Influence of gaps on roof insulation performance
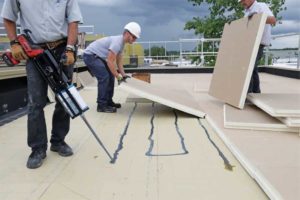
By Jean-François Côté, PhD, OCQ
As the construction industry evolves, product development and implementation of energy efficient solutions increase building performance. Insulation materials and assemblies, including roof insulation, are part of this ongoing process. Increased understanding of the dynamics of low-slope roof assemblies has helped design better performing roofs, from a thermal point of view, as well as other considerations such as moisture management and resistance to wind uplift.
The recommended practice in the roofing industry is to use two layers of insulation and stagger the joints. By doing this, if gaps open between insulation boards, the joints in the first layer will not be positioned directly over joints in the second layer. Consequently, the thermal efficiency of the roof assembly is considered to be less penalized when gaps appear because an insulation layer is always covering a gap. However, this does not prevent insulation from shrinking, so there could still be some appearance of gaps and different gap widths in those insulation materials.
What is the impact of these insulation gaps in the thermal efficiency of roof assemblies? Experiments were performed by RDH Building Science, National Research Council Canada (NRC), and a manufacturer of insulation materials in their respective laboratories to better answer the question. To define parameters for the testing, parameters by which insulation materials shrink needed to be first considered.
Thermal expansion and contraction
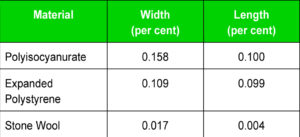
All materials have a coefficient of thermal expansion. This behaviour is inherent in the nature of materials. When a material is heated, it increases in dimension (expansion) and decreases (contraction) when cooled. The thermal expansion and contraction is a totally reversible phenomenon. The dimensions of a material at a given temperature remain unchanged even after cycles of exposure to colder or warmer temperatures. Some materials exhibit larger change in dimensions than others, and the coefficient of thermal expansion is a number used to quantify this change. Further, the change in dimension may not be the same in all directions for a given material.
Specimens of three types of insulation materials (polyisocyanurate [polyiso], expanded polystyrene [EPS], and stone wool [SW]) were cut to a size of 600 x 600 mm (24 x 24 in.) at room temperature. They were then cooled to –15 C
(5 F) and specimen dimensions were measured at –15 C. Figure 1 shows the average percentage of shrinkage in width and length. Unsurprisingly, SW shows the lowest shrinkage of the group by at least an order of magnitude. Both plastic foam insulation materials (polyiso and EPS) show similar results with polyiso being the worst case in width at 0.158 per cent shrinkage. If this is transposed to a roof employing 1.2 x 1.2-m (4 x 4-ft) insulation boards, thermal expansion and contraction can create relatively small gaps of 1.9 mm (75 mils) in size between polyiso boards.