Integrating mass timber in low-rise construction
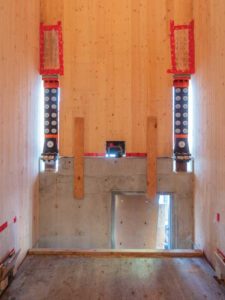
Originally an area of waterfront warehouses and marine service facilities, the neighbourhood has been transformed over time to a high density, mixed-use community centred on the Lonsdale Quay Market and Seabus Terminal. The consolidation of land required by the introduction of higher density zoning had left lots like this exceptionally difficult to develop.
As a family-owned property for three generations, the client was waiting for the right opportunity to do something special on the site. The idea of combining Passive House performance with modern mass timber construction was enthusiastically received, despite the many challenges and uncertainties it presented.
A Passive House approach
A waiver of the on-site parking requirement made it possible to design a three-storey building with a ground floor restaurant and two storeys of offices above that would achieve the full 2.53 FSR permitted by the zoning. To achieve a three-storey building, the project made use of exemptions applicable to the extra thick walls used in Passive House construction. However, the 92 per cent site coverage eliminated the possibility of an on-site staging area for materials and equipment typically required for site construction.
Hemsworth Architecture and Equilibrium Consulting structural engineers were confident a mass timber structure could be prefabricated off-site, but as far as they knew, there was no precedent for a prefabricated Passive House compliant structure built without any setback from a shared property line.
Architecturally, the concept was to use the traditional warehouse vocabulary of an exposed heavy timber structure with brick cladding, but in a contemporary way. This strategy has translated into an exposed glulam post-and-beam structure with CLT floors, stairs, and elevator shafts.
The non-loadbearing brick cladding at the southeast corner of the building is “holding back” and was replaced with large areas of glazing, providing restaurant patrons and office workers with an oblique view of the harbour. The remainder of the south facade includes extensive glazing at the ground level, with a staggered pattern of vertical windows on the upper floors.
While the code permitted the three exterior walls facing the streets and lane to be of combustible construction, it required the north wall abutting the adjacent property to be non-combustible. Such walls are typically built block-by-block in concrete masonry, a method incompatible with Passive House performance. A more sophisticated solution was clearly required, one in which the continuous exterior insulation and vapour barrier for Passive House performance could be installed without accessing the outer face of the wall in the field.
Using an integrated design process involving the architect, structural engineer, building envelope consultant, contractor, mass timber fabricator and installer, a prefabricated and pre-insulated wall system was devised. Alternative detailing, assembly, and installation strategies were explored and optimized using virtual construction.
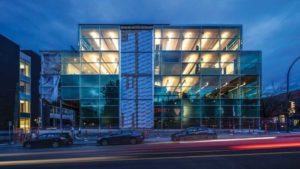
The chosen wall system comprised full-height CLT panels, with a 75 mm (2.9 in.) wide vertical rabbet cut into the inside face of both edges. The panels were laid flat, and the air/vapour barrier was applied to the outside surface, wrapped around the edges and into the rabbets on the inside face; then strapping and 200 mm (8 in.) of insulation was added.
As part of a carefully orchestrated construction sequence, the completed panels were lowered into place by a crane. The vapour barrier was then completed from the inside by sealing the exposed ends (previously wrapped around the panel edges into the rabbeted surfaces) with a second layer of the barrier material across the panel joints. Adjacent panels were connected structurally using a continuous plywood spline, set into the rabbeted joint and screwed in place. On the exterior, metal cladding was field installed on all parts of the wall not obstructed by the adjacent building. Being combustible construction, this wall system required the code consultant to submit and certify an alternative solution.