ICFs, wood, and the changing face of mid-rises
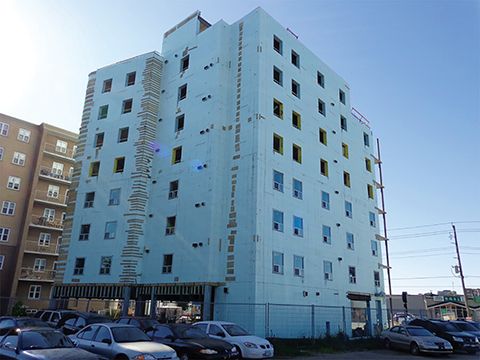
Fire performance
Both wood framing and ICFs require fire suppression design for the occupants, but a bigger concern has been a recent series of construction fires in highly developed urban areas. The move to a six-storey wood-frame building has added requirements for protecting the sites during construction, such as the proposed guideline in Ontario to require a security guard onsite whenever the crew is not present.This is further complicated when additional combustible external insulation is added, pushing some fire authorities to require non-combustible protection of theses surfaces during the construction.
This requirement also impacts the EPS surface of ICFs, as that material is classified as combustible. This means ICFs stored onsite must be protected from any fire safety concerns.
Insulation and thermal performance
Canadian building codes for six-storey structures have historically specified the required nominal R-values of the individual building components themselves, without accounting for thermal bridging within the overall wall assembly.
A thermal bridge is an area of a wall that has a significantly higher heat transfer than the surrounding materials; the result is an overall reduction in the assembly’s effective thermal performance.
Canadian codes are now based on the total effective R-value of the entire wall, which requires additional insulation to be added to meet the new requirements for systems with significant thermal bridging, such as wood-frame construction. Under the 2011 National Energy Code for Buildings (NECB), for example, the whole-wall R-value requirements for above-grade walls are now:
- R-18 for Climate Zone 4;
- R-20.4 for Climate Zone 5;
- R-23 for Climate Zone 6; and
- R-27 for Climate Zone 7.
Most of the wood-frame mid-rise buildings have so far been constructed in Climate Zone 4 in temperate British Columbia, which requires an effective R-18 for above-grade walls. As wood-frame construction enters the colder regions of the country, increased R-values and amounts of insulation will be required.
Sufficient wall cavity capacity to hold insulation then becomes an issue with the a framing factor of 30 to 40 per cent, which is typically what is required for mid-rise wood framing. (As a comparison, the typical framing factor in residential construction is about 25 per cent.) This will lend itself to more insulation being fastened to on the outside of the wall, which, in turn, adds to installation labour and time requirements.
ICFs inherently have foam panel insulation on both the interior and exterior surfaces. The wall assembly R-value of some ICF brands is in the R-23 to R-25 range. Some ICF systems in the market may adapt their product to the increasing R-value requirements by developing products that have thicker forms—some equally on both sides, and others with an increase on one side. Other ICF technologies use a higher R-value EPS bead to hit the R-27 target.
Generally speaking, the new thermal performance requirements have resulted in some increase in cost for wood-frame mid-rises in all climate zones, and for ICF-built mid-rises in Climate Zone 7.
An additional thermal performance element to be considered is the thermal mass of the wall system. This is a material’s ability to absorb and store heat energy. A lot of heat is required to change the temperature of high-density materials like concrete, brick, and tiles. They have high thermal mass, whereas lighter materials—such as wood studs—have low thermal mass.
Although the thermal mass effect is difficult to model, enhanced building thermal performance (including controlling of heating and cooling peaks) in ICF buildings can be seen.