Improving the appearance of hot-dip galvanized steel
Refining the appearance of HDG steel
The engineer and/or architect often have the greatest influence on the appearance of the HDG coating; much more than the galvanizer. Specification and design practices are highly influential on the initial and final appearance of the coating as well as the overall quality. This makes it important for the design professional to communicate the intended use of the product with the galvanizer and fabricator early in the project to ensure expectations are set and responsibilities are clearly defined.
The final appearance and finish requirements for HDG coatings are provided in ASTM A123, Standard Specification for Zinc (Hot-dip Galvanized) Coatings on Iron and Steel Products. Prior to the 2018 revision, Canadian standard CSA G164, Hot Dip Galvanizing of Irregularly Shaped Articles, provided an alternative specification for general galvanizing but the standard now applies only to products intended for use in electrical and communication systems. As ASTM A123 was not originally intended to provide an esthetic finish, many natural and common surface conditions (i.e. runs, inclusions, roughness, or excess zinc) are acceptable under this standard if they do not affect the corrosion protection of the coating or intended use of the product. These allowances cause many specifiers to believe elevated esthetics cannot be achieved for artistic designs and architectural members. In reality, these surface conditions can be reasonably ground, sanded, or filed after galvanizing to minimize their appearance, improve uniformity, and achieve a desired look for featured or showcase elements (i.e. architecturally exposed structural steel [AESS], façades, etc.). Further, designers have the option to specify additional design, fabrication, and coating requirements known to improve overall appearance while minimizing time and cost for smoothing after galvanizing.
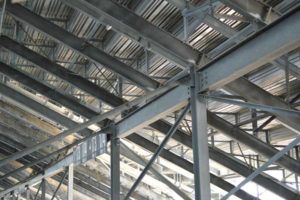
For architects, the Canadian Institute of Steel Construction (CISC) Category Matrix for Specifying Architecturally Exposed Structural Steel (AESS) is recommended to communicate the desired esthetic for AESS members requiring heightened esthetics for surfaces and connections. Any combination of exceptions and/or increased requirements for hot-dip galvanizing should be defined using the Custom Elements (C) category based on viewing distance, function, and cost. To assist specifiers with defining Custom Elements for hot-dip galvanized members within the CISC AESS Category Matrix, AGA offers a free publication, Hot-Dip Galvanized Architecturally Exposed Structural Steel Guide, available at galvanizeit.org/AESS.
If a project’s design requirements go above and beyond ASTM A123 appearance and finish mandates, they must be clearly communicated to both the fabricator and galvanizer. Opening direct lines of communication early in the design process provides the best chance for improved appearance. For example, design professionals can work directly with galvanizers to optimize placement, quantity, and size of venting/drainage holes beyond the minimum requirements to avoid runs and clogs of zinc (Figure 3).
For any welded assemblies, esthetics near the weld area similarly benefit from a greater attention to detail. Welding electrodes containing high silicon (> 0.25 per cent Si) can cause thick and dark coatings in the area even if the weld is ground flat before galvanizing. Low-silicon welding electrodes can be specified to avoid a swollen appearance, but availability may be uncommon for some welding processes (e.g. gas-shielded flux cored arc welding [FCAW-G]). The additional effort to grind and file welds, hollow structural section (HSS) seams, mill markings, and other raised surface conditions will minimize their appearance after hot-dip galvanizing, but are unlikely to eliminate them (Figure 4).
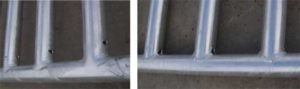
At an additional cost, design professionals may also recommend a commercial blast cleaning prior to hot-dip galvanizing to improve overall aesthetics, reduce the occurrence of thick and brittle coatings, and promote a more uniform appearance across assemblies containing different steel compositions and initial surface conditions.
Touch-up and repair materials
If the coating is damaged after hot-dip galvanizing, it is possible to specify a repair method to maximize esthetics. ASTM A780, Practice for Repair of Damaged and Uncoated Areas of Hot-dip Galvanized Coatings, lists the following three methods for repair:
∞ zinc-based solder;
∞ zinc-rich paint; and
∞ thermal-sprayed zinc (zinc metallizing).
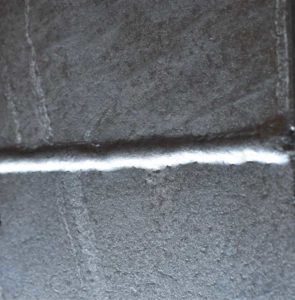
Zinc-based solders and thermal-sprayed zinc more closely match the appearance of galvanizing, but there are some limitations in addition to a higher investment. Zinc-rich paints economically provide suitable esthetics if a matte grey one is utilized because the base galvanizing will weather to a similar colour over time. A shiny or silver repair paint provides a more uniform appearance initially, but results in a permanent mixed appearance upon natural weathering of the galvanizing.
Although not an exhaustive list of additional methods to improve the appearance of batch, HDG products, the above tend to have the greatest impact beyond the design details available in ASTM A385. To help specifiers navigate other design and fabrication best practices for galvanizing, the American Galvanizers Association (AGA) provides the free publication, Design of Products to be Hot-Dip Galvanized After Fabrication.