings Energy Consumption Survey (CBECS) database to determine the estimated electricity use.
Materials & Resources
MR Credit 4, Recycled Content, awards one or two points for materials using recycled content. The sum of post-consumer recycled content plus half of the pre-consumer content must constitute at least 10 or 20 per cent (based on cost) of the total value of the materials in the project. The recycled content value of a material assembly is determined by its weight. The recycled fraction of the assembly is then multiplied by the cost of assembly to determine the recycled content value. For example, window manufacturers typically identify the percentage of pre-consumer and post-consumer content used to build a finish product that may include glass, aluminum, fibreglass, or wood.
MR Credit 5, Regional Materials, awards one or two points for building materials or products that have been extracted, harvested, recovered, and processed within 800 km (500 mi)—2400 km (1491 mi) if shipped by rail or water—of the final manufacturing site. Depending on location, window manufacturers may be able to help a project earn these points.
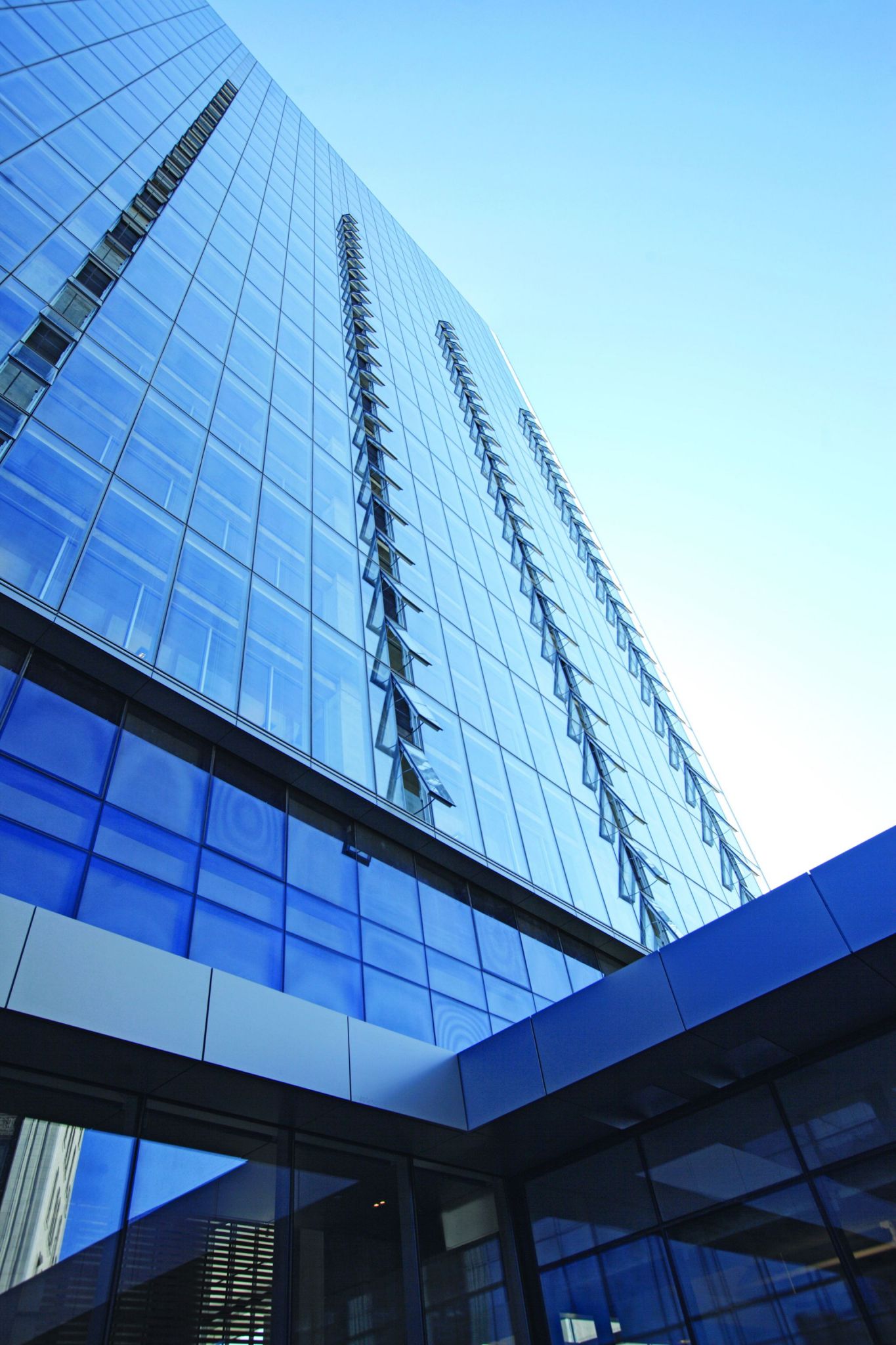
MR Credit 6, Certified Wood, offers one credit for wood-based materials and products certified in accordance with the Forest Stewardship Council’s (FSC’s) Principles and Criteria, for wood building components. (Many window manufacturers confirm the wood used is FSC certified and include this information in their literature.)
