Industrial buildings in wood
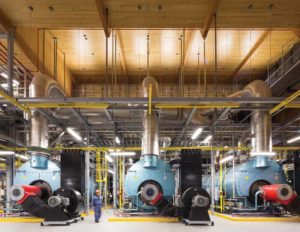
Photo © Ema Peter
UBC Campus Energy Centre
The University of British Columbia (UBC) Campus Energy Centre (CEC) supplies the new hot water district energy system serving more than 130 buildings on the school’s Vancouver campus. Completed in 2015, CEC replaces a steam-based district heating system dating back to the 1920s. Since it operates more efficiently, CEC has reduced the overall energy consumption on the campus by 22 per cent.
A low-carbon solution
With its large owner-operated real estate portfolio, UBC is concerned not only with the initial cost of its buildings, but also their overall life-cycle performance. Life-cycle assessment (LCA) considers both the embodied and operating energies of buildings, together with a wide variety of other potential environmental impacts from the structure.
With several innovative mass timber structures having been completed—the latest being Brock Commons Tallwood House—UBC’s team is well aware of the advantages of building in wood, including carbon storage, low embodied energy, durability, and recyclability. All of these factors contribute to superior life-cycle performance.
Design approach
The 1860-m2 (20,000-sf) facility includes an 18-m (60-ft) high boiler room with a mezzanine as well as a two-storey office and administration area with standard ceiling heights. Juxtaposing these program elements creates a stepped cross-section. When combined with the multiple penetrations of the building envelope for intake ducts and exhaust flues, this cross-section could have resulted in a disparate appearance, at odds with the surrounding buildings.
To unify the design, the architects at Dialog devised an exterior screen of zinc panels, supported 0.9 m (3 ft) off the building on a light-gauge steel frame. The screen was manipulated to provide transparency and weather protection as well as announce entry points. The solid panels are perforated at certain areas for air intake louvres and other service penetrations. On the west elevation, the screen rises above a large area of glazing to reveal the inner workings of the boiler room.
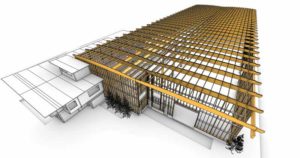
Images courtesy StructureCraft Builders
A hybrid structure
Also revealed through these windows is the primary structure of the boiler process area: a Douglas fir glued-laminated (glulam) timber post-and-beam frame with infill walls of seven-ply, 225-mm (9 ½-in.) thick CLT panels. The sloping roof is also constructed using CLT panels spanning the full width of the space.
The 18-m (60-ft) high SPF, CLT walls create a continuous enclosure around the mechanical equipment, giving the vast space a sense of warmth unusual in an industrial building. All materials were sourced in British Columbia and fabricated in Penticton.
The apparent simplicity of the structure is the result of innovative details devised by structural engineers Fast + Epp. While the CLT walls of the boiler room appear continuous, the height of the space exceeded the 12-m (40-ft) maximum length of panels currently available. This necessitated the stacking of two panels, one on top of the other, above and below a horizontal glulam beam. To maintain visual continuity of the exposed surface, the panels are machined with a half-lap profile, thereby concealing the beam and creating a neatly mated joint. Where loads are greatest, the glulam beams and columns are replaced with steel members.
The CLT wall panels are notched to accept the glulam beams and designed to resist both the dead load of the roof and the lateral loads imposed by wind and seismic forces. On the west side of the building, where the CLT wall panels are omitted to permit views into the boiler room, roof panels are supported on a glulam beam. The connections between the panels are made using pairs of long stainless-steel screws, set at opposing 45-degree angles. This enables both walls and roof to act as diaphragms. The sloping roof of the boiler room is divided into three sections. The steep mid-section is supported by an inclined hybrid wood/steel truss, concealed from below by the CLT ceiling. CLT was also used for the walls of the administration offices, although the electrical room below—requiring a two-hour fire-resistance rating—is constructed in concrete masonry.
Embodied energy
The structure of CEC is pragmatic, employing different structural materials as dictated by function. In comparison to an all-steel equivalent (the construction type most commonly employed for this kind of building), the hybrid wood system reduces the overall construction carbon use by 88.3 tonnes (97.3 tons).
With its exterior cloak of zinc and glass, the building fits comfortably into its campus context, while the exposed wood interiors create a warm and inviting environment for employees.