Is ‘buying local’ always better?
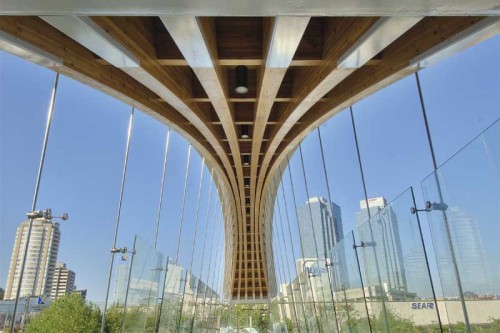
By Helen Goodland, BA, Dip. Arch, RIBA, MBA, LEED AP
Placing special emphasis on the use of local materials is a popular approach to reducing the many environmental impacts of construction projects. The Canada Green Building Council’s (CaGBC’s) Leadership in Energy and Environmental Design (LEED) rating program offers points under Materials and Resources (MR) Credit 5, Regional Materials, for sourcing building materials from within 800 km (500 mi) of the site. However, the reality is more complex and one should not assume the pursuit of this credit will actually reduce the project’s environmental impact.
The primary effects of transportation are the fossil fuels used in conveyance and the associated greenhouse gas (GHG) emissions. It is simplistic to consider these impacts independently from what is being transported and why.
The first factor to consider is the material’s weight and how much is needed. Concrete is extremely heavy and a great deal is required for constructing a wall or floor compared to a framed wall made out of wood or steel studs. As a result, one gets more building out of 1 tonne of steel or wood than 1 tonne of concrete.
Secondly, while it may seem somewhat counterintuitive, transportation impacts are not necessarily a function of distance; mode of transportation matters a lot. A product travelling a long distance via a highly efficient mode may have a smaller environmental footprint than a product with fewer kilometres to travel in an inefficient carrier. LEED sets out transportation efficiencies as follows: shipping by truck (2127 KJ/tonne-km [735.8 Btu/ton-mi]) is over six times worse than rail (373 KJ/tonne-km [129.1 Btu/ton-mi]) and more than 15 times worse than ship (about 138 KJ/tonne-km [47.6 Btu/ton-mi]). Therefore, shipping 1 tonne of wood from Vancouver to Seoul, South Korea, (8153 km [5066 mi]) by freighter uses roughly half the energy as driving 1 tonne of steel from Vancouver to Calgary (973 km [605 mi]) in a truck.
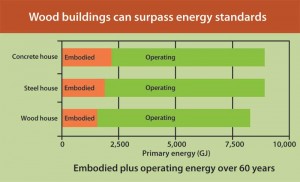
A report by Forintek Division of FP Innovations (a group that includes members of the forest operations, wood products, and pulp and paper industries), “Wood Miles: A Canadian Situational Analysis (Japan) Discussion Paper,” on Japan’s Woodmiles’ system corroborates the same principle, maintaining that “1 km [0.6 mi] of truck travel is equivalent to 31.9 km [19.8 mi] of ocean travel on a bulk carrier.” (A complete copy of the report is available from the “Industry Resources” section of the Forestry Innovation Investment website (www.bcfii.ca). Access to the information is limited to the B.C. forest sector; a password is required to obtain the full report). The report is concerned with the transport of lumber from Canada to Japan. It states that instead of doubling Japan’s self-sufficiency in logs, a faster way to attain the same carbon dioxide (CO2) reduction would be to shift some of Japan’s imports from Canadian logs to Canadian sawn lumber, which is less dense and lighter to transport.
Preference for shipping by road is particular to North America where gasoline prices are lower than competing transportation options. However, this may change. As pricing of carbon emissions takes hold, other modes may become more attractive.
In British Columbia, a carbon tax is already in place, adding $0.0468 to a litre of gas. This increased to $25/tonne in July of this year, moving the tax up to $0.0585/L. Shipping by other less carbon-intensive modes (e.g. rail or ship) will become increasingly competitive as the impacts associated with energy production are monetized and factored in to costs.
Most importantly, the interplay of all the environmental impacts of materials must be considered in totality and objectively assessed. Unlike in Europe, there are no regulations in Canada requiring accountability from product manufacturers for the environmental impacts of raw-material extraction, production, and transportation. The magnitude of these impacts can be significant and building materials are particularly problematic. Large quantities of energy are required for the manufacture of most common construction materials, such as:
- glass–37,550 MJ/m3 (1257.11 MBtu/cf);
- steel–251,200 MJ/m3 (8409.75 MBtu/cf); and
- aluminum–515,700 MJ/m3 (17,264.76 MBtu/cf).
