Jet-grouting: A soil improvement technology
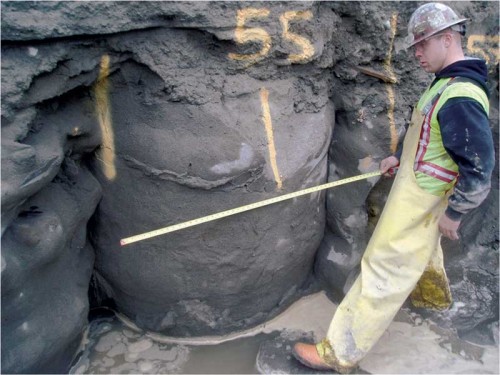
By Andy Vizer, P.Eng., LEED AP
Jet-grouting is a soil improvement technique used in many parts of the world. It involves mixing in-situ soil with water-cement grout, which is then injected into the soil with the aid of special tools at high speeds of over 200 m/s (656 ft/s) and under high pressures ranging from 30 to 60 MPa (4500 to 9000 psi). Jet-grouting was introduced to British Columbia in 2004; since then, several applications for soil improvement––both temporary and permanent––have been successfully carried out in the Lower Mainland.
Historically, the technology was developed in Japan in the mid-70s and imported to Europe in the decade that followed. In Europe, most notably in northern Italy, this technology was quickly adopted and became popular (due to soil conditions particularly suitable to jet-grouting, made up of alluvial soil with sand and gravel). In North America, the use of jet-grouting has also made inroads in recent years. During the last grouting conference in 2003 in New Orleans––a conference held every 10 years––papers presented on the jet-grouting technology were the focus of the event.
Introduction to jet-grouting technology
As mentioned, jet-grouting employs a grout mix injected into the ground under very high speed and pressure. Created at the bottom of the drilling rods, the jet erodes the native soil matrix and simultaneously introduces a water-cement mix into the soil. After the drilling rod is lowered into the required soil depth, the jetting begins. The rod is then withdrawn upward at a constant speed and rotation as shown in Figure 1. The result is a series of grout columns resembling structures.
There are several parameters influencing the characteristic shape and size of a constructed jet-grouted column. Selected by the designer and controlled in the field, these include:
- grout mix pressure;
- air and water pressure (a function of the jetting type employed);
- diameter and number of nozzles (located on the drilling rod);
- grout mix composition; and
- rod withdrawal and rotation speed.
Types of jet-grouting
There are three main types of systems normally used in jet-grouting.
Single fluid
In this method, soil disaggregation and its mixing with the grout mix is done directly by the same grout mix.
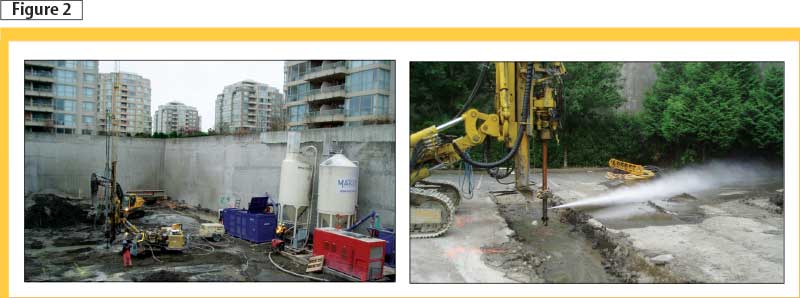
Double fluid
For this system, soil disaggregation and its mixing with the grout mix is done directly by the grout mix in combination with a coaxial air jetting to increase the delivery energy.
Triple fluid
For triple-fluid systems, soil disaggregation is done directly by high-speed water pressure and a coaxial air-jetting. The mixture is created by the grout mix delivered at a lower jet pressure done from a nozzle located below the air/water nozzle. This way, the grout mix is injected into the already eroded soil.
