Integrating mass timber in low-rise construction
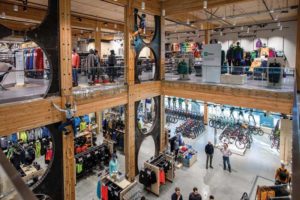
Incorporating CLT panels
The east wall along the common property line is made of solid CLT panel construction, supplied with cladding clips and girts, external mineral wool insulation, and a vapour barrier membrane. Metal cladding was also applied in the field. A 40 per cent glazing-to-wall ratio, permitting much of the south and west walls to be glazed, was achieved through energy modelling.
Electrochromic glass was used on the west facade, providing protection from solar heat gain and glare without the legal and maintenance challenges of fixed shading, which would have encroached into the city right-of-way. Automatically adjusting tin throughout the day, this glass maximizes natural daylight, maintains views, and controls solar heat gain and unwanted glare. It also reduces the installation and maintenance costs associated with interior blinds. To further increase light and views to the exterior, glulam beams are supported on the west side by slender steel hollow structural sections (HSS) columns.
As noted previously, the superstructure is built on top of the post-tensioned concrete slab that forms the roof of the parking garage. The entire east wall of the building consists of two-storey high, vertically oriented five-ply CLT panels connected at their vertical and horizontal joints using plywood splines screwed to the interior surfaces. Where the joints between the panels are visible, a neater, half-lap connection is used. This wall is connected to the CLT stair cores at the northeast and southeast corners of the building and has glulam pilasters integrated into it at 3-m (10-ft) centres, corresponding to the structural bays. Since CLT is a combustible material, this assembly required the code consultant to write and submit an alternative solution to demonstrate an equivalent level of fire safety to the non-combustible construction mandated by the code.
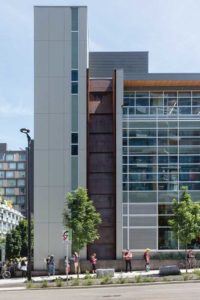
Anchored by the stair cores at either end, this composite CLT and glulam wall takes all the shear forces in the north-south direction. In the east-west direction, CLT walls of the stair cores have seismic dampers recessed into them. These dampers use a resilient slip friction joint (RSFJ) and act as a hold-down and energy dissipation system simultaneously. The devices enable the shear wall to rock, then restore itself to its original configuration without the plastic deformation which most seismic resistant systems are designed for.
While CLT shear walls are codified, the damper system is not and had to be covered by an engineering letter of assurance. Additional steel cross bracing is used in the east-west direction north of the building to counteract torsional forces.
The floors consist of 105-mm (4-in.) thick three-ply CLT panels that span 3 m (10 ft) between the main glulam floor beams. The panels are attached to the beams using long stainless-steel screws, set at opposing 45-degree angles. The panels are then fastened together with 25-mm (1-in.) thick plywood splines, nailed in place to create a floor diaphragm. The panels are covered with a 13-mm (0.5-in.) acoustic mat that also acts as a membrane to prevent moisture damage from the 50-mm (2-in.) concrete topping. The roof is also constructed using three-ply CLT, although in this case, the panels are only 89 mm (3.5 in.) thick.
The steel columns supporting the glulam beams at the west facade extend the full height of the building. They are coated in intumescent paint to achieve the two-hour fire resistance required on the ground floor and the one-hour fire resistance required on all but the top floor above.1 Neither the roof, nor the structure supporting it are required to have a fire resistance rating; therefore, no intumescent paint was used on this level.
Steel chases carrying the cabling for the electrochromic glass are attached to the columns, acting as drag straps tying the horizontal and vertical elements of the structure together.
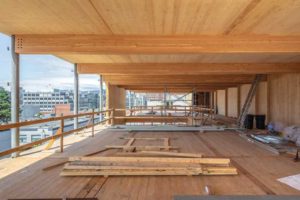
The goal
Architect Austin Hawkins of f2a Architecture believes this project represents a new approach to commercial building design. With its combination of panelized prefabrication, greater emphasis on non-toxic materials, and integrated digital technology, it is a step toward what American author John Greer refers to as the “Ecotechnic Future” – one that is simultaneously closer to both technology and nature.
PH1 – 1 Lonsdale Avenue
This is a small restaurant and office infill project in the Lower Lonsdale district of North Vancouver that employed virtual construction and off-site prefabrication to meet access and constructability challenges. The 7.6 m (25 ft) wide corner lot faces Lonsdale Avenue to the east and a service lane to the west, while the north side abuts an adjacent property and the south side faces the new Polygon Gallery and beyond it, Vancouver Harbour.