Industrial buildings in wood
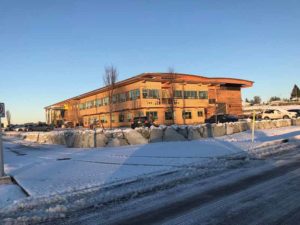
Hybrid facility
A Canadian mass timber design-build firm constructed a new fabrication plant in Abbotsford, B.C. The 4600-m2 (50,000-sf) plant includes two visually connected but structurally separate buildings—a 36.5 x 109.5-m (120 x 360-ft) warehouse and workshop space and an L-shaped administration facility.
A kit of parts
Constructed in just five days, the warehouse consists of prefabricated ‘tall wall’ panels, each measuring 3.6 m (12 ft) wide and 9 m (30 ft) high. The roof panels are 13.6 m (2 ft) wide and 19 m (63 ft) long, spanning between the perimeter walls and a central longitudinal glulam beam, and are constructed with glulam edge beams, bridged laterally by solid-sawn joists. The wall panels have laminated strand lumber (LSL) studs.
All the panels were factory finished with plywood sheathing inside and out, fibreglass insulation, and (in the case of the wall panels) an exterior moisture barrier. They were delivered by truck and lifted directly into place. The wall panels carrying the roof loads at the perimeter of the building were kept vertical with temporary shores until the roof panel was installed, stabilizing the structure.
The roof panels were connected in the field with a second layer of plywood, laid in a staggered pattern overlapping the joints between panels. Glued in place, the two layers of plywood create a continuous diaphragm, transferring lateral forces to the vertical structure and hence to the ground. The central glulam beam, on which the end of the panels bear, is supported on glulam columns at 7.2-m (24-ft) centres. This divides the interior into two rectangular spaces. One is dedicated to custom fabrication projects and the other is used to manufacture dowel-laminated timber (DLT) panels. The large column spacing permits the passage of lifting equipment and prefabricated assemblies.
Engineering innovations for elegance and economy
This apparently simple building contains numerous innovative engineering solutions, designed to make the structure more efficient and economical. For example, the end wall contains two large openings, a feature normally requiring the addition of cross-bracing elsewhere in the building. Instead, the project engineers designed the shallow sections of wall above the doors as box beams. Since these beams contribute to the overall lateral resistance, additional bracing was not required.
The glulam edge beams supporting the roof panels have a curved profile for performing multiple functions. It follows the shape of the bending movement diagram and is thicker mid-span (where the forces are greatest and thinner at the supports where these forces are lowest). This saves material and cost. It also creates a slope in the roof to promote drainage.
These efficiencies, combined with a comprehensive application of prefabrication techniques and the speed of construction, resulted in a structure delivered at a cost comparable to that of a tilt-up concrete or steel frame equivalent.

Dowel-laminated timber
Like nail-laminated timber (NLT), DLT consists of solid-sawn lumber fastened together face-to-face to make a solid panel. However, the fabrication of DLT is a mechanized process in which the boards are first milled, then compressed together by a machine. Holes are drilled through the multiple laminations, and kiln-dried dowels are inserted. As these dowels expand to reach their equilibrium moisture content, a strong mechanical bond is achieved.
Despite this bond, the dowels simply enable the multiple laminations to be handled as a single panel. They do not contribute to its strength. DLT panels of up to 18 m (60 ft) are possible using finger-jointed material. Since DLT panels contain no nails or screws and only miniscule amounts of glue, they can be easily worked or modified with hand or machine tools.
Conclusion
Although different in their design and execution, these three buildings share a common theme. Each embodies the values of the organization commissioning them and, in the case of the Whistler and the Abbotsford manufacturing facilities, built them as well. In a sector of the construction industry where economy and utility have long been the sole drivers of design, these projects add other criteria. They are all healthy and attractive workplaces supporting employee well-being and demonstrating good design has a valuable role to play in every aspect of life.
Jim Taggart, FRAIC, teaches wood design at the British Columbia Institute of Technology (BCIT) in Vancouver. He is also the editor of Sustainable Architecture and Building Magazine (SABMag) and the author or editor of more than a dozen books, including the award-winning Toward a Culture of Wood Architecture (2011). Taggart has also lectured extensively on the role of wood in contemporary architecture throughout North America, Scandinavia, and Australasia. He is a Fellow of the Royal Architectural Institute of Canada (RAIC) and the recipient of the 2012 Premier of British Columbia’s Wood Champion Award. He can be reached at architext@telus.net.