Typical equipment
The execution of a typical jet-grouting operation is usually carried out by medium-sized equipment comprising the following components (as seen in Figure 2):
- a high-pressure grout pump, typically 350 HP;
- a grout plant including a cement silo with a capacity to typically produce 9 to 12 m3 (318 to 424 cf) of grout mix per hour required to continuously feed the pump;
- a drill rig specially equipped for jet-grouting consisting of a mast between 15 to 18 m (49 to 59 ft) high (this mast length usually allows the construction of most jet-grouted columns without the need for rigging up additional rods);
- compressor (when double or triple jet grouting is used); and
- accessories such as a high-pressure grout hose, special swivel, nozzles, computer station, and special single-, double-, or triple-rods.
Quality control
State-of-the-art jet-grouting requires installation of sophisticated sensors located at the pump and drill rig hooked up to a computer station. These sensors are required to keep all the parameters described above under control during the drilling and jetting operations.
Sensors are installed to evaluate the drilling rod depth, grout pressure and flow, and withdraw speed and rotation in real-time. A computer on the drill rig is able to record and store all these parameters to allow for control of each phase during drilling and jetting. The collected data is then stored in the computer and available either electronically or in hard copy.
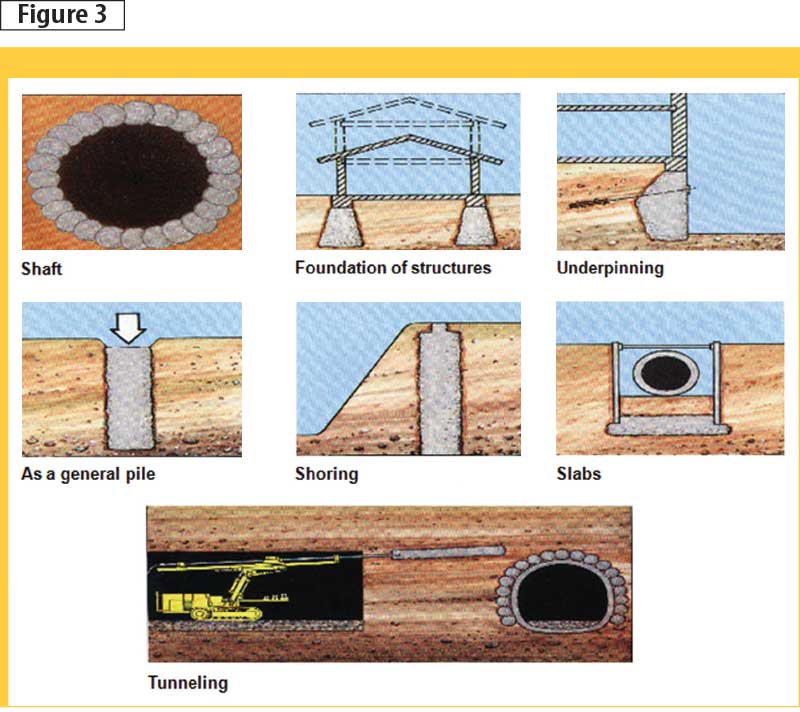
Applications of jet-grouting technology
Some key advantages of jet-grouting technology are the easy and safe installation processes without unwanted disruption to other operations. This often results in reduced construction time when compared to alternate and competing systems. When used as a soil improvement technique for building foundations, jet-grouting eliminates ground vibration often associated with other soil improvement technologies. This benefit is of particular importance in dense urban environments where unwanted vibration during construction may damage the surrounding facilities.
Several case histories of jet-grouting are available in construction literature. These uses range from a simple groundwater cut-off wall to more complex applications, such as structural underpinning. A typical list of jet-grouting applications, illustrated in Figure 3, includes:
- cut-off wall;
- shoring (temporary and permanent);
- vertical shaft;
- various foundation structures (footings and slabs);
- single pile with or without steel reinforcement (casing or bars);
- underpinning of existing structures; and
- tunnel liners.
Vancouver Olympic Village
Vancouver’s largest application of jet-grouting so far was used as a permanent shoring structure at the recently completed residential Millennium Water development in False Creek. The facility hosted athletes for the Vancouver 2010 Olympic Winter Games, and was subsequently converted into housing and is currently being sold to the marketplace. The site comprises 10 parcels of land, covering an area of 46,000 m2 (495,140 sf) in close proximity to False Creek waterfront (Figure 4). The development contains about 15 residential and commercial buildings.