LEDing the Way to Savings: New light fixtures help reduce bills and increase quality of life
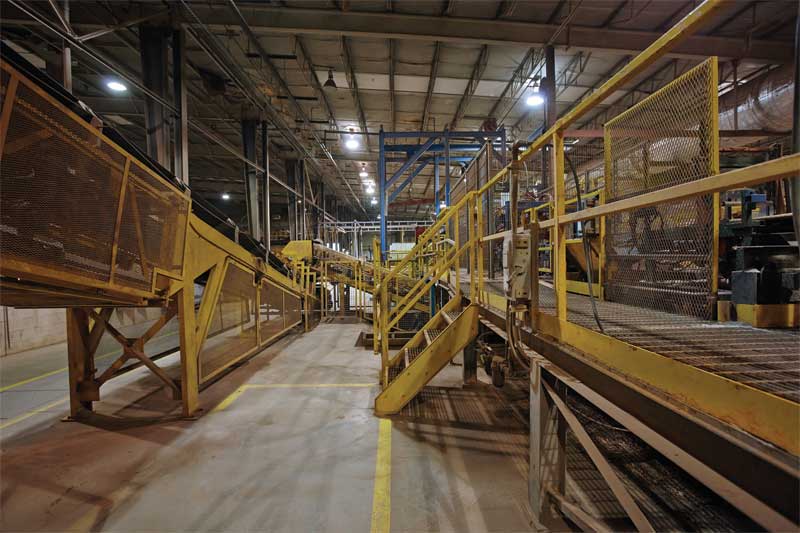
Return on investment
When metal halides are being replaced with LEDs, the return on investment (ROI) is quick. Depending on the building’s size and available rebates, it can take from one to three years, taking into account both energy savings and maintenance costs. When ROI is not as dramatic, facility managers need to examine LEDs’ other benefits and make a ‘quality of life’ decision about their potential impact, and whether it justifies the upfront expense.
Long life
The highest-quality LED fixtures have a rated L70 life (retaining 70 per cent full strength) of 150,000 hours, which is about 17 years of 24/7 use (In contrast, metal halide and fluorescent bulbs typically have a rated life of two to three years.).
Lower maintenance
Some LEDs are built of anodized extruded aluminum with components designed to protect them from dirt and debris, which can lower the lifetime of other lighting sources. There are also no bulbs to change or ballasts to replace, meaning no electricians to hire, lifts to rent, or new bulbs to buy—though drivers do need replacement, it is, on average, every five to seven years.
Bright, clear light
If good visibility makes work easier, then LEDs can boost productivity, quality of work, and employee morale. One large machine shop in Louisville, Ky., decided to replace 160 recently installed fluorescent fixtures with 90 high-bay LEDs. It went from 6 to 12 foot-candles to 28 to 30 foot-candles, and it is much easier to see their work and read blueprints.
Less heat production
A metal-halide fixture can reach 148 C (300 F) or above, while a high-quality LED only hits about 37 C (100 F). Cooler operating light is important not just in cold-storage settings, but also in places that can become uncomfortably warm in summer, such as auto repair shops. Metal halides make spaces hotter—depending on duct placement, they can heat the cooled air from air-conditioning units before it reaches the floor, reducing the efficiency of an HVAC system.
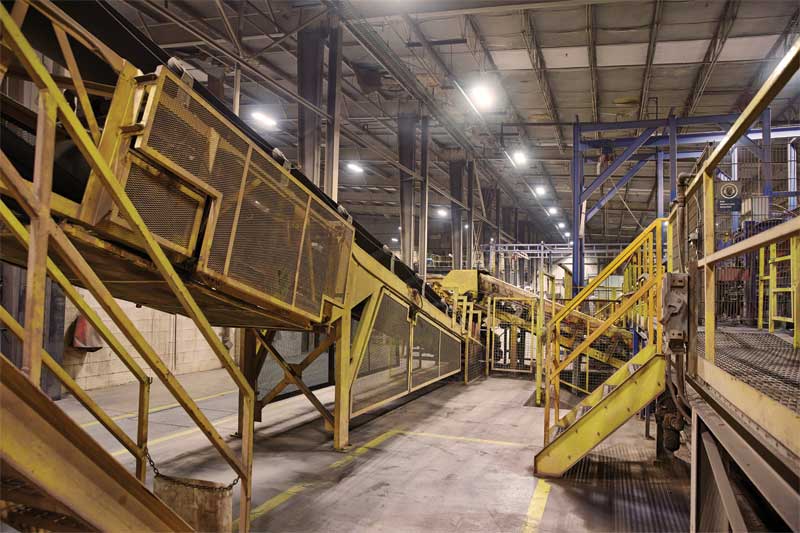
Building in savings
One place where temperature is a factor is brickmaking. A large Canadian brick manufacturer is among the growing number of companies changing metal halides to LED fixtures. The company turns out more than 300 million bricks a year at its 4-ha (10-acre) manufacturing facility in Brampton, Ont., where raw materials are brought in, broken down, moulded into bricks, and put in cars rolling through the kilns 24/7.
Much of the operation is automated, but employees are constantly monitoring the process. It is a dusty environment prone to high temperatures, especially around the kilns. As heat rises, it collects under the arched roof, which was exactly where the facility’s metal-halide fixtures were located. Since many lights were positioned directly above the kilns—having been installed before the current kilns were in place—they were inaccessible for maintenance.
The company decided to reduce expenses by replacing all the old lights with nearly 300 high-bay LEDs that have a high temperature rating and occupancy sensor. Their contractor got layout assistance from the fixtures’ manufacturer, and a series of utility rebates significantly reduced the brickmaker’s cost. The new lighting makes it much easier to detect imperfections in the bricks, and helps employees see where they are walking. The company has seen energy savings of close to $250,000 in the first year since lights were installed, and the feeling is both safety and morale have been improved.
Not all or nothing
Like most facility decisions, choosing whether to install new lighting often comes back to budget. In a large space, such as a brick factory or distribution centre, replacing every fixture can be a big expense. However, upgrading to LEDs does not have to be an all-or-nothing proposition. Installing new fixtures in phases is a good way to get a head-start on facility-wide LED lighting while staying within annual budgets and energy goals. Some lighting manufacturers offer programs eliminating most upfront costs entirely with a monthly service subscription.
LEDs are not yet the best solution for every environment. Places with extremely high temperatures, such as steel mills, still do better with other lighting forms. However, for most other types of facilities, there are LED fixtures ideally suited for the kind of work being done.
With lighting consuming up to 40 per cent of energy costs in some settings, it pays to research various providers to see where they rank in terms of reliability, durability, quality, and performance. With the right assistance and products, retrofitting almost any facility, whether done in stages or at once, can be a smooth process resulting in a brighter and more productive workplace, as well as energy bills that will light up the bookkeeper’s life.
Vicky Broadus has a master’s degree and 15 years of experience as a journalist. She is a writer for Big Ass Solutions, the parent company of Big Ass Fans and Big Ass Light. She can be reached via e-mail by contacting vicky.broadus@bigasssolutions.com.