Innovation in design drives formwork solutions
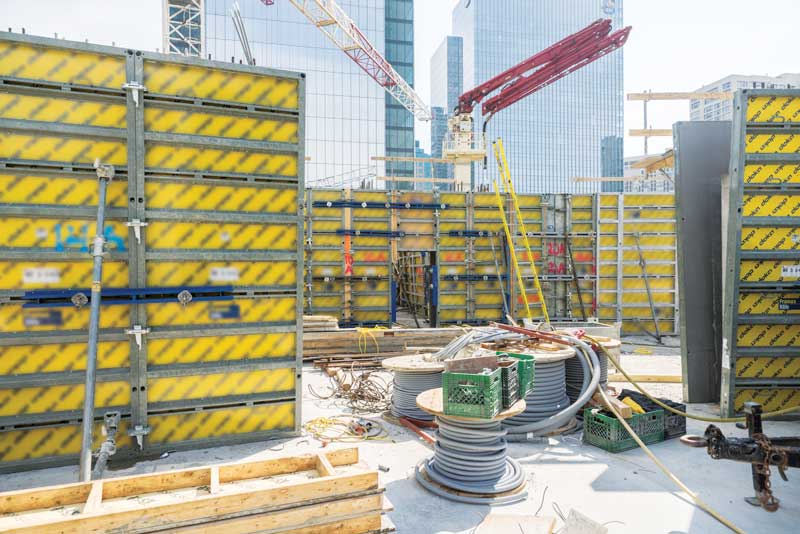
Formwork challenges
NCL will be a landmark building exemplifying design excellence, as well as a community space inspiring thought, collaboration, and conversation. The design is the greatest challenge on this project, given its very high slabs and architectural exposed walls and columns, which translate to a low amount of repetitive work. Therefore, most of the forming solutions implemented here are custom. Many of the project’s steel and concrete components are built simultaneously and incorporated within each other.
The solution
For this design, it was necessary to provide a tieless formwork solution for the architectural columns and beams. The tieless solution eliminated concerns and potential conflicts with reinforcement steel and composite steel structural components. In addition, it provided a smooth final architectural concrete finish, as patching of holes from ties was eliminated. With this method, challenges introduced by complicated column cross-sections, large column heights, and stringent specifications on concrete finish requirements could all be met.
The formwork provider’s team of engineers used 3D modelling from the architect to complete the execution and assembly drawings for the customer. Weekly meetings with the contractor, Stuart Olson Company, were required to stay atop ever-changing project demands and ensure the formwork solutions achieved a high-quality architectural concrete finish.
Conclusion
Specific engineering requirements introduced by innovative design choices can be met by involving the formwork company early in the process, and by working with its in-house engineers to find the best customized solution. The formwork company can also provide ongoing engineering and onsite support throughout the project to ensure the solutions are working. Ten York and NCL are two examples of groundbreaking structures where the architect, contractor, and formwork supplier must work closely together to achieve desired designs.
Effective column formwork can be used to tackle issues such as complicated column cross-sections, large column heights, multiple formwork reuse cycles, and tough specifications with regards to the concrete finish.
HOW TO CHOOSE THE BEST FORMWORK SYSTEM FOR A JOB |
By working closely with the formwork provider right from the beginning, building professionals will be able to use formwork efficiently and to its full capacity. It is crucial to eliminate unplanned costs and delays by asking questions from the start and working with the formwork partner through every step of the project.
1. Evaluating total project needs. 2.Development of cost-effective solutions. 3. Value engineering of project design. 4. Estimating total costs and schedule. 5. Job-built versus equipment rental. 6. Engineering design requirements. 7. Development of a jobsite plan. 8. Management of equipment delivery and returns. 9. Assembly and inspection onsite. 10. Jobsite closeout. |
Michael Schaeffer is the vice-president of sales for Doka North and South America, and has been in the design/construction industry for more than 25 years. His career in formwork has included front line sales, operations, and organizational development, but his current responsibilities include sales management, product development, customer solutions, marketing, and project management. He can be reached at michael.schaeffer@doka.com.