Indoor Environmental Quality
EQ Credit 4.1, Low-emitting Materials–Adhesives and Sealants, allows one point to be awarded for use of adhesives and sealants on the interior of the building in compliance with volatile organic compounds (VOC) limits. For instance, structural glazing adhesives cannot exceed more than 100 grams per litre, less water, of a VOC. Information on the VOC contents of sealants should be available from the sealant supplier.
To earn a point in the EQ Credit 6.2, Controllability of Systems: Thermal Comfort, in regard to glazing assemblies, operable windows may be used in lieu of controls for occupants located 6 m (20 ft) inside and 3 m (10 ft) to either side of the operable part of the window. This category awards one point if individual comfort controls are provided for a minimum of 50 per cent of the building occupants, which enables adjustments to meet individual needs and preferences.
EQ Credit 8.1, Daylight and Views–Daylight, enables one point if daylighting is provided into at least 75 per cent of the regularly occupied spaces. Skylights are effective design features to enable greater use of natural light instead of electric lighting. In some cases, glass walkways have opened up spaces to allow natural light to reach lower floors on a space.
EQ Credit 8.2, Daylight and Views, awards one point if a direct line of sight to the outdoor environment via vision glazing between 760 and 2300 mm (30 and 90 in.) above the finished floor for building occupants in 90 per cent of all regularly occupied areas is present.. Glass façades, storefronts, and windows enable the visual connection between the inside of the building space and the outdoors.
Commercial products offering
On the systems side, manufacturers offer a wide array of products. These include:
- sloped glazing and skylight systems that incorporate high-performance materials and enhance daylighting;
- sun shades that help reduce solar heat gain;
- high-performance thermal products, including triple insulating glass (IG) units, high-performance frames, and spacers;
- power shades with photovoltaic cells that convert light energy from the sun into electricity;
- power walls that produce energy by virtue of solar cells in the curtain wall itself;
- operable windows that enable fresh air to enter the building; and
- light shelves that reflect natural light deeper into occupied spaces.
From a glass perspective, laminates and IG units can be specified with high-performance coatings on glass to reduce U-values and solar heat gain into the building. The placement of glass products based on orientation can affect a building envelope’s overall efficiency. Even placing glazing with high visible transmittance (VT) on the top part of a window, and lower VT glazing or shades on the bottom portion, can optimize energy performance and create a more comfortable living and working environment.
Advanced glazing products include:
- electrochromic: an electrical stimulus changes the visible light transmission and solar heat gain co-efficient of the glazing;1
- photochromic: glazing transparency changes with UV light exposure;
- polymer-dispersed liquid crystal: organic particles suspended between two sheets of plastic can go from clear to opaque in appearance;
- sunlight-activated: visible light transmission and solar heat gain co-efficient change based on sunlight exposure;
- suspended particle device (SPD): suspended particles between two electrically coated plastic interlayers; and
- thermotropic: reflective, absorptive, and light-scattering glazing change as temperature changes.
