Innovations in protecting construction joints
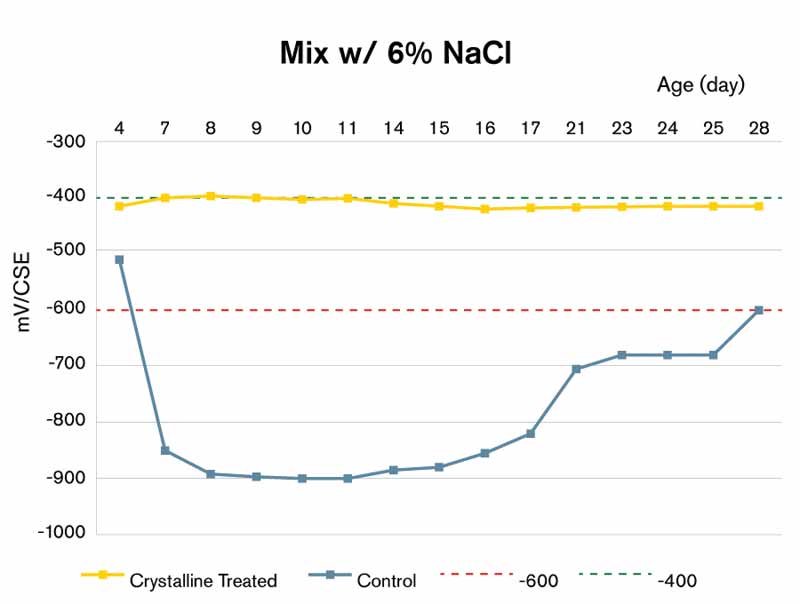
Phase 1: Corrosion
Overall, when the coating is applied at the joint, the interface and bottom section of rebar are coated with crystalline coating. Hence, when water penetrates through cracks, it contacts the coated rebar instead of the rebar directly. Thus, in this phase, the corrosion resistance of reinforcement steel with crystalline waterstop coating was compared with uncoated rebar. The coating was applied to some samples. After curing, the coated and uncoated samples were directly immersed in a sodium chloride (NaCl) solution for a certain period. This setup simulates a marine environment.
At the end of each testing period, a visual inspection of the specimens was conducted to compare the level of corrosion. Additionally, a half-cell potential measurement device was employed to monitor the corrosion process of the specimens in accordance with ASTM C876-09, Standard Test Method for Corrosion Potentials of Uncoated Reinforcing Steel in Concrete. Further, the potential readings were analyzed in accordance to the International Union of Laboratories and Experts in Construction Materials, Systems, and Structures’ (RILEM) book TC-154, EMC: Electrochemical Technique for Measuring Metallic Corrosion.
After monitoring the samples for 28 days, half-cell potential measurements showed crystalline coating material directly applied on the rebar surface, dramatically delayed the corrosion activity compared to the control (uncoated) samples. These results were also confirmed by a visual inspection (Figure 3).
Phase 2: Bonding
Previous studies have shown any coating on the reinforcement bars in concrete structures could affect the ultimate bond strength of the rebar. Therefore, as part of this research project, it was critical to assess the impact of crystalline coatings on the bond strength of embedded rebar with surrounding concrete. One of the most commonly used test methods for assessing the ultimate bond strength of embedded rebar is the pull-out test. According to RILEM book RC 6, Bond test for reinforcement steel, five samples are needed to make the comparison in this test.
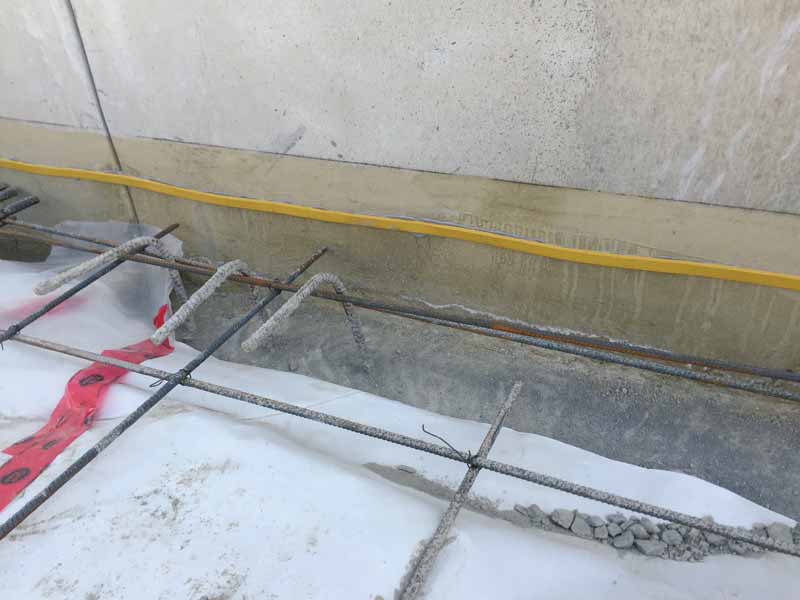
Therefore, 10, 10M black steel rebars were cut into 152 mm (6 in.) pieces. After cleaning the bars, crystalline coating was brushed onto five rebars. The coated bars were then cured for hardening. After 24 hours of initial curing, the coatings had sufficiently hardened. The bars were then placed into cylindrical-shaped moulds. A batch of concrete was prepared in accordance with ASTM C192, Standard Practice for Making and Curing Concrete Test Specimens in the Laboratory, and poured into the cylindrical moulds. Filled concrete moulds were transferred into the curing room, covered with plastic tenting, and sprayed with water every day for 28 days. After 28 days of curing, the specimens were subjected to a modified pull-out test using a compression machine.
The results show the crystalline coating did not reduce the bond strength of the reinforcement steel bar with its surrounding concrete, but increased this ultimate bond strength by 3.85 per cent. The control (untreated rebar) had a bond strength of 5.501 MPa (797.8 psi) while the treated sample had a bond strength of 5.717 MPa (829.18 psi).
Conclusion
Based on the complexity of new buildings, limitations of traditional methods, and the goal to make more sustainable structures, advanced waterproofing solutions, especially for high-risk areas such as construction joints, seem necessary. Crystalline coating and swelling waterstop can provide a reliable barrier and prevent water penetration through the joint during its service life. The solution not only prevents water penetration, but also has the potential to reduce the corrosion of rebar in concrete without any negative effects on the ultimate bond strength.
Alireza Biparva, M.A.Sc., LEED GA, is technical manager and concrete specialist at Kryton International. He has more than 10 years of experience in the field of concrete permeability. Biparva oversees a variety of research projects, focusing primarily on concrete permeability studies and the development of innovative products and testing methods for the concrete, waterproofing, and construction industries. He is an active member of the American Concrete Institute (ACI). Biparva has published several research papers in international journals and conferences on concrete permeability, waterproofing, durability, and sustainability. He can be reached at alireza@kryton.com.