Integrating mass timber in low-rise construction
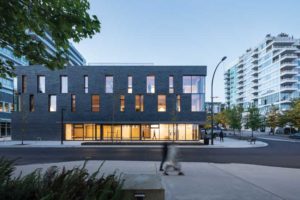
The use of glulam
The foundation is a slab on grade with a 100-mm (3.9-in.) upstand around the perimeter on which the wood structure sits. The primary structure is a hybrid post-and-beam frame. Glulam beams span across the 6.56 m (21 ft) width of the building. The beams are supported on glulam columns on the south side and a combination of glulam and steel HSS columns on the north side. End connections are made using steel hangers and knife plates. The floors and roof consist of five-ply, 175-mm (7-in.) thick CLT panels spanning 6.10 m (20 ft) between beams across most structural bays, with shorter spans at the east and west ends.
Panel-to-beam connections consist of pairs of long stainless-steel screws set at opposing 45-degree angles, while joints between the CLT panels use continuous plywood splines set into the rabbets at the panel edges and screwed in place. This creates a floor diaphragm that contributes to the lateral load-resisting system for the building.
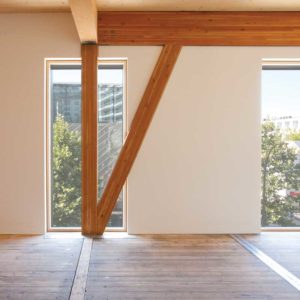
Lateral forces are transferred to the ground by two circulation cores located in the northeast and northwest corners of the building and constructed using continuous vertical CLT panels. The hold down system for the CLT panels consists of anchors, one end of which is embedded in the concrete slab, the other is epoxy-glued into the CLT.
In the east-west direction, additional lateral resistance is provided by bracing between the columns on the south side of the building. On the ground floor where there are large windows, the bracing is steel tension rods connected at the floor and ceiling level to the glulam structure by steel plates. On the upper floors, the bracing consists of diagonal glulam struts that extend from the base of the glulam posts, at an angle of 30 degrees from vertical, to the underside of the beam above. The location of these braces is carefully co-ordinated with the window pattern on the south elevation.
The integrated design process, factory prefabrication of all mass timber components, and the use of virtual construction, enabled the entire superstructure to be erected in just 10 days. With only hand tools and very few deliveries required, noise and traffic impact on the neighbourhood was greatly reduced.
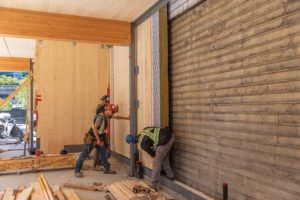
The goal
The integrated design, construction process, and the factory prefabrication of all mass timber components reduced the on-site construction time to just eight days for this entire superstructure. This, in turn, greatly reduced the disruption to traffic in a very busy area of the city.
An additional benefit to residents of the adjacent apartments was the fact that construction of the wood elements required only hand tools, which are much quieter than the various machines required for other types of construction. Architect John Hemsworth says, “People are asking for these buildings because they are visually warmer, healthier, and more environmentally friendly.”
Notes
1 Had glulam columns been used, they would have required a 91-mm (3.5-in.) charring layer on each exposed surface to achieve the two-hour fire resistance rating on the ground floor.
Jim Taggart is a Vancouver-based architectural journalist and educator who has written and lectured extensively on the role of wood in contemporary architecture for more than 25 years. He is the author of the award-winning book, “Toward a Culture of Wood Architecture” (2011) and co-authored with Michael Green, “Tall Wood Buildings: Design, Construction and Performance” (2017). The book was updated in 2020 and a third edition is scheduled for publication in 2024. Taggart was also the 2012 recipient of the Premier of BC’s Wood Champion Award.