Safety and security
While glass and glazing certainly play an important role in LEED projects, the specification of glass is often based on performance or building code requirements for safety and security. If this is the case, laminated glass may be required to provide intrusion-, blast- or bullet-resistance, or protection from falling glass in skylights and glass railings. Laminated glass can be incorporated into IG units for improved thermal performance. Many coatings can be used with laminated glass to enhance energy performance of the laminate.2
Laminated glass is the only architectural glass solution when post-glass breakage retention is required. Different interlayers used in laminated glass provide various benefits. Softer interlayers (e.g. polyvinyl butyral [PVB]) are better sound-absorbers, and stiffer interlayers (e.g. ionoplast) have improved edge durability, deflection, and post-glass breakage performance over standard PVB interlayers. Whenever laminated glass is used, it is important to verify compatibility of coatings, frits, and sealants with the interlayer.
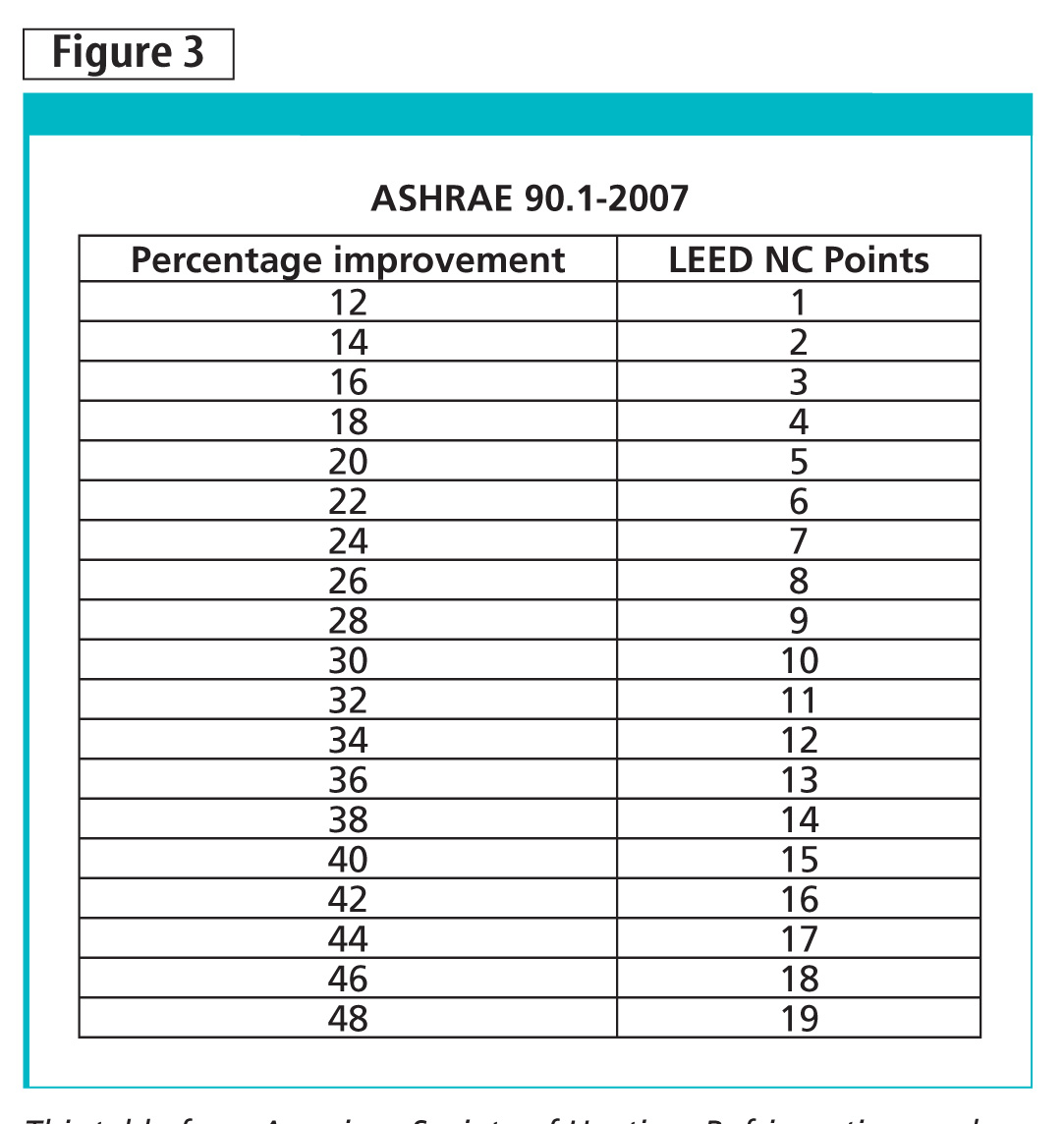
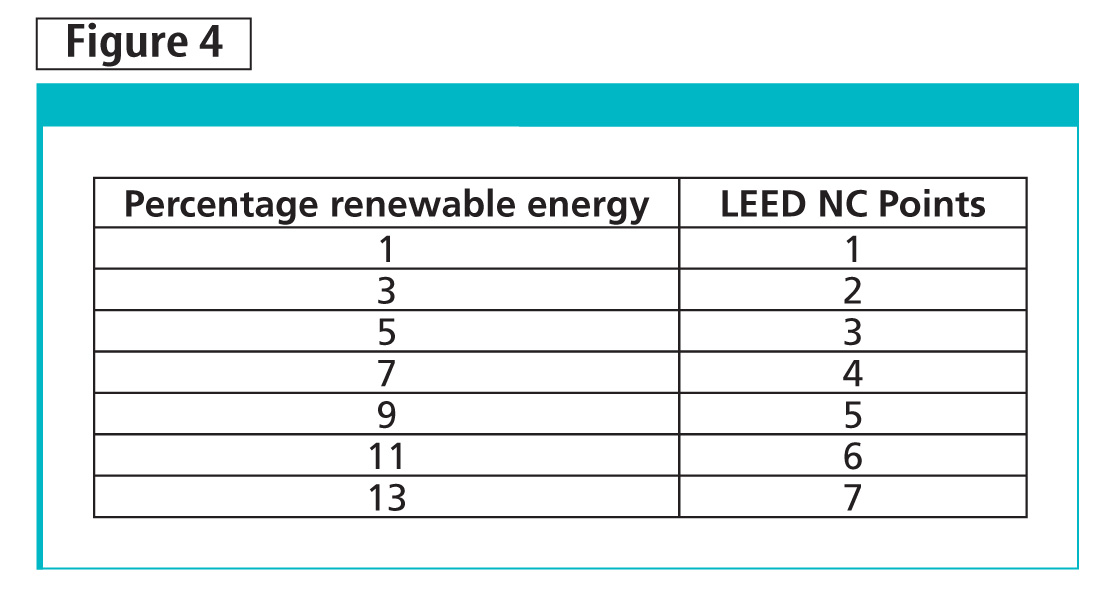
Conclusion
After all is said and done, architects and building owners still appreciate the esthetic glazing offers. Glass is an attractive, cost-effective building material that also connects well to sustainable building strategies. Its ability to connect the inside and outside environments is recognized by LEED, as it can not only deliver effective energy performance, but it can also bring light into a space to help conserve energy usage.
Notes
1 For more, see Helen Sanders, PhD, and Maure Creager’s article, “A Dynamic View: Electrochromic glass technology in building envelope applications” in the November 2007 issue of Construction Canada. (back to top)
2 For more, see Valerie L. Block’s article, “Expanding Laminated Glass Performance” in the September 2012 issue of Construction Canada. (back to top)
Valerie L. Block, CDT, LEED AP, is the senior marketing specialist for DuPont Glass Laminating Solutions. She chairs the ASTM task groups on glass strength and the task group on glass floors, as well as the laminating division of the Glass Association of North America (GANA). With 30 years of experience in the architectural glass industry, Block is the president of the Glazing Industry Code Committee (GICC) and a member of the Canadian Standards Association (CSA) Technical Committee on Building Guards. She can be reached via e-mail at valerie.l.block@usa.dupont.com.
To read a case study about the Vancouver Convention Centre West, click here.
To read a case study about the Ottawa Paramedic Service Headquarters, click here.