Knowing The Low-flow Culture: New approaches in water- and energy-efficient plumbing
Central domestic hot-water systems in residential apartment buildings usually have multiple gas-fired heater/tank units located in a rooftop penthouse, and are equipped with a recirculation system. The domestic water piping is generally arranged with hot- and cold-water risers running vertically behind the plumbing fixture groups. Thus, there can be relatively short branch-pipe connections to the individual sinks, showers, and lavatories.
However, the balancing of the recirculation connections to the domestic hot-water risers and the arrangement of how these connections are made can be critical for the difference between providing a short wait time and happy residents, and having a bank of suites wasting large amounts of water to get the right temperature at sinks. The due diligence of the installer, balancing agent, and design engineer of record need to come together to ensure the recirculation system is equipped with proper hydronic balancing valves, and that they have been set up to make certain of proper flows at all domestic hot-water risers.
The next step is to resolve the energy efficiency for operating the system. Running even a fractional horsepower recirculation pump can contribute to a small, but significant, fraction of the building energy consumption, along with the standby heat losses from all that hot water circulating around through pipes insulated to ‘code-minimum’ thickness. The State of California is starting to drive most of the leading-edge North American energy codes and standards, and there is movement toward using a demand-control recirculation pump operation.
The traditional method of domestic hot-water circulation pump control is to use a time-of-day schedule; this means having the recirculation pump running during the normally acceptable occupied hours, which could be up to 16 or 18 hours a day. A demand-controlled pump, on the other hand, would be started and stopped based on a number of options:
- water temperature sensor in the system that cycles the recirculation pump to maintain a minimum system temperature at the furthest available fixture;
- room occupancy sensor in the bathroom or kitchen that enables the recirculation pump; or
- bathroom light interlock, so the recirculation pump can be activated when someone is about to use hot water.
Commercial buildings
From retail shopping centres to high-rise office buildings, commercial buildings also have similar issues. However, they are less affected than residential buildings due to the much lower plumbing fixture count. Nevertheless, the same issues arise for retrofitted low-flow fixtures in an older plumbing system, as well as new installations where the domestic hot-water heat maintenance systems are not designed to best-practice standards.
Commercial office buildings can be ideal project types to specify a demand-controlled domestic hot-water recirculation system using occupancy sensors in the washrooms due to the intermittent use throughout the day. The key design issue involves ensuring the domestic hot-water recirculation connection to each lavatory is made within 2.5 m (10 ft) of the faucet.
Retail projects where the washrooms could have high traffic are best served by a time-of-day domestic hot-water recirculation system, or an electric heat-traced temperature maintenance system in new construction applications. The self-regulating heat tracing is reasonably energy efficient provided the pipe insulation is properly installed, ideally with insulation thicker than the code minimum. The most important thing is to make certain the run-outs to the fixtures requiring hot water are designed properly in the first place for new construction.
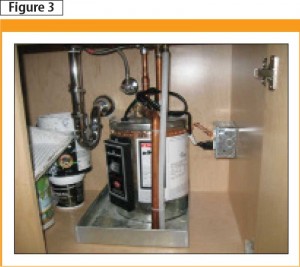
Photo courtesy Cobalt Engineering
A viable option for small local washrooms are point-of-use water heaters, consisting of a local electric heater with a small amount of storage capacity. This can achieve relatively low-energy requirements and quick hot-water flow, but at the expense of lost storage space under the sink and counter (Figure 3).
Conclusion
Properly piped demand-controlled domestic hot-water recirculation pump systems, along with improved and complete pipe insulation application, can provide the following improvements:
- proper water temperature prevents energy waste and also preserves occupant health and safety;
- having more reliable systems means less maintenance and repair costs; and
- improved convenience means less waiting for hot water and, therefore, saving water.
Of course, the only way this becomes mainstream design—for everything from a single-family dwelling to high-rise apartments—is for the building codes to incorporate the minimum requirements for energy and domestic hot-water systems performance parameters. (To be blunt, voluntarily designing a low-loss/energy domestic hot-water system would not significantly impact the country’s energy use and water waste since the general ‘budget-cost’ approach is to design a building to simply meet the minimum code requirements. As energy and water costs get higher, there will be some economic drive to try to reduce waste and provide domestic hot-water energy conservation, but the code-minimum standards must be raised for there to be real change).
Geoff McDonell, P.Eng., LEED AP, is an associate partner at Cobalt Engineering LLP in Vancouver. He has more than 30 years of experience in mechanical engineering, and is a registered mechanical engineer in British Columbia and Alberta. McDonell specializes in low-energy mechanical systems, including radiant cooling applications, Passivhaus style designs, and assisting architects with building envelope performance evaluations. A Leadership in Energy and Environmental Design-accredited professional (LEED AP) since 2001, he was a speaker at the first Greenbuild conference. He can be contacted via e-mail at gmcdonell@cobaltengineering.com.