Jet-grouting: A soil improvement technology
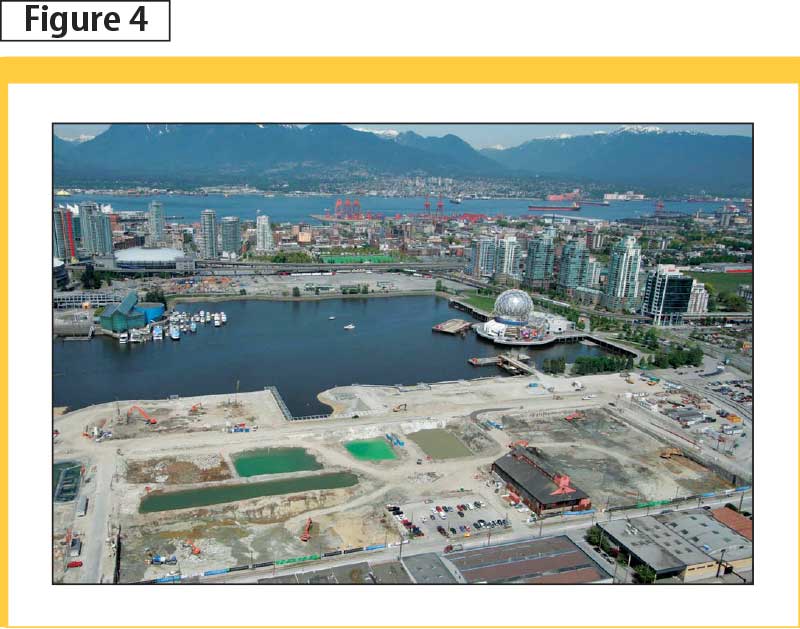
Jet-grouting was used on this project for shoring of the single large excavation of the whole site. More than 1100 jet-grouted columns were installed along three sides of the site perimeter, some in close proximity to the ocean. Jet-grouting was selected to create a soil-cement wall with two primary objectives:
- to create an impervious cutoff wall protecting the site from water seepage; and
- as a support of streets and other adjacent public space improvements.
Site conditions
The city had commissioned a design for infrastructure improvements at the site, which included all new roads and utilities north of 1st Avenue. The intent was to complete all these works before building construction on the site began. The city’s geotechnical consultant concluded the existing fills were compressible and could not be used to support future roads and utilities. Therefore, before installation of any improvements, all the existing fills were to be removed from the future road right-of-ways and replaced with compacted engineered fill.
The Olympic Village site was previously used for various industrial activities, including wood-sorting and log-milling facilities and a zinc-plating plant. Much of the current site was originally reclaimed from False Creek by placing up to 6-m (20-ft) thick layers of variable soil materials. Due to the previous industrial use, a significant amount of soil and groundwater contamination was identified and needed to be remediated before the beginning of construction.
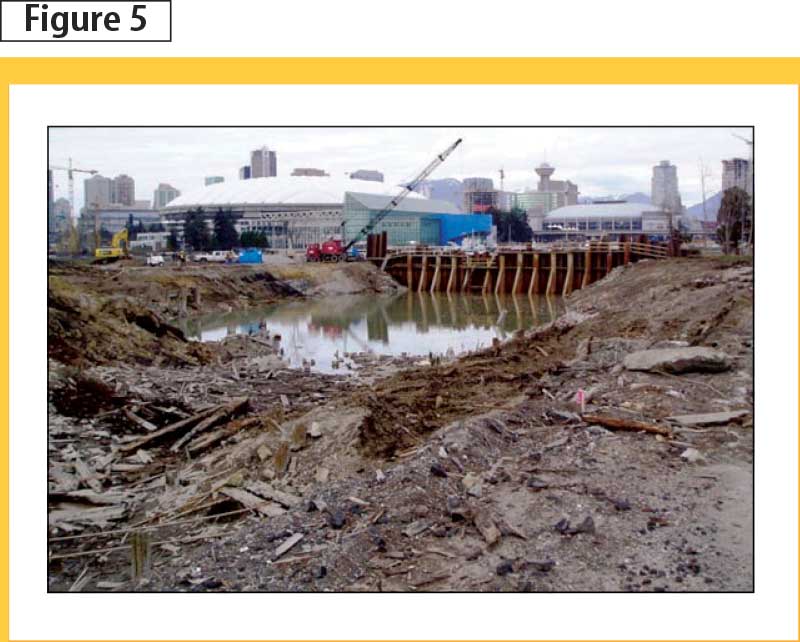
Photo courtesy Cement Association of Canada
The site cleanup employed another soil improvement technology called solidification and stabilization (SS), which uses cement as a primary medium to bind soil contaminants. About 280 tonnes classified as ‘hazardous contaminated soil’ was stabilized using cement. In this application, the SS technology reduces the leachability characteristics of the lead in the soil, and thus renders the treated soil non-hazardous (Figure 5).
