Innovations in protecting construction joints
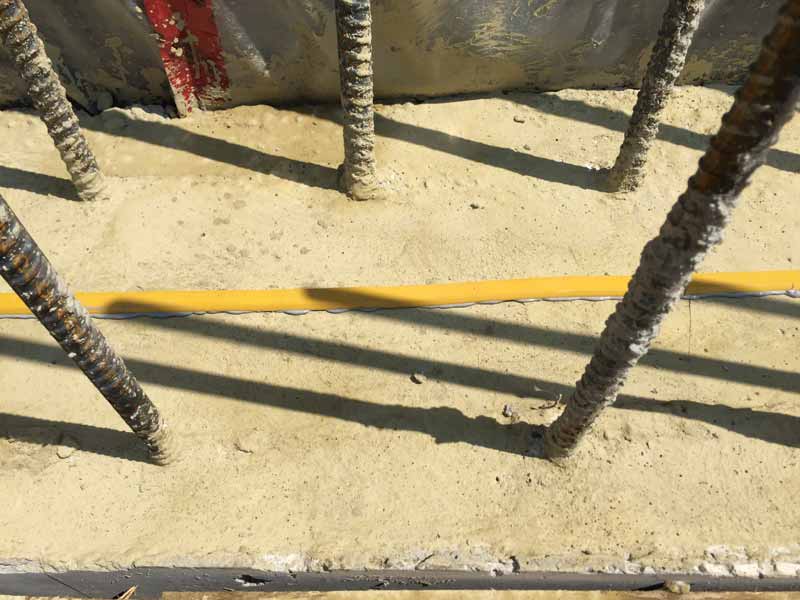
By Alireza Biparva
Proper waterproofing of construction joints plays a vital role in fortifying below-grade concrete structures. Construction joints are stopping places—caused by non-continuous concrete pour—and a plane of weakness. Hence, they represent the most vulnerable part of the structure from a waterproofing perspective.
Without an effective joint waterproofing system known as a waterstop, it is not a matter of if the joint will leak, but rather, when it will leak. Leakage or dampness not only impacts the serviceability of the structure, but also causes major deterioration such as corrosion of reinforcing steel in concrete. Water penetration is a global problem as it reduces the service life of concrete structures. It is responsible for more than 80 per cent of damage to reinforced concrete facilities, thereby continuing to rack up the repair costs for owners and developers.
Traditional method
One of the technologies used to waterproofing joints is a polyvinyl chloride (PVC) waterstop, also known as the traditional “dumbbell” due to its shape. These plastic sheets are placed across the joint before the concrete is poured to create a physical barrier for blocking water penetration. This type of waterstop relies on the ribs in the design to prevent water from passing through the joint. The PVC waterstop is great for blocking water, and is relatively inexpensive, but has limitations. Improper compaction around the waterstop creates a pathway for water—PVC waterstop can bend while concrete is poured, forming a tunnel and area where water can infiltrate. This does not mean the waterstop is not working; an installation deficiency or concrete compaction is causing leakages. To make matters worse, it is virtually impossible to recognize the problem until the joint begins to leak, which is too late. Additionally, when PVC is considered as a single barrier, water can seep in until it reaches the waterstop. As you can see in Figure 1, the rebar on the water side of the joint is exposed to the water and will corrode.
Alternative methods
These difficulties have opened the door for other waterstop systems such as hydrophilic swelling strips and crystalline waterstop coating.
The swelling waterstop is a synthetic rubber strip designed for waterproofing construction joints. Synthetic rubber swelling strips act as a physical barrier and can swell up to 1000 per cent of original volume to seal the construction joint and stop water flow. Its ability to swell and block water intrusion, not only under hydrostatic conditions, but also when facing salt or contaminated water, sets it apart from other products. This is important considering the state of the moisture in below grade and marine environments.
Crystalline waterstop coating is a powder mixed with water to a slurry consistency, and brushed on the joint area. It utilizes advanced integral crystalline waterproofing (ICW) technology to block the movement of water through concrete joints and acts as a chemical barrier. The crystalline waterstop coating exhibits a hydrophilic property, meaning, the special chemicals in the coating react on exposure to water, allowing millions of long, needle-shaped crystals to grow deep into the concrete mass. These crystals permanently block and prevent the passage of water through capillary pores, micro-cracks, and joints, thereby making the joint waterproof. As long as moisture remains present, crystals continue to grow throughout the concrete. Once the moisture content is reduced, the crystalline chemicals lie dormant until another dose of water causes the chemical reaction to begin again.
