Improving continuous insulation
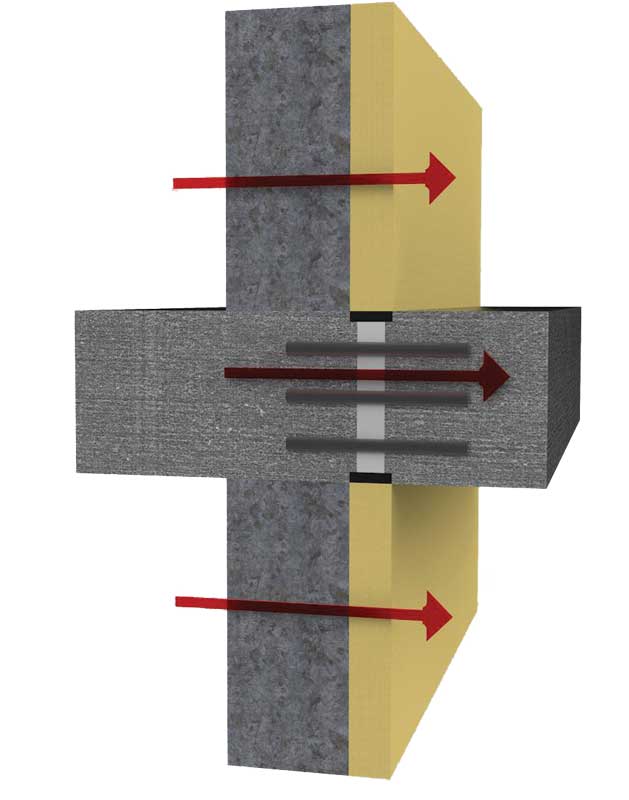
The Morrison Hershfield study done for the EIFS Council of Canada stresses that design at windows’ terminations should be carefully considered. The position of windows in the wall and how they align with the EIFS insulation can affect the assembly’s overall performance. Detailing the window inbound of the insulation, supported on the wall framing, has a linear transmittance of 0.35 W/m•K. Wrapping the rough opening with insulation, or moving the window so the thermal break is in alignment with the insulation, significantly improves performance to 0.2 W/m•K. (It is important to note the Morrison Hershfield calculations for the EIFS ‘clear wall’ included a geometrically defined drainage cavity [GDDC].)
EIFS terminated at a cantilevered concrete deck cannot stop heat loss through the slab. However, adding thermal breaks in the slab and aligning them with the continuous insulation will have an impact on wall performance, as shown in Figure 6. The study shows the linear transmittance improvement from an uninsulated floor slab (i.e. 1.0 W/m•K) to one with a thermal break (i.e. 0.35 W/m•K) is significant. This would be true for all claddings.
Implementation
Just as advances in computer modelling have led to a new level of building science savvy, so too have the advancing computer analyses of global warming trends continued to clarify the big picture. As data accumulates, the question of “What’s happening?” is being answered with greater accuracy, and the questions “What can we do?” and “What must we do?” are beginning to merge. (For some thought-provoking comparisons on the total energy increase resulting from a mere 2-C [3.6-F] temperature rise, visit www.skepticalscience.com/4-Hiroshima-bombs-worth-of-heat-per-second.html.)
Late last year, Canada was one of 175 countries to sign the Paris Agreement, committing to take action on climate change. Keeping global temperature rise below 1.5 C (2.7 F) was accepted as “an aspirational goal.” In North America, buildings are a leading energy-user and hence a primary target for energy conservation measures. Effective continuous insulation, working hand in hand with air leakage reduction, is the primary prerequisite. (Airtight construction is a code requirement, and necessary for any insulated wall to function as designed. The information in this article assumes airtight construction.) This will produce the best energy reduction for the most effective cost. When the envelope is tight and insulated, other building systems may be addressed.
A study conducted by McKinsey & Company compares the effectiveness of implementing an energy strategy with the cost of undertaking that strategy. (The 2009 report, “Pathways to a Low-Carbon Economy, Version 2 of the Global Greenhouse Gas Abatement Cost Curve,” is online at www.mckinsey.com/business-functions/sustainability-and-resource-productivity/our-insights/pathways-to-a-low-carbon-economy.) If a methodology is effective in reducing greenhouse gas (GHG) emissions and saves money, it is an obvious place to start. In general terms, conserving or reducing energy use tends to be more cost-effective than developing new carbon-free sources. Specifically, the act of insulating buildings, especially retrofits, ranks high in the global GHG abatement cost curve.
