ICFs and the new green standards
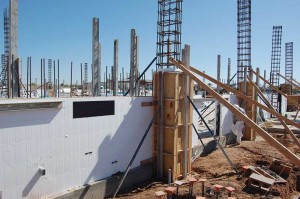
Right now, trial versions of the credits to be added to the new LEED 2012 are available to project teams looking for Innovation in Design (ID) credits by selecting one from the library of ‘pilots,’ two in particular of which the ICF industry will be watching to see how well they fare under the new rating system. Both share similar language to the verbiage in the new credits in the rating system’s second public comment draft.
The first of these is Pilot Credit 1, Lifecycle Assessment of Building Assemblies and Materials, which is available to project teams working on LEED NC and Healthcare projects. The credit relies on the Athena EcoCalculator (offered by the Athena Institute, out of Merrickville, Ont.) for calculating and comparing the various material assemblies from a lifecycle assessment (LCA) perspective.
LEED treats an ICF as a portion of the building envelope system or assembly. The LCA practitioner produces an impact score sheet for the assemblies assessed and those results are plugged into the LEED LCA Calculator to generate the documentation a project team needs to continue with the building design process. How the Athena Calculator will be brought into LEED 2012 is expected to be clarified in the final version.
The other credit relevant to ICFs is Pilot Credit 43, Certified Products, in which building materials can either be certified to approved standards, or manufacturers can offer product data in approved formats. Either way, the proposed credit would reward project teams with one point for a green product with a label verifying the product has been third-party-certified for at least a single sustainable product attribute, while the credit leaves product performance to be captured somewhere else in LEED. This pilot credit also refers to another USGBC document under development—“LEED Standard for Standards.”
Energy efficiency
The energy efficiency of ICF walls are well-documented in studies and research by the Portland Cement Association (PCA) and CTL Group consultants, (For an example, see the article, “Concrete’s Mass Appeal for Energy: A Look at LEED EA Credit 1 Across Five Climates,” by Martha G. VanGeem, PE, ASHRAE, LEED AP, and Medgar L. Marceau, PR, CSI, ASHRAE, LEED AP, in the November 2008 issue of The Construction Specifier. Visit www.constructionspecifier.com and select “Archives.”) as well as in ongoing research projects by the U.S. National Association of Home Builders (NAHB) under the Program for Advanced Technology in Housing (PATH) and the Oak Ridge National Laboratory (ORNL).
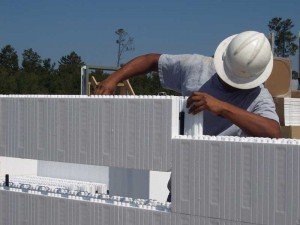
per cent compared to wood frame homes over a 60-year lifecycle.
The baseline building performance measurement is calculated with Appendix G of American National Standards Institute (ANSI)/ASHRAE/IESNA 90.1-2010, Energy Standard for Buildings Except Low-rise Residential Buildings, using a computer simulation model for the whole building project. Further details of the requirements for this calculation are listed in the prerequisite within LEED’s Energy and Atmosphere (EA) category.
In the new LEED 2012 EA category, available credits will be reduced, with some being shifted to the new Performance (PF) category. This is a change reflecting an emphasis on measuring energy efficiency after initial certification. The EA credits moved to Performance are concerned with measurement, performance, and verification over the project’s life. Contained in the changes to Energy and Atmosphere, as well as the new Performance category, are opportunities for projects using ICFs to retain and even expand possible credits toward LEED certification.
Additionally, research has shown the thermal mass of an ICF building envelope would fare better during the energy modelling portion of the commissioning for an easier time in passing testing and verification benchmarks details in ASHRAE 90.1, especially compared to wood or steel construction.3
Concrete and ICFs
In LEED 2012, the Materials and Resources (MR) category will be overhauled from a building materials and products manufacturer’s perspective. Design professionals will have to relearn the compliance pathways for gaining points through the MR category, and manufacturers will need to update their documentation to reflect the changes.
Several credits are new and others have been eliminated in an attempt to reward LEED project teams for specifying materials on a lifecycle basis, rather than just single sustainable attributes. In fact, products that once contributed to multiple LEED credits—such as recycled or regional content—can now only contribute additional points if they have third-party certification or can document their product’s reduced environmental impact through an LCA.
