Insulating glass: Compensating for internal pressure changes

While these in-transit pressure intervals may be short, lasting several minutes to several hours, they may be quite extreme when elevation differences approach 3048 m (10,000 ft). For example, if an IGU is manufactured at an elevation of 1219 m (4000 ft) and adjusted at the factory for sea-level pressure, but it goes over a 3048 m (10,000 ft) pass on the way to its final installation site, it will experience the full 3048 m (10,000 ft) difference compared to sea level. Whether or not the edge seal breaks depend on the exact makeup of the IGU.
Referring to the equation for gas pressure change, if the starting elevation at the manufacturing site is known (P1), and the elevation at the final installation site is known (P2), and the volume of air or gas in the IGU is known (V1), then a professional (such as an engineer) who may or may not be employed by the IGU manufacturer, can calculate V2 for the volume of air or gas at the destination and submit the results to the specification professional.
In addition to the ambient conditions, the amount of glass deflection is also dependent upon the interplay of many configuration-related variables. These include glass type and thickness, glass area, dimensional geometry (aspect ratio), framing profile design and material, IGU cavity width, edge seal design and materials, sealant and spacer selection, and spacer size.
Pressure compensation
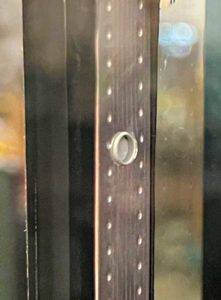
Generally, IGUs are specified and designed to withstand breakage or other effects from these dynamic and static forces. In some cases, the fenestration manufacturer or IGU fabricator will provide units that will be permanently deflected at the installation location but are well within the tolerance of breakage.
In other cases, some IGUs are manufactured or installed with a pressure compensation scheme that adjusts internal gas pressure based on the intended final installation location. It is up to the IGU fabricator to determine how to achieve this. Each approach has advantages and disadvantages, as well as need certain considerations during installation (glazing).
Capillary or breather tubes
In this method, permanent air tubes are inserted in air-filled IGUs after fabrication to allow for pressure equalization. Stainless steel capillary tubes have an inside diameter of 0.53 mm (0.021 in.), while aluminum tubes have a diameter of 0.81 mm (0.032 in.). In this method, permanent air tubes are inserted in air-filled IGUs after fabrication to allow for pressure equalization. Stainless steel capillary tubes have an inside diameter of 0.53 mm (0.021 in.), while aluminum tubes have a diameter of 0.81 mm (0.032 in.). Although similar, breather tubes, made of metal or plastic, are significantly larger with a diameter of 3 mm (0.12 in.) but are not as common as capillary tubes. Note, neither capillary or breather tubes are applicable for argon or krypton gas-filled IGUs.
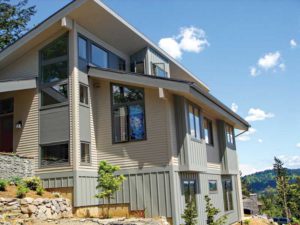
Installing contractors and glaziers should follow the fabricator’s instructions on where the tube is to be placed in relation to the top, sides, or bottom of the installed IGU. Usually, the tube is positioned near the top of the IGU pointing down and is sealed prior to the glazing operation. Specify that the tube must have adequate clearance from the glazing frame or accessories within the glazing system during installation.
For IGUs which are pre-glazed and shipped to the construction site prior to sealing, the framing system should be specified to provide access to the capillary tube so proper sealing of the tube can be carried out onsite within the timeframe designated by the fabricator.
Daily fluctuations in cavities pressure-compensated with open capillary tubes are covered in FGIA’s document, IGMA/GANA TB-1601-95(14), Guidelines for Capillary Tubes.
Desiccant adsorption/desorption
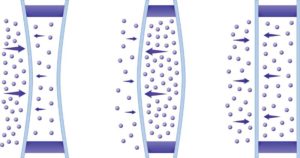
In this approach, a sacrificial gas typically is adsorbed from the cavity into a desiccant material. This reduces the pressure in the cavity relative to the atmospheric pressure at the time of manufacture. It also allows sealing at atmospheric pressure, without the need to puncture the spacer or glass for pressure adjustment after sealing.
The sacrificial gas must be mixed into the insulating gas at the time of filling. The desiccant must adsorb the sacrificial gas, but not the insulating gas. The IGU likely will be glazed with its glass bowed slightly inward. This bow will need to be accounted for when adding accessories like tape-applied grills to the glass.
While there are other methods, it stands to reason the geographical location of where the IGUs are manufactured and where they typically ship would affect the need for compensation methods. For example, if a manufacturer is in Vancouver, British Columbia, and all of the IGUs are shipped to Calgary, Alberta, they would need to have a compensation system in place.