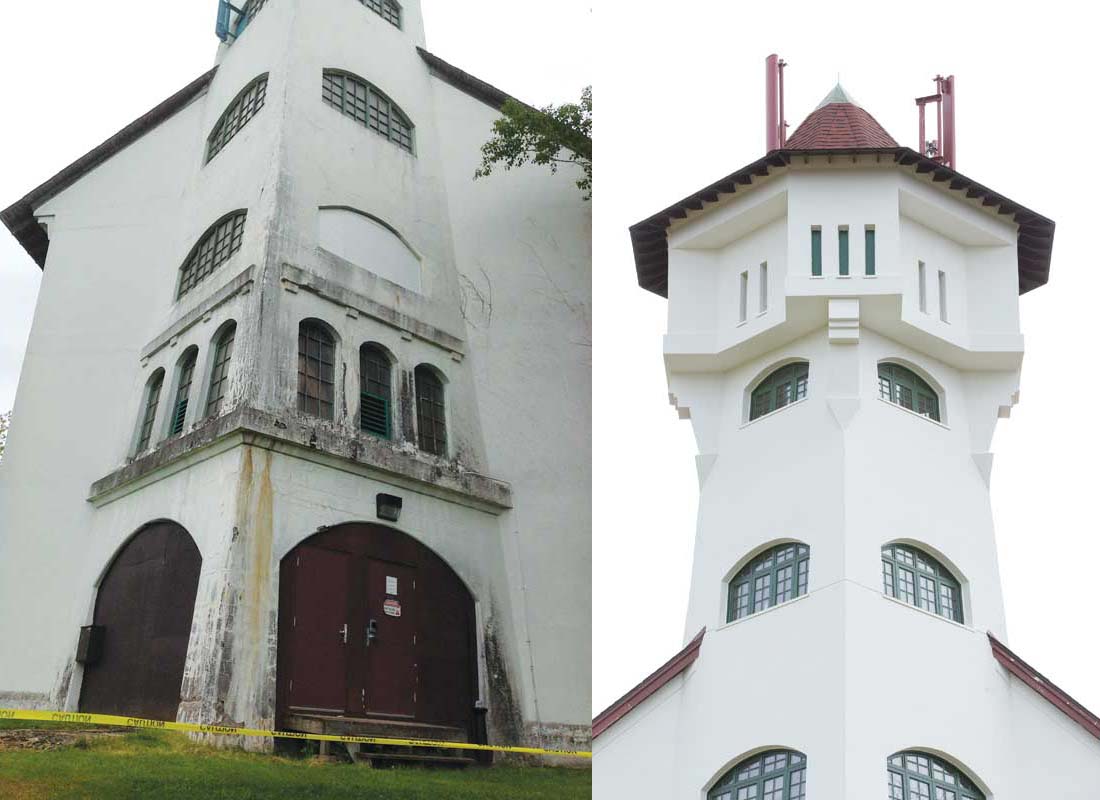
Among recent Canadian examples of using insulation creatively to improve performance, the Algonquin Hotel (St. Andrews, N.B.) is a stand-out. The iconic century-old hotel used to close down every fall because it was uninsulated. In a recent retrofit, the exterior was completely wrapped in an airtight blanket assembly designed to look exactly like the original Tudor stucco design. The hotel now operates year-round (Figure 7).
There are many good reasons to improve the thermal efficiency of buildings. From a business perspective, the modest increase in capital cost has a long-term benefit of reducing operational expenses. An effectively insulated building has more protection from rising energy costs.
International commitment to action is now being translated into change for the construction industry. The Canadian government has signed a $40-million contract with National Research Council (NRC) to rewrite building codes to meet energy conservation goals. The Ontario government has introduced the Ontario Climate Change Action Plan to tackle greenhouse gas reduction. Electric cars attract the media spotlight, but enforcement of new building and energy codes is going steadily forward. Already announced, the Ontario energy code, SB-10, requires a 13 per cent energy performance improvement.
If this level of improvement seems hard to achieve, then it is important to watch out for the Ontario Climate Change Action Plan, which will target an 80 per cent reduction in GHG emissions by 2050. Further, design professionals can look forward to building commissioning and labelling similar to that done in Europe. To start the process, proposed Ontario Bill 135 amends the Energy Statute Act to require reporting of greenhouse gas emissions. The public will know which buildings perform well and which do not. Inevitably, that information will affect leasing and resale values. Cities like Vancouver, Calgary, and Toronto are working hard at the municipal level to create ‘stretch codes’ because, like Canada’s commitment to the Paris Agreement, the industry will have to stretch to meet them. For example, the Toronto Green Standard requirements will be 15 per cent tighter than the province’s SB-10.
When the nations of the world agree to do something to save the planet, and a significant part of that ‘something’ concerns the built environment, our industry becomes a vital participant in the agreement. We are on the front lines of GHG emission reduction, and we can make change happen.
John Edgar is president of John R. S. Edgar Consulting Inc., and past-chair of the Exterior Insulation and Finish System (EIFS) Council of Canada. He is convener of ISO TC163 SC03 TG09, preparing three new international standards for EIFS. Edgar has held positions including technical director at Sto Canada, member of the National Building Code of Canada (NBC) Standing Committee on Environmental Separation (part 5), and chair of Underwriters Laboratories of Canada S716 Task Group for EIFS. He can be reached at john@johnrsedgar.com.