Crystalline waterstop coating can be used in conjunction with a swelling waterstop at all static concrete-to-concrete joints where water penetration is a concern. This is called a double protection system. Crystalline waterstop coating as single protection can also be employed as a dampproofing treatment when the joint is subjected to water with low or no hydrostatic pressure.
Since crystallization takes some time to occur, corrosion of rebar on the wet side is a concern in both single and double protection systems as it is with the PVC system (Figure 2). However, testing has demonstrated the coating not only acts as a chemical barrier to prevent water penetration, but also protects the rebar.
To investigate the effects of crystalline coating, a joint research study was conducted by a concrete and waterproofing solutions manufacturer and a University of British Columbia co-op student. This study was performed in two phases at the Kryton Research Centre, Vancouver, in December 2016. In the first phase, half-cell potential measurement, as well as visual inspection, was used to analyze the corrosion mitigation of coated steel reinforcing bars embedded in concrete. In the second phase, in parallel to the corrosion tests, a modified pull-out test was employed to assess the bonding of the materials with concrete and steel.
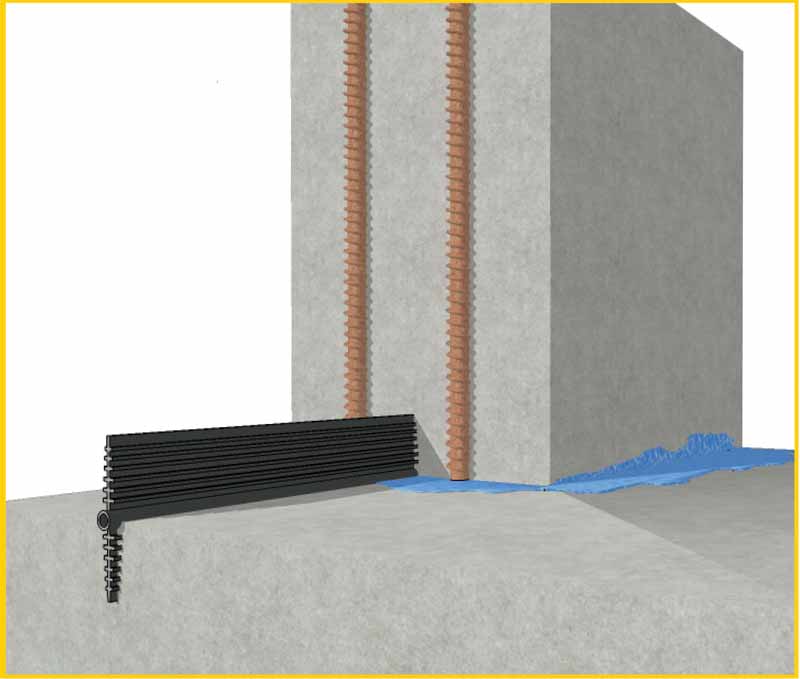
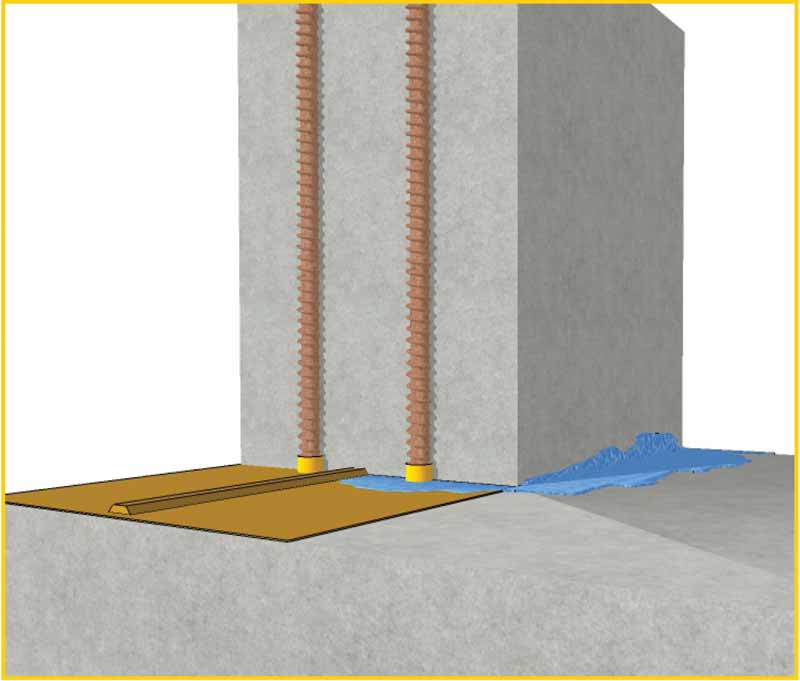