Insulation’s crucial role in creating habitable basements
One of the first questions to be asked when designing a basement foundation is “what is the desired functionality of the basement?” On one end of the spectrum, a basement may provide comfortable, fully habitable spaces comparable to the above-grade portions of the building (Figure 1). In the middle of the spectrum, the basement may be less habitable than the main living areas. In other words, it will be cold in the winter and damp during much of the year. On the far end of the spectrum, the basement may serve as a structural foundation only and nothing more.
The Swinton and Kesik study, a Canadian research paper, shows precedence with respect to classifying basements. Although a complete review of the classification system is beyond the scope of this paper, this article is focused on Class A basements as defined by Swinton and Kesik. In their study, Swinton and Kesik list service criteria and limitations/allowances for different classes of basements.1 According to their classification system, Class A basements provide a below-grade living space comparable to the living space of the floors above. To ensure long-term performance, the design and construction of Class A basements must be virtually defect-free and provide critical, redundant moisture control measures. They emphasize the construction of a comfortable and habitable basement (i.e. a Class A basement), which requires much more attention to the components and the system design compared to the design of basements not intended to be used as living spaces. There may also be health and safety requirements, as well as HVAC requirements, which go beyond the scope of the 2005 report by Swinton and Kesik.
Thermal control challenges
Aside from the structural challenges, the thermal challenges for basements include the following functions: (1) facilitating moisture drainage at the face of the exterior insulation down to the foundation drainage system, (2) keeping temperature extremes outside the basement wall, especially cold temperatures, and (3) preventing condensation of the basement air onto the interior of walls in the basement. Insulation strategically placed on the exterior side of the foundation plays an important role in each of these objectives (Figure 2).
Facilitating movement of exterior moisture to the foundation drainage system
In an NRC Institute for Research in Construction (NRC-IRC) Technology Update,2 Swinton et al. describe their approach to managing water exposure to basements is in terms of “two lines of defense”:
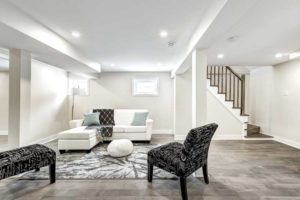
The most effective strategy for managing water is to provide two lines of defense. When exterior basement insulation is used, the first line of defense is the exterior surface of the insulation, which supplies a continuous means of managing water from the ground surface down to the gravel and drainpipe at the footing. The second line of defense is the outer face of the foundation (cast-in-place concrete, concrete block, or wood sheathing in a permanent wood foundation), which can handle the incidental quantities of water that may get by the first line of defense.
It is important to understand this concept because even the best below-grade insulations benefit from some degree of environmental separation.
Since 1999, much research has been dedicated toward accumulating valid experimental data on how insulations perform when placed on the outside of a basement wall in contact with the earth, and when insulation is placed beneath floor slabs. For example, the continuous monitoring of the thermal performance of 13 different basement insulation systems by the NRC-IRC throughout two heating seasons provided some answers.3
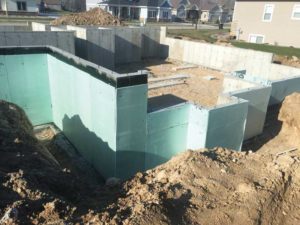
The military “two lines of defense” analogy in the IRC Technology Update is apt. The outer lines of defence are expected to protect against liquid water penetration. This outer layer is sometimes referred to as “effective environmental separation.” If the first line of defence allows liquid water to reach the second line of defence, then the second line must provide some protection against liquid water penetration. In this case, the basement certainly could not be considered a Class A basement.
Drainage does more than just helping in preventing leaks through the basement wall. It helps to address potentially significant reductions in R-values of insulation (up to 50 per cent) due to water absorption and retention; refer to the section “Getting practical” later in this article. However, water drainage does not address the negative effects of water absorption on R-value entirely. If liquid water and water vapour are not properly managed, the insulation R-value is reduced.