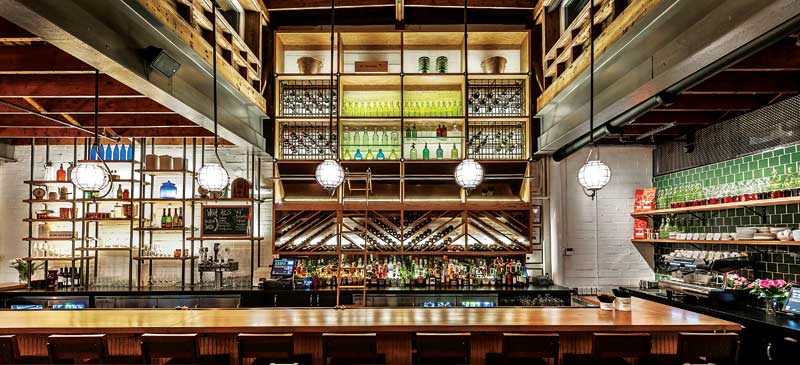
By Drew Parks
The creation of drawings and specifications for any construction project is a complicated business. First, the general conditions must be outlined, all appropriate references identified, and contractual obligations listed. Then, each section must clearly inform the bidder of the scope of work and its specifications. If a specifier wants to retain sanity in this process, every resource that can add credibility and accuracy to their document must be accessed and mined.
The content in many sections of bid documents is already benefiting from collaborations with the affiliated trade—structural, electrical, mechanical, and door hardware professionals all provide much needed input and follow up inspections to ensure the quality of the bid documents and the finished product. The architect and specifier cannot be expected to be experts on every aspect of building construction. Their job should be to create the vision, identify the detailing requirements, and corral the trade expertise needed to put their vision on paper for bidding and fabrication.
One area of the building finishes, for which available resources have not been fully tapped by the specifier, is the interior product collectively known as ‘millwork.’ Such materials are identified in the architectural woodwork, laminates, panelling, wood doors, and laboratory cabinet sections of MasterFormat—respectively, 06 41 00, 06 42 00, 06 46 00, 08 14 00, and 12 35 53. The items governed by these sections are often the first things seen when entering a lobby, boardroom, store, suite, or office. They are one of the principal elements that contribute to ‘first impressions’ and quality assessments.
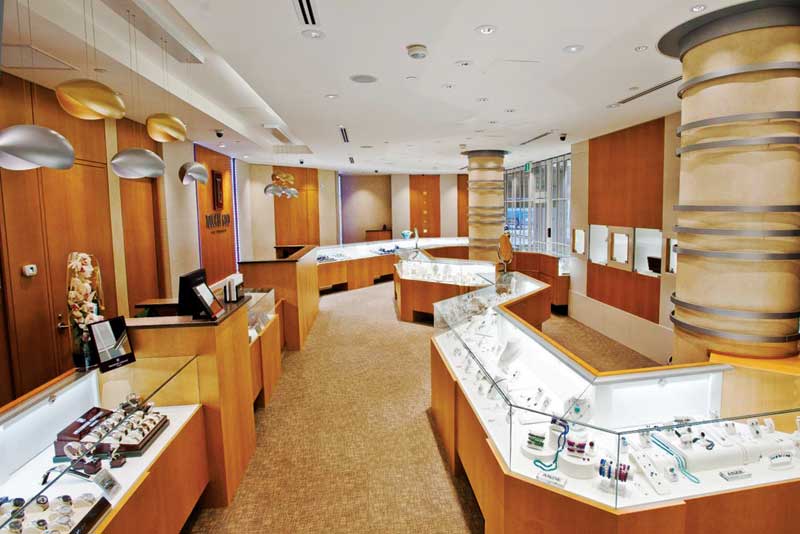
Photo courtesy RCS Construction Inc.
Unfortunately, the writing of these sections is often a source of frustration for the specifier. Accurate material and construction details are difficult to nail down, and clear identification of these elements in the bid drawings and specifications is a time-consuming process. Inconsistencies in the final specifications and drawings can plague the architectural firm, general contractor, and millwork firm throughout the bid and building process.
This article examines how resources from the Architectural Woodwork Manufacturers of Canada (AWMAC) can help design/construction professionals in this regard. The goals are:
- less work for the specification writer and for the plans draftsperson;
- more concise and accurate bid specifications as well as drawings;
- fewer questions and addenda before bid closing;
- bid proposals on a relatively level playing field and based on the production of a good-quality product;
- extended life expectancy for properly installed products; and
- securement of a two-year guarantee on the millwork components of your project.
Understanding millwork’s evolution
Millwork production and installation has changed dramatically over the last generation. Once the domain of the finish carpenter, the trade now comprises a team of specialists:
- estimators;
- shop drawing technicians;
- computer numerically controlled (CNC) equipment programmers;
- machine operators;
- cabinetmakers;
- shop finish applicators;
- site installation crews; and
- project managers.
The manufacturing facility has evolved from the backyard shed or garage to larger industrial spaces filled with CNC machinery. The capability of the local manufacturing process has also evolved. It was not that long ago that low-tech manufacturing methods restricted the buyer to simple design and materials. Unique elements resulted in extra costs generated by labour-intense processes and limited access to ‘special’ materials. For years, complicated features such as carved elements, large interconnected pieces, multiple colour patterns, and inlay designs were only available with a large price tag. Today, the availability of new and reimagined materials and the detail and speed of computerized machinery has opened the door to ‘sky-is-the-limit’ design.
For the specifier, the downside of this new design opportunity and industry change becomes the complications of getting the vision details recorded in words and drawings for the bid process and, ultimately, in the translation of those specifications into the final installed product. The architect and specifier are expected to control all aspects of the building design, from foundations to finishes. The idea the architect, designer, and specifier can also be trade experts who understand all the intricacies inherent to each discipline is simply unrealistic.
Each qualified tradesperson has tens of thousands of hours of training and work experience; each trade’s business place usually relies on specialists within its own ranks. To adapt to this reality, the specifier community has developed links with the individual trades—consultants, inspectors, and engineers—to ensure the myriad details are looked after and a good product is controlled and produced for the owner.