The developer negotiated a delay to the installation of improvements on some roads to reduce the amount of shoring required and also lower the potential to which existing works would interfere with construction. Therefore, only the site’s perimeter was shored, and Parcel 4 was shored separately.
The subsurface soil and groundwater conditions were carefully investigated by city staff and the information was made available to all the parties involved in the project. Soil profile at the location of the shoring walls consisted of up to 7 m (23 ft) of compact to dense clean granular fills over native soils consisting of loose to compact post-glacial marine sediments overlying dense glacial till. The glacial till was made up of a well-graded mixture of silt and sand with some gravel and occasional cobbles and boulders, and underlain by sandstone to siltstone bedrock. The fill thickness generally increased from the south side (as little as 1 m [3 ft] thick) toward the north side of the site where up to 7 m of fill was identified. The long-term static groundwater level was located at about 0.5 m (1.6 ft) geodetic, although a perched transient groundwater condition occurred along the south end of the site, where fills were generally thinner.
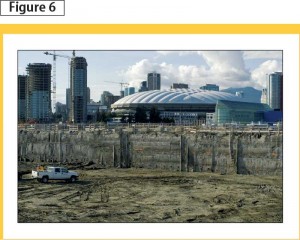
Photo courtesy Sea to Sky Geotech Inc.
Figure 6 shows the completed jet-grouted wall construction. To improve the wall stiffness, vertical steel H-sections were installed in alternate columns every 1.5 m (5 ft) on centre (oc). The knife-trimmed wall provided a smooth surface on which a synthetic drainage material could be applied directly against the shoring. The minimum required column diameter was 900 mm (35.4 in.) with centre to centre spacing of 750 mm (30 in.) to ensure full overlap between the columns and watertightness of the shoring wall.
A traditional sheet pile wall was also initially considered. However, based on the designers’ previous experience, there were concerns with groundwater leakage at the interlock and anchor head. Further, sheet piling could not be relied on to be driven through debris-laden fill and also as a permanent cut-off wall because of close proximity to a marine environment where groundwater was shown to be brackish.
Conclusion
The Olympic Village jet-grouting project confirmed the flexibility and suitability of this construction technology in variable ground conditions where a high-strength and low-permeability structural wall is required. The system was able to be installed in the vicinity of existing utilities and fixtures, with low vibration levels and generally low impacts to the surrounding lands.
Removing the upper portion of the walls required for various parcels servicing was also straightforward once shoring was complete. The work was able to proceed regardless of the discovery of unexpected materials, including wood waste, steel and concrete fragments, and boulders that would have impeded the installation of other shoring systems.
Andy Vizer, P. Eng., LEED AP, is the director of engineering with the Cement Association of Canada (CAC) Western Canada Region. He spent a decade in the consulting field before joining CAC, where Vizer spent 30 years working in various positions. He can be reached via e-mail at avizer@cement.ca.