Knowing the rules of flashing masonry
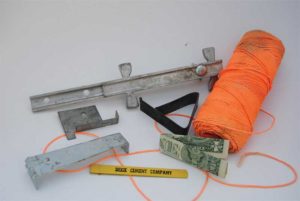
Polyurethanes
For several years, this has been the sealant of choice for many masons to seal masonry-to-masonry, masonry-to-dissimilar material, and metal flashing laps. Polyurethanes are typically one- or two-part sealants offering a wide range of colours for many construction-related joint sealing. It offers a lifespan ranging from six to 10 years, depending on exposure and geographical location. The working temperatures of polyurethanes are limited from 4 C (39 F) to 35 C (95 F). The tack-free time of polyurethane is typically four hours. Single-part polyurethanes are moisture cured and the two-part types are chemically cured. It is important to check the product data when using with flashing to ensure it will have compatibility and adhesion with the membrane selected.
Modified polyether (polyether)
Modified polyethers have become a new force in the sealant industry. Polyethers are modified silicones with the gunnability of silicone and the best characteristics of polyurethanes. In the author’s experience, polyethers do not migrate oils into porous masonry and are gunnable in temperatures as low as –9 C (16 F). With the low volatile organic compounds (VOCs) and the quick tack-free time, polyethers could soon replace polyurethanes because of superior joint material performance, bonding to a wide variety of membranes and substrates, and the ability to be installed in a range of weather conditions. It is important to verify the selected polyether will adhere to the membrane, not just initially, but long-term.
Flashings
Flashings have seen the biggest change in the market over the past few years with the industry introducing products that have proved their value for many years in the roofing industry.
Of course, the tried-and-true copper laminate material is still on the market. A more durable and desirable version with a mesh of polyethylene laminated onto both sides of the copper is now available. It is nearly impossible to cut with a trowel and as good of a material that can be found on the market. In the author’s experience, this flashing material will perform well for years to come.
In terms of cost, rubberized asphalt is usually the most economical, EPDM, PVC, and TPO are typically mid-range in price, and copper laminates are generally the most expensive.
Rubberized asphalt
Rubberized asphalt is the most common flashing on the market today. The rubberized asphalt or ‘stickie back’ is a good stable material that performs well when installed properly. Primers are sold by some manufacturers as part of every application and others omit the primer if the customer used a termination bar. It is critical the masonry contractor reads the fine print for each product as warranties can depend on the use of primers. Compatibility between rubberized asphalt and PVC-moulded corner boots and end dams should be investigated prior to construction as plasticizers can migrate from PVC, and reduce the plasticity of the rubberized asphalt over time, causing the potential for a leak down the road.
PVC
PVC flashings are not the 1980s’ variety, and should not carry any of the reputation of the first-generation PVCs that entered the market. A crossover from the roofing industry, PVCs represent old and new technology with strong, durable, and flexible materials, thanks to the addition of non-migratory plasticizers. The material making the PVC stable and flexible is going to stay within the latter, and not leach out, evaporate, or allow it to break down and become brittle, which would form cracks and create leaks. PVCs are as good of a membrane as any on the market now.