High embodied energy also results in significant carbon emissions. For example, according to the Ecosmart Foundation, one tonne of carbon is emitted for every tonne of cement produced. (Visit www.ecosmartconcrete.com/enviro_cement). By comparison, the Edinburgh Centre for Carbon Management states that trees absorb carbon during their lives, resulting in many wood products being effectively carbon-neutral. (For more information, visit www.woodforgood.com/the_facts). Therefore, the significant carbon footprint of locally available concrete (which would contribute to LEED’s MR Credit 5 points) may net out worse than low-carbon wood from further away (which may not).
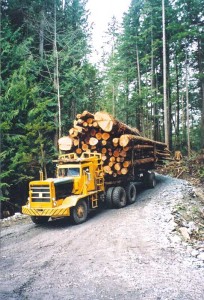
The United Kingdom is the first country in the world to have a Publicly Available Specification—PAS 2050—for assessing the carbon footprint of individual products. This methodology brings together all carbon impacts (e.g. transportation, raw material extraction, and manufacture). “Carbon Footprint of Four Canadian Wood Products Delivered to the UK as per PAS 2050 Methodology,” a study prepared by the Athena Institute and FP Innovations, assessed four B.C. wood products of interest to the United Kingdom market. (Information is available at www.naturallywood.com, a site offered by Forestry Innovation Investment (FII), a crown agency of the Province of British Columbia). Despite being transported more than 16,000 km (9942 mi), all four Canadian products represent a net carbon sink upon delivery in the United Kingdom.
Using transportation as a metric of environmental impact is limited. The solution is for buildings to be assessed using a lifecycle impact assessment (LCIA) methodology. This process analyzes total environmental impacts of all materials and energy flows, either as input or output, over a product’s life from raw material to end-of-life disposal or rebirth as a new product.
Increasingly, some companies, industries (e.g. the B.C. forestry industry), and countries (such as France) are looking to lifecycle analysis (LCA) as a standard method (defined by International Organization for Standardization [ISO] 14040, Environmental Management: Lifecycle assessment–Principles and framework) with which to assess and report environmental impacts.
Since energy consumption has a direct economic impact on product selection, advocates use transportation as a proxy for other environmental impacts. The manufacturing and shipping of materials also impact air emissions (e.g. smog, global warming, human health, and ozone depletion), along with water emissions (e.g. acidification, eutrophication of lakes and oceans, and aquatic hypoxia) and land emissions (depleted biological services and ecosystem degradation). Today, these impacts can be assessed in a rigorous and systematic way using internationally accepted LCA assessment tools.
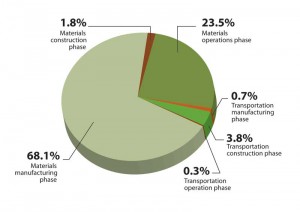
Tools like Building for Environmental and Economic Sustainability (BEES)—from the U.S. National Institute of Standards and Technology (NIST)—provide quick, graphical comparisons of products. (Visit www.nist.gov/el/economics/BEESSoftware.cfm). Athena Institute’s spreadsheet-based application, EcoCalculator, comes pre-loaded with a wide range of envelope and structural assemblies for a series of North American climate zones. It also factors in various transportation options applicable for specific urban centres. (The EcoCalculator is available at www.athenasmi.ca). Athena’s Impact Estimator is a proprietary system that can assess whole buildings with data that can be easily inputted from drawings and/or bills of quantity. All these systems enable the full range of impacts to be considered, not just transportation.
Compared to their international counterparts, North American green building rating systems have been slow to adopt LCA methodology. The U.S. Green Building Council (USGBC) is currently running a pilot LEED credit for LCA analyses of building structure and envelope using the EcoCalculator. However, the Building Research Establishment (BRE) Environmental Assessment Method (BREEAM) for green buildings, as established in the United Kingdom, has already established a protocol for documenting the use of materials with a low environmental impact over the building’s full lifecycle. Credits are achieved based on the U.K. Green Guide ratings for the specification. (Visit www.bre.co.uk/greenguide/podpage.jsp?id=2126).