Innovative Sound Control Strategies: Achieving compliance with 2015 code requirements
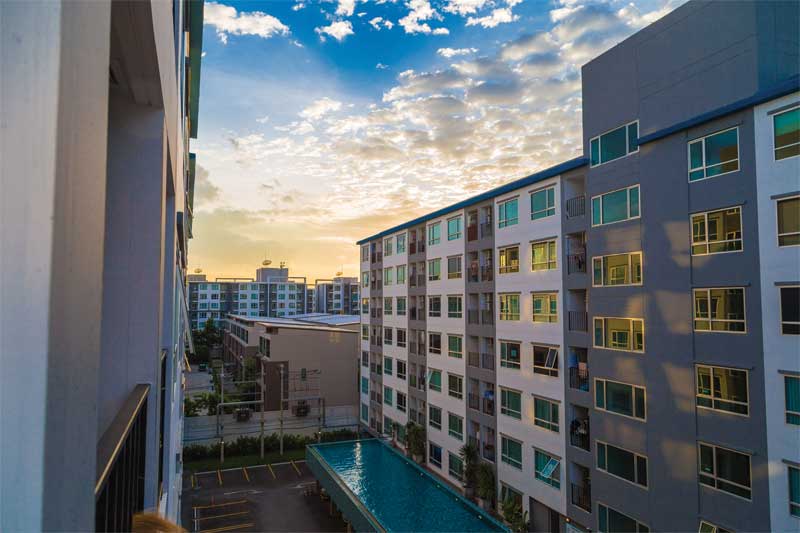
By Robert (Bob) Marshall, P.Eng., BDS, LEED AP, and Robert Hartogsveld, CTR, CCCA
The 2015 edition of the National Building Code of Canada (NBC) introduced 360 technical revisions that address contemporary concerns and raise standards even as Canada is in the midst of a construction boom.
The two most timely and impactful code revisions for building and design professionals are Part 3, “Fire Protection, Occupant Safety and Accessibility,” and Part 9, “Housing and Small Buildings.”
Part 3 provides an affordable housing option for Canada’s rapidly growing population. It permits the construction of residential, business, and personal services buildings up to six storeys in height using gypsum and traditional combustible construction materials—particularly wood framing assemblies. Advances in wood research and building technology over the years have led to stronger, safer, more sophisticated fire-protected products that make mid-rise wood construction a more viable option.
Part 9 of NBC 2015 raises the bar for project sound control standards with the introduction of the apparent sound transmission class (ASTC) rating. This rating gives a more comprehensive description of noise between dwellings—including sound transmitted through flanking paths—than the longstanding sound transmission class (STC) rating.
This article outlines the importance of each of these code revisions, and demonstrates how professionals can create smart sound-control strategies that exceed code requirements and reduce project costs.
Wood-framed mid-rise construction: An affordable housing solution
Canada is one of the fastest-growing developed nations in the world, largely due to the continuous wave of immigrants seeking new homes in the country in recent years. According to Statistics Canada, the nation welcomed 320,932 immigrants as permanent residents between July 2015 and July 2016—its highest annual total in more than a century. These numbers are expected to increase.
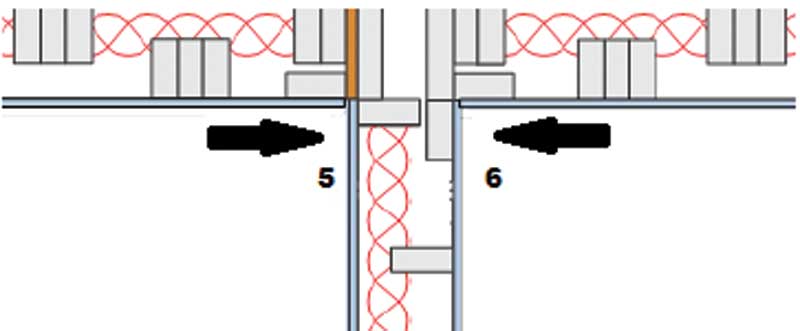
Images courtesy CertainTeed
Metropolitan areas across the nation, from Vancouver to Halifax, are receiving the lion’s share of this population influx—as well as the accompanying rising real estate prices. The record-breaking detached home prices in many of these areas are prompting more people to look into townhouses and condos, also skyrocketing in price. The Toronto Real Estate Board recently reported the benchmark price for a detached home in the Greater Toronto Area (GTA) was $952,983 in July—a 21.1 per cent increase from last year. The same report showed the average condo price for the metropolitan area was $402,865, increasing 9.2 per cent from the same month in 2015.
This high equity is beneficial to some—current homeowners can complete residential upgrades to create an income-producing secondary suite within their homes. However, for those looking for a new home, the nationwide need for more affordable housing options is clear. One very workable solution is mid-rise multi-family residential construction—specifically, construction of fire-protected wood-framed buildings of up to six storeys nationwide, and cross-laminated timber (CLT)-framed buildings of 12 or more storeys in Québec and British Columbia. Since its announcement, the new code revision has been adopted by the building codes of those two provinces, along with Ontario and Alberta.
The use of wood framing in mid-rise construction has a number of advantages. Most importantly, it costs less than poured concrete for mid-rise buildings. A recent report from the Building Industry and Land Development Association (BILD) estimates wood framing can save project teams $300 to $400/m² ($30 to $40/sf), or up to 20 per cent more than steel and concrete. Those numbers translate to $20,000 to $25,000 savings for a 100-m2 (1000-sf) home. (Paul J. Bedford’s article, “Unlocking the Potential for Mid-Rise Buildings: Six-Storey Wood Structures” was published in 2013 by the Building Industry and Land Development Association (BILD).) This means mid-rise construction can create more affordable prospects for property owners, developers, and home buyers in desirable neighbourhoods that normally have high-priced housing.
As the only renewable construction product, wood has many advantages over other materials. Its processing requires less energy than concrete or steel in terms of resource extraction, manufacturing, and transportation, and makes less of a carbon footprint. According to a 2005 study, that was led by the Consortium for Research on Renewable Industrial Materials (CORRIM), the life cycle of steel and concrete results in 26 per cent to 31 per cent more greenhouse gas (GHG) emissions than that of wood.
However, in a wall assembly, wood framing is only as good as the surrounding materials. These include insulation, gypsum drywall, sealants, and putties. Such components are especially important given the requirements of NBC’s new ASTC rating to address flanking paths. Due to the many flanking paths typical in high-density projects—such as vertical and horizontal wall intersections—acoustic control can be a challenge to address. When discussing any multi-family dwelling, sound control is a must for ensuring an acceptable level of peace and privacy for residents.