Identifying green buildings that work
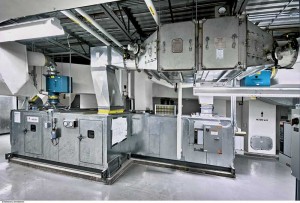
A rooftop energy recovery ventilator (ERV) and a true underfloor displacement ventilation system supply 100 per cent outside air to floor grilles in the runway around the main floor and mezzanine retail area. In winter, ventilation air is pre-conditioned by the ERV, then further warmed by hot water pipes wrapped around the underfloor ducts set in the radiant heated floor. All spaces are heated by hot water radiant floors and two modulating condensing gas boilers.
MEC Burlington’s actual energy use is 188 kWh/m2 (17.5 kWh/sf)—56 per cent less energy than a conventional building.
Other sustainable features include:
- two rainwater cisterns—one that collects stormwater runoff from the parking lot for irrigation and the other that collects rainwater from the roof for toilet flushing;
- the building is designed for simple disassembly and material recycling or reuse; and
- the structure is made of wood—a renewable resource—97 per cent of which is from Forest Stewardship Council (FSC)-certified sources.
Le Tournant School
Although one of the lowest energy users of Canadian commercial/institutional buildings at 281 kWh/m2 (26 kWh/sf), prospective green schools have their own challenges, such as strict construction budgets and rigid, traditional design rules.
In the facility’s water loop heat pump system, heat is added to the water loop using a condensing boiler and rejected from the water loop with a dry cooling tower. Each water-to-air heat pump, distributed throughout the office ceiling space, responds only to the heating or cooling load of the zone it serves. This zoning provides excellent comfort levels for occupants, better control of energy use for building owners, and lower seasonal operating costs.
Completed in 2002, the 2682-m2 (28,869-sf) Le Tournant School in St. Consant, Que., serves 220 students. With an Energy Star score of 90, it is one of the most energy-efficient schools in the country, using 72 kWh/m2 (7 kWh/sf)—a reduction of 74 per cent. These results were achieved by using simple, tested methods.
A high-performance building envelope with an optimal WWR set the stage for the rest of the high-performance design. The asphalted areas are away from the building, and careful planting was used to encourage heat gain in winter and block the sun in summer. Even the brick colour was selected to optimize absorption.
The mechanical engineering option selected was a closed-loop geothermal system. A mix of methanol circulating through 5 km (3 mi) of pipe connecting to 18 independent wells transfers heat to and from the ground. In winter, heat from the ground is transferred to the school, and in summer, heat from the school is returned to the ground. Depending on the weather conditions, the system selects one of the two air intakes which, during the heating period, pass behind one of the two solar walls (a plain black perforated plate) and benefit from substantial heat gain. The fresh air intake rate is regulated by a carbon dioxide (CO2) sensor.
To prevent heat loss, a thermal tube heat exchanger is also used to warm intake air from the outside using the heat extracted from evacuated stale air. Inside the building, heating and air-conditioning are ensured by 25 heat pumps. An electric coil can provide backup if necessary. Electricity use is reduced to the minimum so even though the heating coil runs on fossil fuel, the impact on CO2 emissions is negligible.
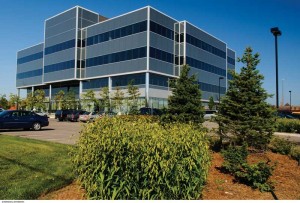
Ventilation and lighting are linked to presence sensors, and the control of all school systems is centralized and can be remotely monitored.
With the help of a subsidy from the federal government equal to twice the expected annual savings, the budget granted by the Québec Ministry of Education, Recreation, and Sports was exceeded by only 10 per cent. One could speculate on a larger-scale project, the cost overrun would be even less. At current energy prices, the additional cost was recovered by 2011.
3115 Harvester Road
The office is the most common type of Canadian commercial building, using an average of 394 kWh/m2 (37 kWh/sf). The target for energy reductions for the Green Buildings that Work database is 60 per cent for offices.
This five-storey, LEED Silver speculative office (Speculative offices are workspaces built for unknown tenants to rent as opposed to being built for a particular tenant or by the owner). in Burlington, Ont., demonstrates green buildings and energy savings are not necessarily synonymous with a high design and construction premium. Created on a comparable budget to other spec offices, this project achieved an Energy Star score of 88 because its actual energy consumption is 134 kWh/m2 (12 kWh/sf), and its use reduction is 66 per cent.
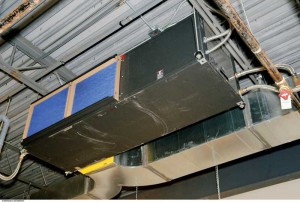
The energy-saving measures implemented in the project, 3115 Harvester Road, include heat pumps, demand-controlled ventilation, and an efficient lighting design. The building shell is often sacrificed in primarily glass buildings. This building features a high-performance curtain wall with a low-emissivity (low-e) coating, argon-filled gaps, and warm-edge spacers. The roof is well-insulated at R-25 (i.e. RSI-4).
The energy recovery ventilation units for this project achieved 76 per cent efficiency on energy recovery. Another improvement in this building regarding energy efficiency is its demand-controlled ventilation in meeting rooms. In these rooms, CO2 sensors on the wall monitor the number of people in the room and increase or decrease the amount of fresh air brought into the space accordingly. This not only saves energy by providing a decreased ventilation rate when the rooms are not in use, but improves indoor air quality (IAQ)—especially when a meeting room is full.
An efficient lighting plan minimizes the amount of lighting power density needed in the space. Occupancy sensors are used to only turn on lights when someone is in that room. The building only uses 9 W/m2 (0.8 W/sf).
Low-flow plumbing fixtures for toilets, urinals, and faucets supplied by a rainwater cistern helped the building achieve an indoor water use of 11 L (2.9 gal) per person—a 60 per cent reduction.
Conclusion
Over the past seven years or so, Canadian design teams have shown green buildings can be exciting, attractive contributions to the built environment. The next step is to prove green buildings are actually using significantly less energy than conventionally designed ones. This does not need to be an expensive challenge or require new technologies. The best buildings in Canada today—green buildings that work—use simple engineering strategies, good basic design principles, and on-the-market, proven technologies to create superior performance results.
Stephen Carpenter, P.Eng., is president of green building consulting firm, Enermodal Engineering–a member of MMM Group. Operating since 1980, Enermodal has certified more than 100 Leadership in Energy and Environmental Design (LEED) Canada projects through its offices across the country. Carpenter can be reached at info@enermodal.com.