Relevant to ICF systems, instead of LEED 2009’s MR Credit 1, Building Reuse–Maintain Existing Walls, Floors, and Roof, USGBC has developed a new MR Credit 1, Environmentally Preferable Structure and Enclosure. It gives project teams various options, among which is the exclusion of fly ash in concrete as a substitute for cement and as recycled content (but only for healthcare projects). It also requires an LCA of any major structural elements reused in new construction projects, as well as any exterior portions of the building dividing the conditioned space from the outside.
A forthcoming BD+C LEED 2012 Reference Guide will further explain the specifics, including the design parameter methodology for the LCA. Additionally, the new LEED will require reuse of structural enclosure materials to be “better than average” when compared to the USGBC’s stated “highest value impact categories” within an LCA, including Climate Change, Human Health, and Water (consumption and pollution). Further, waste from municipal solid waste cannot qualify as recycled content if the project team seeks to earn this credit. ICFs will be better than many comparable structural systems due to their lower global warming potential (GWP) over 60 years, as discussed later in this article.
In cases where the building will be reused, much remains the same as the LEED 2009 MR Credit 1, except the threshold is higher for three points as 90 per cent reuse is now the new benchmark. The remainder of the new MR Credit 1 asks project teams to source materials locally when possible. There are also guidelines for reuse of historic buildings or abandoned structures in typically blighted areas; ICF durability can play a role here, too.
Since ICF walls are a major portion of the building envelope, the system can be considered part of the calculation for reuse credits in LEED for MR Credit 1, as it can be a load-bearing portion of the supporting building systems.
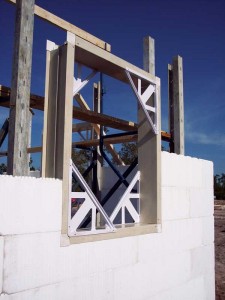
USGBC has indicated it believes LCA has its limits. Therefore, the council has introduced additional criteria relevant to ICF walls such as MR Credit 5, Responsible Sourcing of Raw Materials, which looks for a commitment by manufacturers mining raw materials to support programs such as the Framework for Responsible Mining. This credit has relevance for the ICF industry since one of the main ingredients of the system is concrete.
Lifecycle analysis of concrete
While much is made of ICF benefits to conserve energy consumed by buildings, the LCA of concrete buildings published by the Massachusetts Institute of Technology (MIT) Concrete Sustainability Hub, in its 2011 report, “Methods, Impacts, and Opportunities in the Concrete Building Lifecycle” showed ICF homes can reduce a structure’s GWP compared to light-wood-framed single-family homes. Visit www.think-harder.org/MITResearch.aspx This report is perhaps the best indicator of how insulating concrete forms for commercial new construction and renovations can have a positive impact.
The research was undertaken because the manufacturing of portland cement is very energy-intensive, and the report helped dispel some myths about concrete’s sustainability. It also showed buildings generally consume the most energy while occupied; therefore, this stage of the lifecycle is responsible for 88 to 98 per cent of the GWP emissions. Initially, all building types in the report had very similar emissions over a 60-year lifecycle when concrete construction was compared to steel and wood construction in different U.S. climates. The addition of fly ash then further helped reduce concrete’s environmental impact. The authors concluded:
Although the concrete homes have higher initial embodied emissions than light-frame wood construction, the lower annual operating emissions means that the emissions of concrete houses are lower over a 60-year period… The cumulative emissions of the ICF houses are 4.7 per cent lower in Chicago and eight per cent lower in Phoenix than the equivalent light-frame wood house.
Energy loss impacts finite resources. Insulating concrete forms have a high resistance to heat flow and, when correctly specified and installed, reduce energy usage. Lowering energy consumption reduces not only the owner/tenant’s utility bill, but also the built environment’s carbon footprint.
As these aspects of ICFs become more salient (due to codes, standards, and increased awareness), they will become better documented candidates for the building envelope on a rising number of construction projects.
Paul Nutcher, CSI, CDT, is president of Green Apple Group, LLC. He has nine years of building industry experience as a marketing and sustainability consultant. Nutcher can be contacted at pnutcher@greenappleconsult.com.