Improving the appearance of hot-dip galvanized steel
Altering the appearance of HDG steel
Although it can be difficult to control the initial appearance of hot-dip galvanizing, design professionals continue to turn to it for a modern industrial appearance or to complement the surrounding environment with a neutral grey. Though HDG coatings provide a unique esthetic, there are ways to alter its appearance for projects where a desired sheen or colour is an important attribute of the overall design.
Newly galvanized parts will dull slowly as they weather naturally in the environment, but a prematurely matte surface is achieved by applying a zinc-phosphate conversion coating. This procedure is typically used for rural environments or wilderness areas where surface reflectivity must be reduced prior to installation for safety or environmental concerns. Some galvanizing plants can dull the coating using an immersion process, but a spray or immersion application may also be performed by a third party.
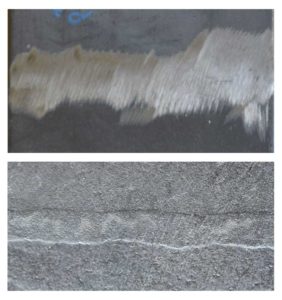
To alter colouration of the galvanized coating while preserving other interesting visual aspects of the metallic coating, metal surface treatments can provide a distinctive alternative. These post-galvanizing treatments do not affect the corrosion protection and are applied either by immersion in solution or spray application. For example, a natural earth tone can be achieved to blend galvanized components within a natural landscape by applying a colour treatment to react with the zinc surface to develop a mottled and rustic, brown finish often associated with a historical esthetic. The final effect is often compared to weathering steel. Where a more vibrant colour is preferred, other passivation technologies, such as polymer-based, waterborne products specifically designed for use over zinc surfaces, can be spray applied. They dry within seconds to offer long-lasting translucent colours in a variety of hues (Figure 5). Due to the variety of initial appearances that are possible, it is impossible to guarantee spangles or other features will be visible underneath a translucent surface treatment.
A duplex system: Painting or powder-coating over galvanizing
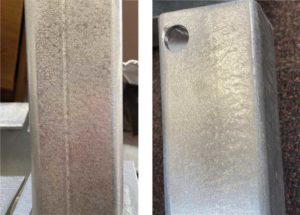
Where a certain colour other than a natural, grey metallic is preferred, the HDG coating may be painted or powder-coated, known as a duplex system. In addition to a specified hue and texture, duplex systems provide improved longevity, 1.5 to 2.3 times the combined lifetimes of both systems, as the result of a synergistic effect between the coatings. The paint or powder-coating should be specified based on the intended use of the part, application method, environmental concerns, and the desired appearance. For assistance in evaluating the available options designed to work well over hot-dip galvanized surfaces, it is best to consult a paint manufacturer directly or reference the Society for Protective Coating (SSPC) Guide 19, Selection of Protective Coatings For Use Over Galvanized Substrates. SSPC Guide 19 is a valuable resource to guide specifiers in selecting an appropriate liquid coating system for the duplex system.
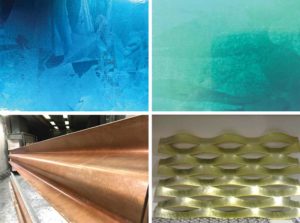
Surface preparation is the most important step in ensuring the appearance and overall performance of painted or powder-coated HDG steel meets the desired expectations. The following standards clarify the steps necessary to prepare the galvanized surface for a wide range of liquid coating systems:
ASTM D6386, Practice for Preparation of Zinc (Hot-dip Galvanized) Coated Iron and Steel Product and Hardware Surfaces for Painting; and
ASTM D7803, Practice for Preparation of Zinc (Hot-dip Galvanized) Coated Iron and Steel Product and Hardware Surfaces for Powder Coating.
After coating selection and preparation of the hot-dip galvanized surface, the paint or powder-coating should always be mixed, applied, and cured in accordance with the manufacturer’s instructions.