Influence of gaps on roof insulation performance
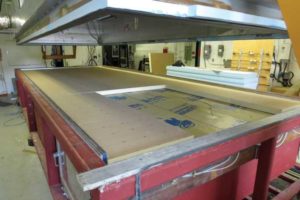
Photo courtesy National Research Council Canada
Hot box testing
The next part of the study was performed with full boards by NRC in Ottawa with a calibrated hot box. The equipment measures 2.4 x 6.1 m (8 x 20 ft) and replicates conditions acting on the roofing assembly at an intermediate scale. It is composed of two chambers and the test specimen is exposed to a temperature difference between the top and bottom chambers. The energy required to maintain both chambers at constant temperature conditions is measured and converted into an effective R-value. The testing was conducted according to the ASTM C1363, Standard Test Method for Thermal Performance of Building Materials and Envelope Assemblies by Means of a Hot Box Apparatus, specification for calibrated hot box (Figure 4).
For this study, the top chamber temperature was kept at 4.5 C (40 F) and the bottom chamber temperature was maintained at 41.5 C (107 F) (23 C [73 F] mean temperature and 37 C [99 F] temperature difference). A vapour impermeable air barrier was installed under the insulation boards to avoid any airflow or moisture movement into the specimens.
Assembly 1 was composed of two layers of 63.5-mm (2.5-in.) polyiso boards with staggered joints (this can be considered the reference). Joints were spaced by 0.60-m (2ft) between the layers in both directions. Assembly 2 used the same configuration but introduced 13-mm (½-in.) gaps at every joint in both layers of insulation. Assembly 3 was constructed with a single layer of 127-mm (5-in.) polyiso with no-gap shiplap joints. Finally, Assembly 4 used a single layer of 127-mm polyiso with shiplap joints with an added 13-mm gap at all joints in both directions (the shiplap edge is present on all edges of the boards).
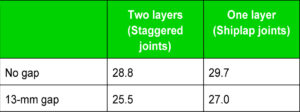
The results of the hot box testing are presented in Figure 5. When gaps are closed, shiplap joints (Assembly 3) provide marginally better R-values (3 per cent) than staggered system (Assembly 1), which is opposite to what one would have seen in the small-scale testing. When the gap size is increased to 13 mm, the difference in R-value increases in favour of the shiplap configuration which retains 90 per cent of the reference R-value as opposed to a 85 per cent retention for staggered joints. This seems to indicate using shiplap polyiso in a roofing assembly may bring benefits in terms of thermal performance when gaps do not exceed the dimension of the shiplap lip. The impact of increasing the gap size further will be part of future studies.
The increase in performance observed for shiplap polyiso is consistent with claims from polyiso manufacturers that R-value per inch of polyiso increases with thickness. A single layer of polyiso is composed of insulation foam between two facer materials. At an equivalent thickness, two layers of polyiso introduce two additional facer materials, which are not as thermally efficient as the thickness of foam they replace. Field trials confirmed an increase in speed of installation for shiplap joints over staggered systems (not so much for mechanically attached assemblies). Changing practices for roof insulation installation will not happen tomorrow. Polyiso has generally not been used in large thicknesses in Canada because failures have been observed where thick boards showed excessive cupping, curling, or unacceptable variations in thickness. Polyiso manufacturers capable of providing stable thick boards with shiplap edges might provide tangible benefits to the industry.
This study confirmed the presence of gaps between boards of insulation will cause a reduction in R-value. The different parameters that could cause insulation boards to shrink (coefficient of thermal expansion, dimensional stability, and moisture) may create gaps up to 25 mm, although typical dimensional stability data shows 13 mm is a more realistic maximum gap size for polyiso. Under these conditions, gaps created between polyiso boards with shiplap edges cause a smaller reduction (10 per cent) of the thermal performance of the assembly compared to dual layers with staggered joints (15 per cent).
Jean-François Côté, PhD, OCQ, is the director of standards and scientific affairs for Soprema. A registered chemist in Québec, he chairs the Canadian Standards Association (CSA) A123.23 technical committee on bituminous roofing materials. Côté is also an active member of ASTM International, Asphalt Roofing Manufacturers Association (ARMA), Polyisocyanurate Insulation Manufacturers Association (PIMA), and Underwriters Laboratories of Canada (ULC). He can be reached at jfcote@soprema.ca.